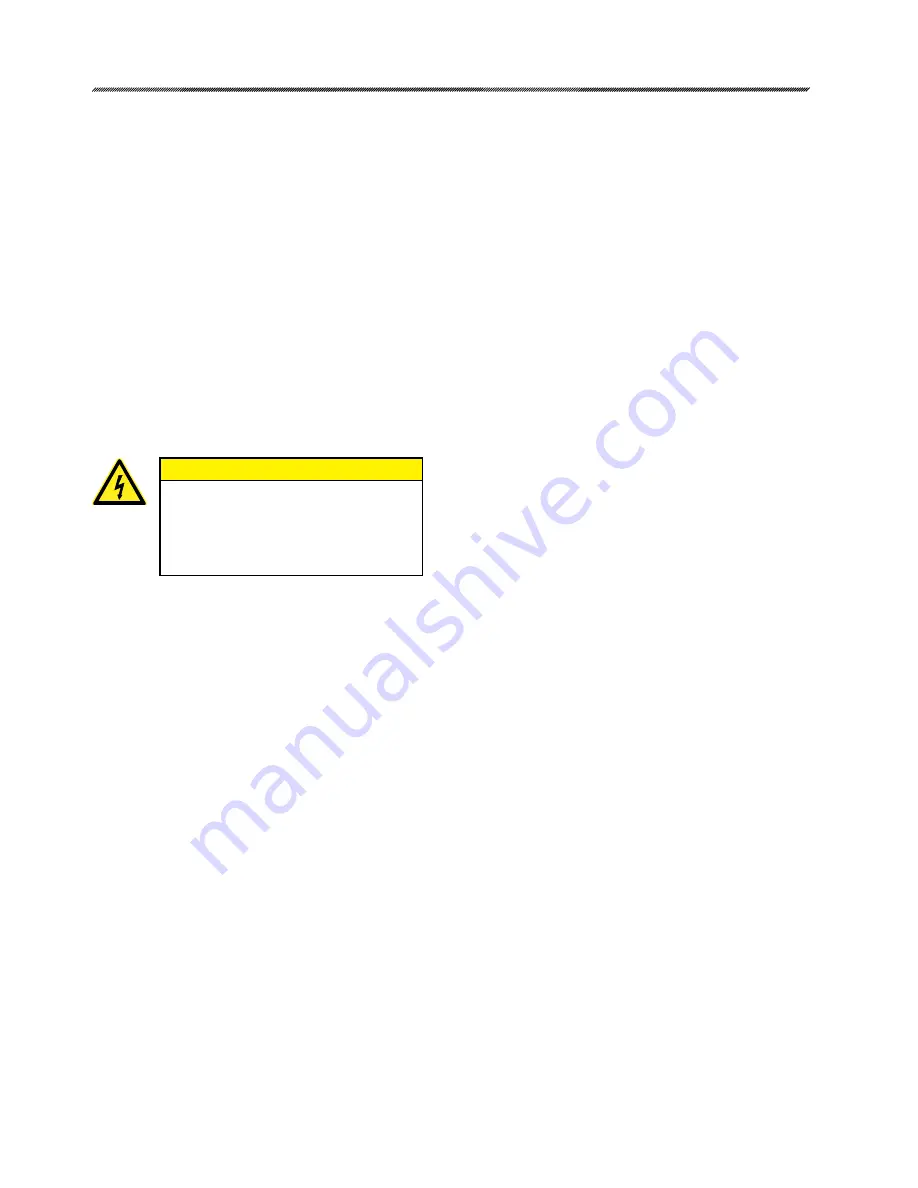
79
80-1403-01, Rev. 3
The Beck Group 14 actuator requires
only minimal routine maintenance. Periodic
lubrication of the gearing is recommended to
extend gear life. Periodic visual inspections
are recommended to verify that the connection
to the valve is intact and operating normally. If
vibration is present, check the electrical terminal
connections and other hardware for tightness.
LUBRICATION
The drive parts of the Beck actuator are
factory lubricated and in normal service will not
need relubrication for five years. Actuators in
more active service will require more frequent
relubrication. Any actuator operating near its
rated thrust and with a frequency of operation
greater than one per minute on a 24 hour
schedule should be inspected every two years.
CAUTION
Before removing the gear housing
assembly, block the valve stem to
prevent the gear train from moving
when the housing assembly is
removed.
To inspect or lubricate the output gear only,
remove the cover plate (1/2” bolt heads) on the
side opposite the motor. The output gear is not
field replaceable.
To inspect all the gears, first remove the
motor from the housing, following the instructions
on page 80. Then, remove the housing assembly
from the body (1/2” bolt heads). Clean all parts
thoroughly, removing as much old lubrication
as possible. Examine the gear teeth for signs
of excessive wear, scoring, or other damage.
Check for excessive free play of gears on shafts.
The assembly is not field repairable and should
be returned to the factory if excessive wear is
noted.
Before reassembly, recoat the teeth with
a heavy layer of Fiske Lubriplate GR-132 or
equivalent. GR-132 is an E.P. grease with
polymer additives. To reinstall the gear housing,
carefully position the housing on the body’s
alignment pins. Replace the bolts and tighten to
10 lb-ft (13.5 N•m).
Reattach the motor per the instructions on
page 80.
This section covers replacement of many
components of the Group 14 actuator. Note that
some components are not field repairable.
If it should ever be necessary to replace
the output gear, shaft, or output shaft bearings,
a major overhaul is required and the actuator
should be returned to the factory.
GASKETS
During routine service, inspect the gaskets
and O-rings for wear or damage. In order to
protect internal components, worn or damaged
gaskets and O-rings should be replaced.
To remove the main gear cover, terminal
compartment, or the motor gaskets, scrape all
of the old adhesive and gasket material from the
body housing and cover. Cement the new gasket
to the actuator body using a gasket cement such
as 3M #847 Rubber and Gasket Adhesive, or
equivalent.
O-ring seals are used between the body
and the top and bottom bearing plates. Before
installing a new O-ring, lubricate it with light
machine oil.
The large top cover is sealed with rubber
foam gasket material, 5/16” (8 mm) in diameter.
To replace this material, scrape the old gasket
material and cement from the groove. Cement
the new foam gasket into the groove with
3M #847 Rubber and Gasket Adhesive, or
equivalent. Cut the ends of the material on an
angle and cement them together with this same
adhesive.
SEALS
Worn or damaged output shaft and motor
shaft seals should be replaced to prevent
damage to internal bearings and drive parts.
To remove the shaft seal, push the blade of a
small screwactuatorr along the shaft and under
the seal lip. CAUTION: The seal is approximately
1/4” wide. Do not force the screwactuatorr blade
beyond the width of the seal; damage to the shaft
bearing could result. Pry up on the seal and
force it out of the housing. Clean the shaft and
housing and press in the replacement seal with
the closed side facing outward.
BEARINGS
There are some field replaceable bearings in
the Group 14 actuator. Consult the factory for
details.
MAINTENANCE
Routine / Component Replacement