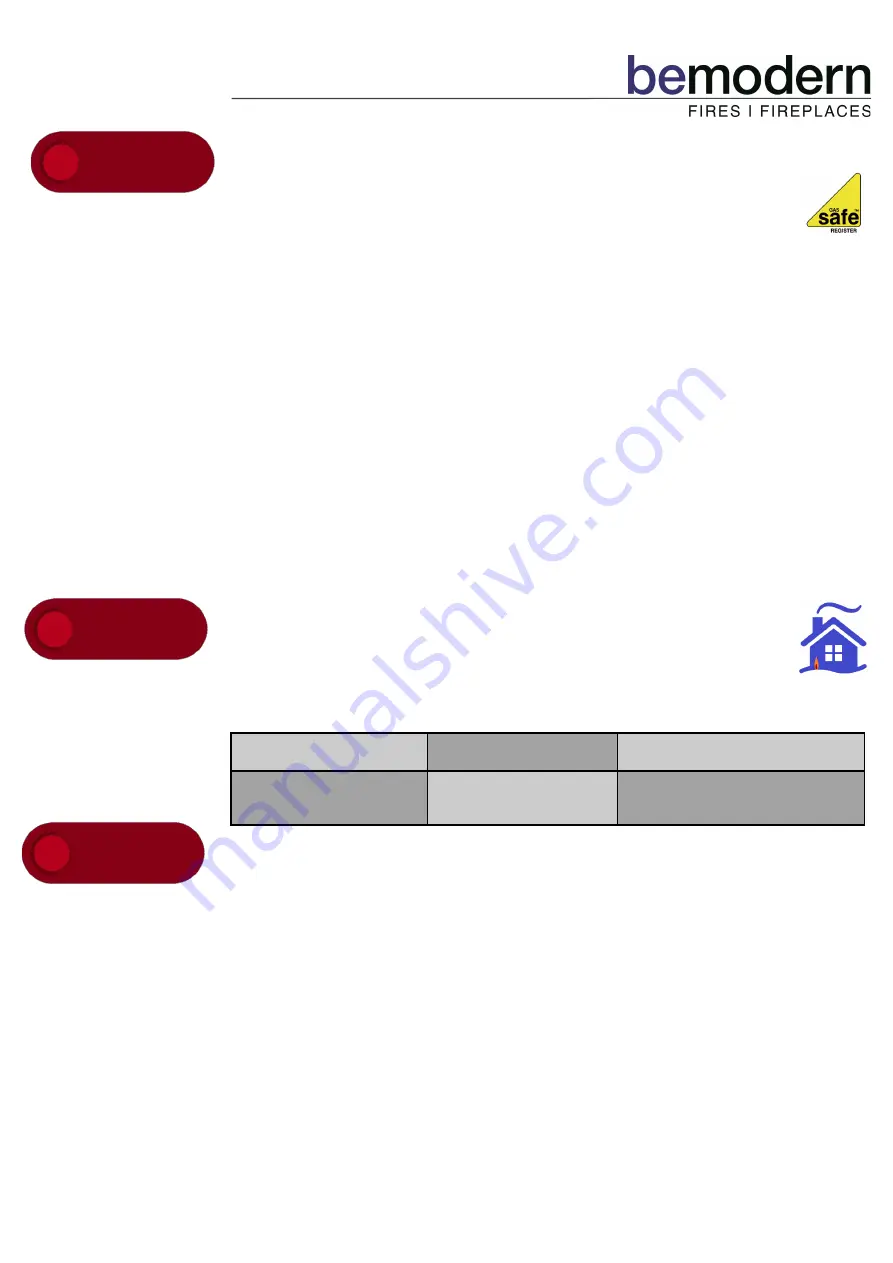
16
3.3
Prior to installation ensure that the gas supply is compatible with the appliance,
this appliance must only be used on
natural gas
at a supply pressure of 20 mbar as
marked on the data plate on the appliance and the carton.
This appliance is only to be installed into a builders opening which must be constructed
of non
-
combustible materials confirming to BS1251 or a suitable flue
-
box complying
with the requirements of BS715/BS EN 1856
-
2.
If the product is being installed into a builders opening the chimney must be at least 3
metres in height and should be swept before installation if it has been used for the
burning of solid fuel (e.g. coal or wood). The chimney must only serve as a flue
-
way to
this appliance and must have no openings to any other room. The opening should be
inspected and any exposed brickwork should be repaired where necessary. The chair
-
brick (if applicable) should be removed. Ensure that the chimney/flue only serves one
fireplace. Remove or securely fix open and dampers or register plates.
If the product is being installed into a fabricated Flue
-
box (to BS715) it must be
installed onto a non
-
combustible surface with a thickness of at least 12mm.
The flue should be checked for draw using a smoke bomb or similar, if there is a
definite draw then the installation of the appliance can proceed.
3.2
The efficiency of this appliance has been tested to EN613 and the result is
74.7% net (67.3% gross). This efficiency value has been verified by Kiwa
(0558). This efficiency value can be used for SAP (Standard Assessment
Procedure) for energy rating of UK dwellings.
Appliance Technical Information
INSTALLATION
INSTRUCTIONS
REGULATORY
INFORMATION
3.1 NOTE THE FOLLOWING PRIOR TO THE INSTALLATION OF THIS APPLIANCE.
This gas appliance
MUST
be installed by a GAS SAFE registered installer by
law. It must be installed in accordance to these installation instructions and
the GAS SAFETY (Installation & Use) REGULATIONS 1998 as amended. Non
compliance of this law may lead to prosecution and it is in the interest of you
and your family that this condition is observed.
The installation of this appliance must be in accordance with the relevant parts of the
LOCAL AND NATIONAL BUILDING REGULATIONS as issued by the Department of the
Environment or BUILDING STANDARD (Scotland Consolidation) REGULATIONS issued
by the Scottish Development Department and the following relevant British Standards:
BS5871
Part 2 Installation of Inset Live Fuel Effect Gas Fires
BS5440
Parts 1 & 2 Installation of Flues and Ventilation
BS6891
Installation of Gas Pipe
-
work
BS6461
Part 1 Installation of Chimneys and Flues
BS1251
Open Fireplace Components
BS715/BS EN 1856
-
2
Metal Flue Boxes /Metal Flue Pipes for Gas Appliances
BS EN 1858
Chimneys Components & Concrete Flue Blocks
IS813:1996
Domestic Gas Installation (Republic of Ireland)
GAS TYPE:
NATURAL
GAS CATEGORY:
I
2H
INLET PRESSURE:
(COLD)20mBar
HEAT INPUT:
GROSS 6.6kW
INJECTORS:
0.98 / 1.1
(4) / (1)
DESTINATION
COUNTRIES:
GB
EFFICIENCY /
TECHNICAL
INSTALLATION
REQUIREMENTS