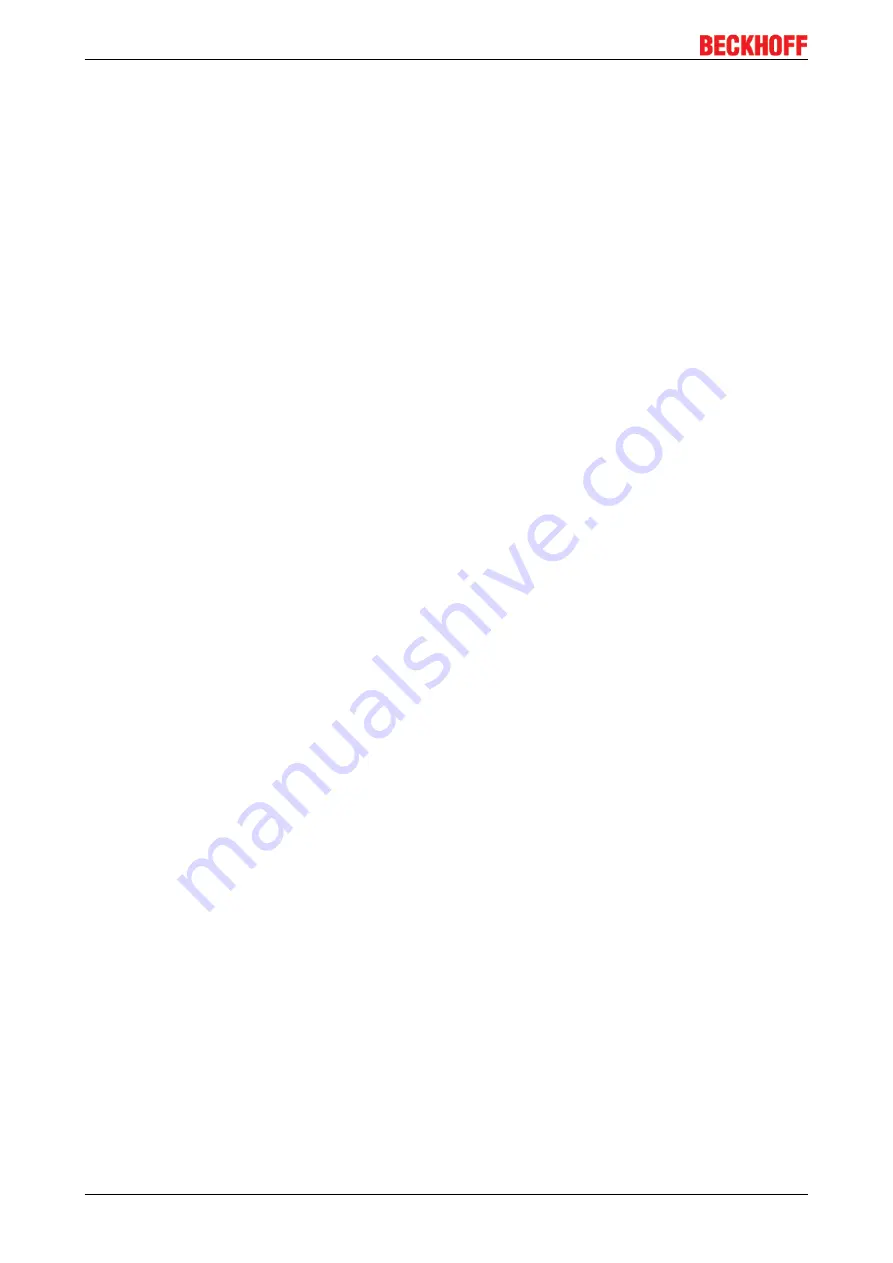
PROFIBUS
BC3150
78
Version: 2.1.0
6
PROFIBUS
6.1
Introduction to the system
6.1.1
Fieldbus Overview
PROFIBUS is a manufacturer - independent, open fieldbus standard with a wide range of applications in
manufacturing and process automation. Manufacturer-independence and openness are guaranteed by the
International standards EN 50170 and EN 50254. PROFIBUS allows devices from different manufacturers to
communicate without the need for specially adapted interfaces. PROFIBUS is suitable both for fast, time-
critical applications and for complex communication tasks.
PROFIBUS offers communication protocols of different functional levels: DP and FMS. According to the
application, RS-485, IEC 1158-2 or optical fiber are available as transmission techniques.
PROFIBUS specifies the technical features of a serial fieldbus system with which distributed digital
automation devices can be networked together, from the field level up to the cell level. PROFIBUS is a multi-
master system, and therefore permits common operation of a number of automation, engineering or
visualization systems with their decentralized peripheral devices on one bus.
PROFIBUS device types
PROFIBUS distinguishes the following device types:
Master devices
determine the data traffic on the bus. A master may transmit messages without having
received an external request when it is in possession of the bus access authorization (token). Masters are
also referred to as active devices.
Slave devices
are peripheral devices such as input/output devices, valves, drives, measuring transducers
and the Beckhoff PROFIBUS slaves from the BK3xx0, BC3xx0, IPxxxx-B310, IL230x-B310 and IL230x-C310
series. They do not receive any bus access authorization, so that they are only allowed to acknowledge
messages that have been received, or to send messages in response to a request from master. Slaves are
referred to as passive devices. They only require a small proportion of the bus protocol, which means that
they can be implemented with little effort.
PROFIBUS DP
PROFIBUS DP is designed for efficient data exchange at the field level. The central automation devices,
e.g. PLC/PC or process control systems, communicate with decentralized field devices such as I/O, drives,
valves etc. via a fast serial link. The data exchange with the decentralized devices is predominantly cyclic.
The communication functions required for this are specified by the basic DP functions conforms to
EN 50170.
In addition to these basic functions, PROFIBUS DP also offers extended acyclic communication services for
such purposes as parameterization and other operations. These are also supported by the Beckhoff
PROFIBUS slaves of the IPxxxx-B310, IL230x-B310 and IL230x-C310 series. A central controller (master)
cyclically reads the input information from the slaves, and writes the output information cyclically to the
slaves. The bus cycle time here should be shorter than the central automation system's program cycle time,
which lies around 10 ms in many applications.
A high data throughput is not in itself sufficient for successful use of a bus system. Ease of handling, good
diagnostic facilities and secure transmission technology are also of the utmost importance if the user's
demands are to be satisfied. These properties are ideally combined in PROFIBUS DP.
System configuration and device types
PROFIBUS DP allows single master or multi-master systems to be implemented. This permits a high level of
flexibility in system configuration. A maximum of 126 devices (master or slaves) can be connected to one
bus. A station address between 0 and 99 can be chosen for the Beckhoff PROFIBUS slaves from
the IPxxxx-B310, IL230x- B310 and IL230x-C310 series. The specifications for the system configuration