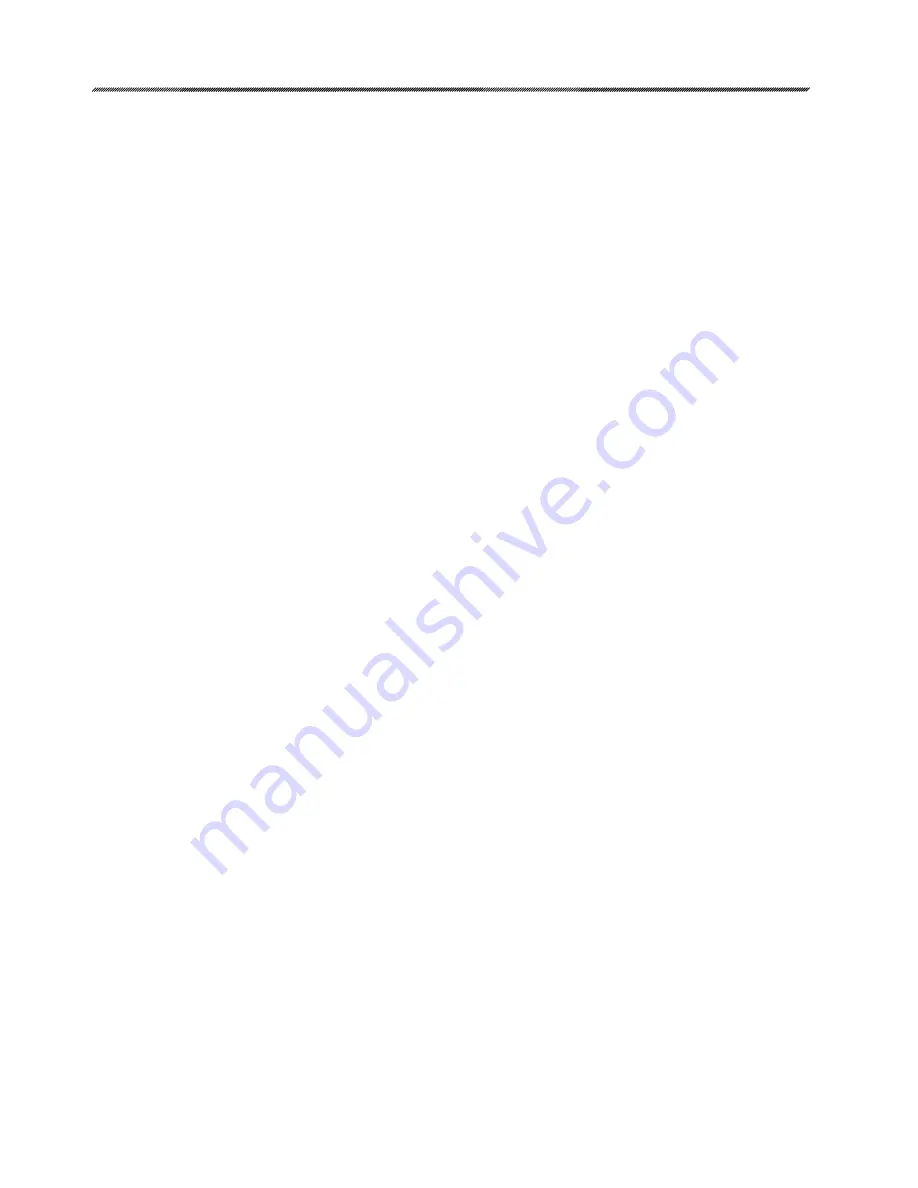
13
80-1403-01, Rev. 3
FOUNDATION FIELDBUS
COMMUNICATION OVERVIEW
The Foundation Fieldbus communication
interface is a method of superimposing digital data
onto a DC voltage power supply bus. Details and
specifications of the interface are maintained by
the Fieldbus Foundation.
The Foundation defines a large list of
predefined function blocks and defines the method
of using these function blocks. The Beck DCM-3
includes five blocks: One Resource Block, one
Transducer Block and three function blocks.
1. Resource Block
This block is a fieldbus requirement, and
is not directly used in controlling the Beck
actuator. This block is a standard block
as defined by Fieldbus Foundation, and
resembles all other standard Resource Blocks.
For typical automatic operation, this block
must be in Auto mode.
2. Transducer Block
This block is a fieldbus requirement, and
is generally not directly used in controlling the
Beck actuator. The Transducer Block is used
to read and write actuator‑specific calibration,
configuration, and status information.
Calibration and configuration information will
have a significant effect on the performance
of the actuator. For example, the direction
of rotation for an increasing set point is
determined by a setting in this block.
When installing the actuator pay particular
attention to Actuator Dir (Actuator_INFO2.
Actuator_DIRECTION) to configure the
direction of actuator movement in response to
an increasing actuator set point (page 30).
For typical automatic operation, this block
must be in Auto mode, and the Op Mode
parameter (Actuator_OPERATING_MODE)
set to Hold.
3. Analog Output (designated Channel 1)
This is a standard Analog Output function
block as defined by Fieldbus Foundation, and
is used to control the Beck actuator. Because it
is a standard Analog Output block, it resembles
all other standard Analog Output blocks.
Apply the actuator set point to CAS_IN. The
actuator set point is typically scaled in “percent.
”This set point is propagated to Transducer
Block variable “Demand” (DEMAND_VALUE).
For typical automatic operation, set
Channel to 1, set SHED_OPT to NormalShed_
NormalReturn, and set the mode to Cas|Auto.
For information on how the actuator utilizes
Demand, refer to DEMAND (page 25).
4. Analog Input (designated Channel 2)
This is a standard Analog Input function
block as defined by Fieldbus Foundation, and
is used to measure thrust load on the output
shaft. This function is not available with the
Group 14.
5. Analog Input (designated Channel 3)
This is a standard Analog Input function
block as defined by Fieldbus Foundation, and
is used to measure the internal temperature of
the actuator. Because it is a standard Analog
Input block, it resembles all other standard
Analog Input blocks.
Minimum and maximum recorded
temperatures can be viewed in the Transducer
Block. For typical operation, set Channel
to 3, and set L_TYPE to Indirect. For more
information on temperature sensing, refer to
TEMPERATURE SENSING (page 22).