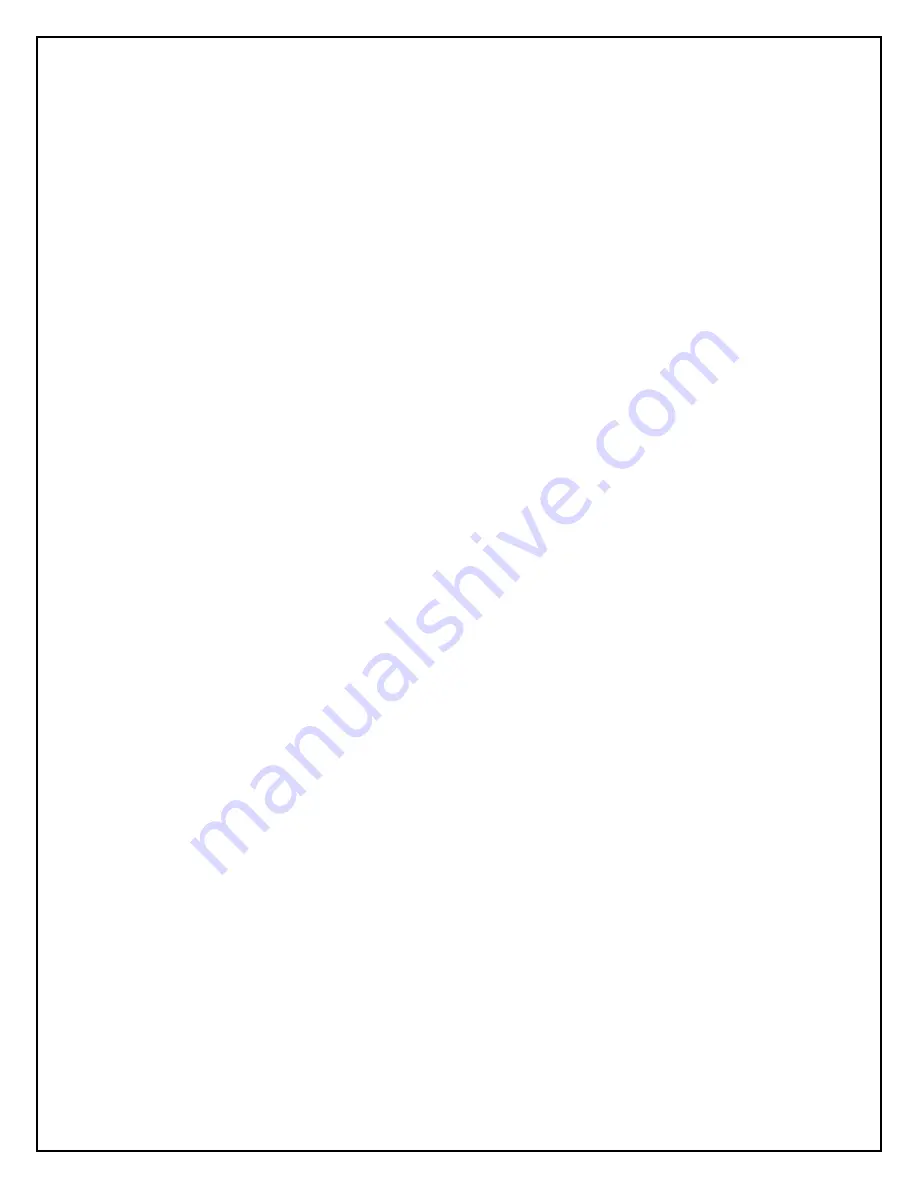
Microseparator™ Coolant Systems Transport, Installation, & Initial Startup
M000005_A - V Twin Ultra Transport & Installation 5.2-EN TM
55/78
18.9.1
Connection Point at the Machine
Connect tubing using a hose clamp to hose barb within the machine. It
can be routed through the hole provided at
on page 53
18.10
Dirty Coolant Drain from Generator
Typical generator drain connections are DIN100/4” to allow lenses to
pass unobstructed. Maintain the full pipe diameter into the Machine. The
drain should have minimum turns and no restrictions in diameter. DN100
pipe or US 4” with mating flexible rubber connection with hose clamp at
the generator is common.
18.10.1
Connection Point at the Machine
The coolant drain (and coolant line to the generator) can be connected
from either side as shown at
Figure 38 - Pump Station Connections
on page 53
. Only one generator may be connected to each Pump
Station.
18.11
Dirty Coolant Return to Coolant System
Return line connection is a 2” PVC pipe. Clear PVC pipe is recommended.
Connection Point at the Machine
The return pipe is connected at the top right as shown at item 5 in
section 8.2 above.
18.12
Connection Procedure
18.12.1
Connecting the Compressed Air Supply
Connect an appropriate air line to the fitting provided at
on page 53
Connect the other end of the hose to the building’s compressed air supply
system. Ensure that building air is clean and dry.
18.12.2
Connecting the Overhead Coolant Pipelines
Consult Satisloh for the installation guidelines for all supply and return
pipelines if you have also purchased the Bazell Microseparator™ System.
The installation diagrams specify important points to be closely followed
especially as they relate to diameter, fitting types, and piping restrictions.