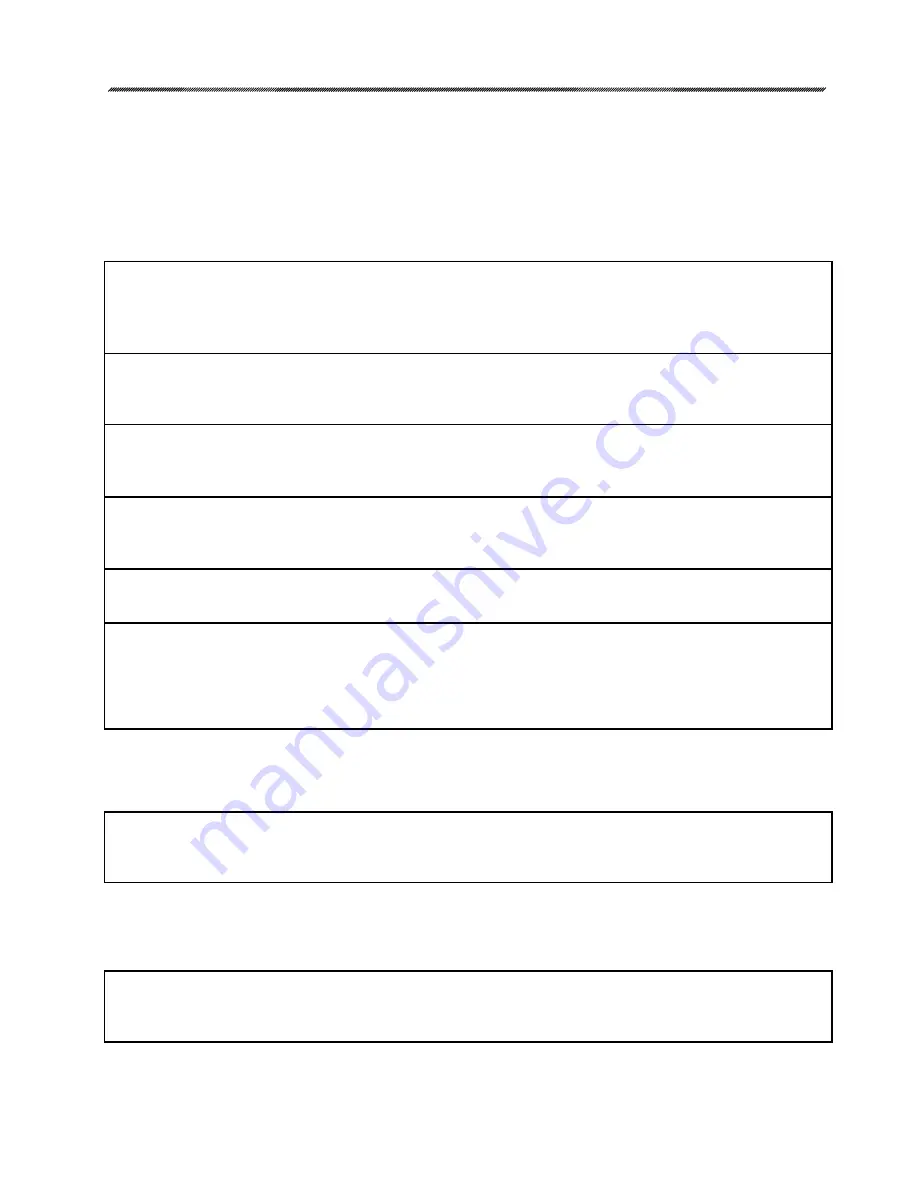
48
80-1403-01, Rev. 3
Common HART Messages
HART protocol maintains both standard and
device‑specific informational messages that are
displayed on the HART master when various
conditions occur. Below is a table of typical Beck
actuator messages and message sequences. It
does not include all possible messages, only the
most common.
Output Shaft Position Measurement Messages
Message
Process applied to the primary variable
is outside the operating limits of the field
device.
The Position Signal is less than -5% or
greater than 105%.
Position signal in LOS.
Position out of accurate measurement
range.
Position sensing error.
Analog output 1 and its digital
representation are outside the operating
range limits, and not responding to
input.
Description
This is a standard HART‑defined message that appears whenever
the position signal from the CPS-5, as measured at the DCM-3, is
outside the design or calibrated range. This message should be
accompanied by a Beck‑specific message with more detail.
This Beck‑specific message indicates the DCM‑3 is reading a
CPS-5 signal that is not within the expected calibration range.
Refer to OUTPUT SHAFT POSITION SENSING (page 28).
This is a Beck‑specific message. The DCM‑3 is reading a CPS‑5
signal that is outside of the range associated with a functional
CPS-5. Refer to OUTPUT SHAFT POSITION SENSING (page 28).
This is a Beck‑specific message. The DCM‑3 is reading a CPS‑5
signal that is outside of the range for accurate measurements.
Refer to OUTPUT SHAFT POSITION SENSING (page 28).
This is a Beck‑specific message. The DCM‑3 circuitry for measuring
the CPS-5 signal does not appear to be functioning properly.
This is a standard HART®‑defined message that appears whenever
the position signal from the CPS-5, as measured at the DCM-3, is
outside the range for accurate measurements. Refer to OUTPUT
SHAFT POSITION SENSING (page 28). This message should be
accompanied by a Beck‑specific message with more detail.
Handswitch and Over-travel Limit Switch Message
Message
Motor power is blocked, check switches.
Description
This message will appear if a condition beyond control of the
DCM‑3 microcomputer prevents current flow to the motor. Refer
to STOP/LIMIT INDICATION (page 22).
Stall Protection Message
Message
Stall condition has been detected (see
"Stall Time" in the "General Setup"
menu).
Description
This is a Beck‑specific message indicating that the Stall
Protection timer has determined an alarm exists. Refer to STALL
PROTECTION (page 23).
DCM-3 HART
Messages