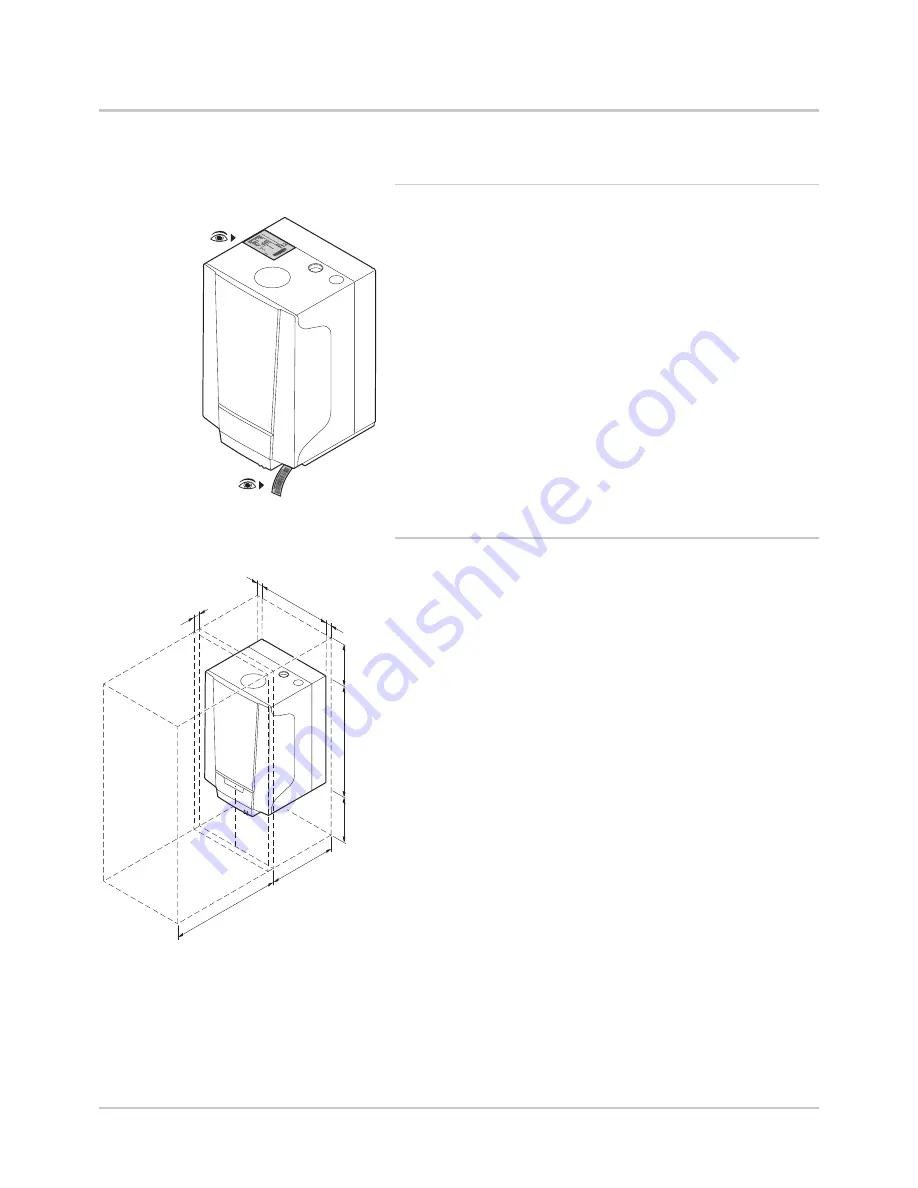
5.2
Choice of the location
5.2.1.
Type plate
The identification plate on top of the boiler features the boiler serial
number and important boiler specifications, for example the model
and unit category. The dF and dU codes are also stated on the type
plate.
5.2.2.
Location of the boiler
(1)
Clearance when operating
(2)
Clearance for maintenance
4
Before mounting the boiler, decide on the ideal position for
mounting, bearing the Directives and the dimensions of the
appliance in mind.
4
Ensure that there is sufficient space under the boiler to fit and
remove the condensate trap and the connection box.
4
To ensure adequate accessibility to the appliance and facilitate
maintenance, leave enough space around the boiler.
4
Mount the boiler onto a flat surface.
R000697-A
R000698-A
368
5
1000
(2)
364
≥ 200
5
≥ 250
554
5
(1)
5. Installation
Baxi MainEco Combi and System 24 - 28 - 35 / 18 - 24
20
02092014 - 7619497-02