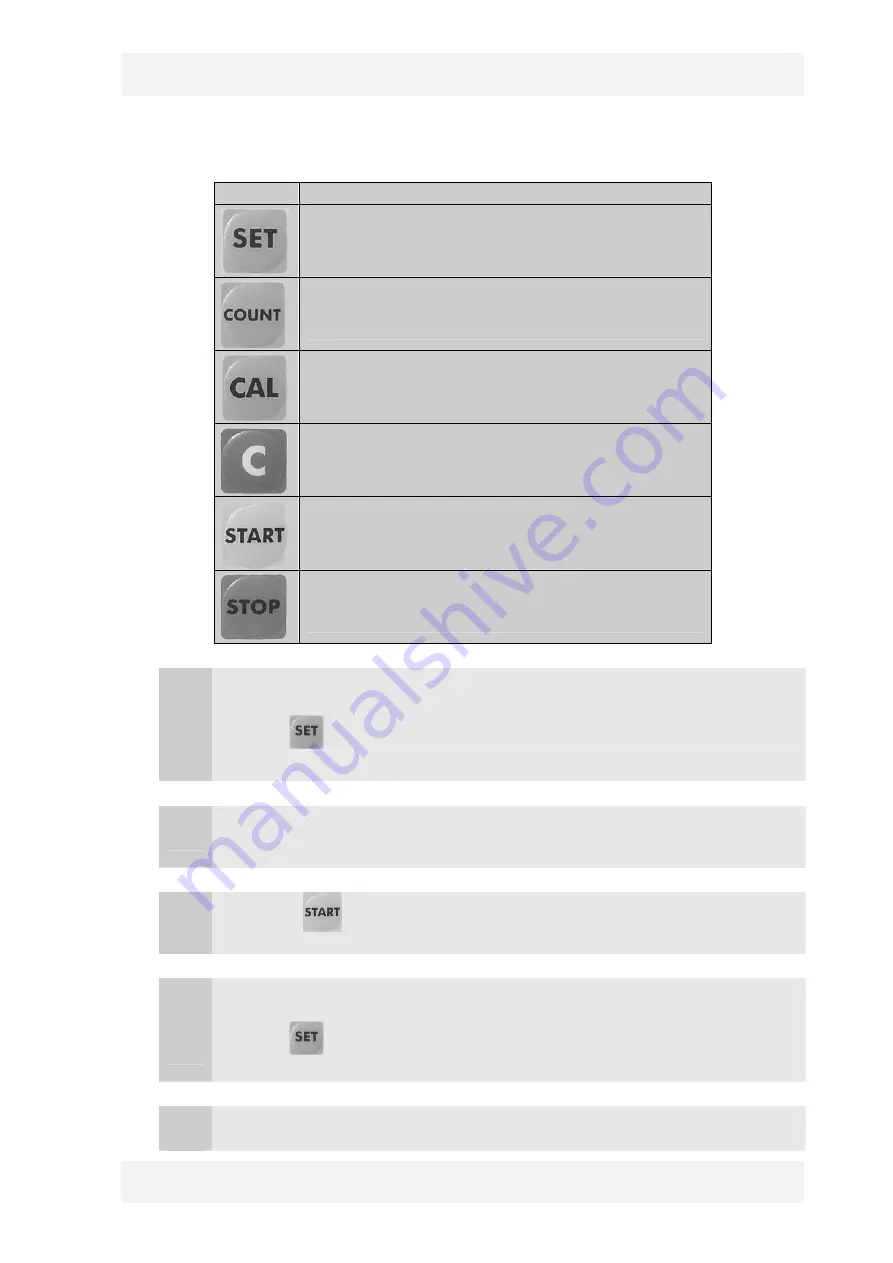
BAYKAL
EDITION NO :
HGL
SECTION :
DATE OF ISSUE :
November 2009
PAGE :
81
Figure 6.5.6.36
Key
Description
Set key
display shows
Quantity counter set key
Calibration Key
Clear key
Start and Enter key
Stop and Cancel key
1.
How to position the back-gauge
Press set key. The display will show 00000.
2.
Write desired position to the display by using numerical keys.
3.
Press start key. The back-gauge will move the desired position.
1.
How to enter quantity
Press set key. The display will show 00000.
2.
Write desired position to the display by using numerical keys.
Summary of Contents for HGL C Series
Page 15: ...BAYKAL EDITION NO HGL SECTION DATE OF ISSUE November 2009 PAGE 15 Figure 4 1...
Page 17: ...BAYKAL EDITION NO HGL SECTION DATE OF ISSUE November 2009 PAGE 17 INSTALLATION DIAGRAM...
Page 98: ...BAYKAL EDITION NO HGL SECTION DATE OF ISSUE November 2009 PAGE 98 APPENDIX A SPARE PART LIST...
Page 99: ...BAYKAL EDITION NO HGL SECTION DATE OF ISSUE November 2009 PAGE 99...
Page 100: ...BAYKAL EDITION NO HGL SECTION DATE OF ISSUE November 2009 PAGE 100 B HYDRAULIC CIRCUIT DIAGRAM...
Page 101: ...BAYKAL EDITION NO HGL SECTION DATE OF ISSUE November 2009 PAGE 101...
Page 102: ...BAYKAL EDITION NO HGL SECTION DATE OF ISSUE November 2009 PAGE 102 C ELECTRIC CIRCUIT DIAGRAM...
Page 103: ...BAYKAL EDITION NO HGL SECTION DATE OF ISSUE November 2009 PAGE 103...
Page 104: ...BAYKAL EDITION NO HGL SECTION DATE OF ISSUE November 2009 PAGE 104 ADDITIONAL MANUALS...