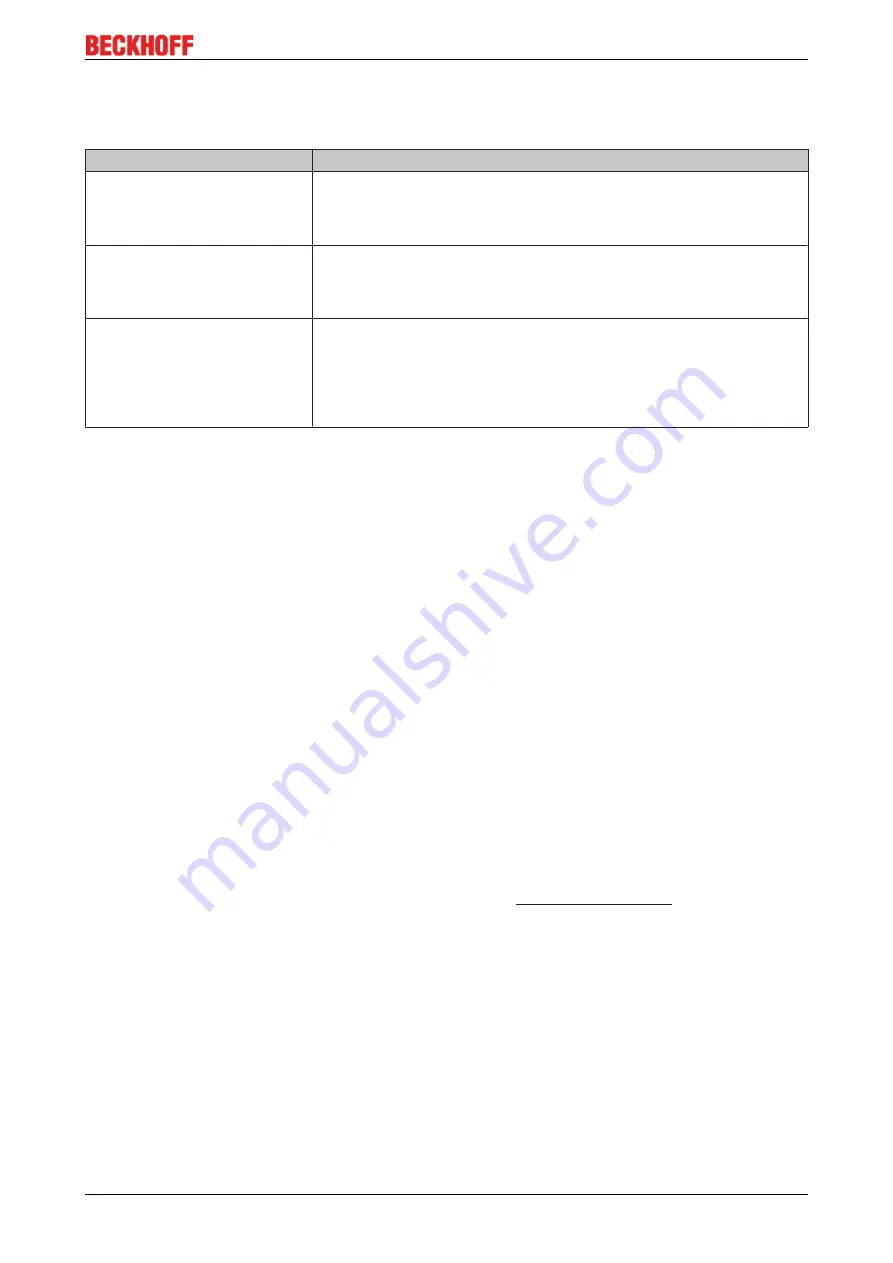
PROFIBUS
BC3150
79
Version: 2.1.0
contain the number of stations, the assignment of the station addresses to the I/O addresses, data
consistency of the I/O data and the format of the diagnostic messages and the bus parameters being used.
Every PROFIBUS DP system consists of different device types. Three types of device are distinguished:
Class
Description
DP master class 1 (DPM1)
e.g. Beckhoff FC310x:
PROFIBUS master card for PCs
This involves a central controller that exchanges information cyclically
with the decentralized stations (slaves) in a specified message cycle.
Typical devices include, for instance, programmable logic controllers
(PLCs) or PCs.
DP master class 2 (DPM2)
Devices of this type are engineering, project design or operating devices.
They are used for commissioning, for servicing and diagnosis in order to
configure the connected devices, to evaluate measured values and
parameters and to interrogate the status of devices.
DP slave
e.g. Beckhoff IPxxxx-B310:
Fieldbus Box for PROFIBUS
A PROFIBUS DP slave is a peripheral device (I/O, drive, measuring
transducer, etc.) that reads input information and passes output
information on to the peripherals. It is also possible to have devices that
only handle either input or output information. The quantity of input and
output information is device-dependent, and may not exceed 246 bytes of
input data and 246 bytes of output data.
Mono master systems
In single master systems only one master is active on the bus in the operating phase of the bus system. The
PLC controller is the central control component. The decentralized slaves are coupled to the PLC controller
via the transmission medium. The shortest bus cycle time is achieved with this system configuration.
Multi-Master Operation
In a multi-master mode there is more than one master on the bus. They either form subsystems that are
independent of one another, each consisting of one DPM1 and the associated slaves, or additional project
design and diagnostic devices. All the DP masters can read the input and output images of the slaves.
Writing the outputs is only possible for one DP master (the one assigned as DPM1 during the project
planning). Multi-master systems achieve a medium bus cycle time. In time-critical applications, the increase
in bus cycle time should be observed by adding a diagnostic tool.
Basic device files (GSD)
In PROFIBUS DP, the performance characteristics of the devices are documented by the manufacturers and
made available to users in the form of a device data sheet and of a basic device file. The structure, content
and coding of these basic device files (GSD) is standardized. They make it easy to plan a project with any
PROFIBUS DP slaves using project planning devices from various manufacturers. The PROFIBUS User
Organization (Profibus Nutzer Organisation - PNO) archives this information for all manufacturers, and will
provide information about the GSD from any manufacturer on request. The GSD files are read by a
PROFIBUS master configuration software, and appropriate adjustments are transferred to the PROFIBUS
master. Please see the appropriate software manual from the master manufacturer for a description.
The Beckhoff GSD files may be obtained from the internet under
Diagnostic functions
The extensive diagnostic functions of PROFIBUS DP allow rapid fault localization. Diagnosis of the Beckhoff
Bus Coupler is not switched on in the default setting of the type file or the GSD file. The diagnostic
messages are transmitted over the bus and collated by the master.
They are divided into three levels: