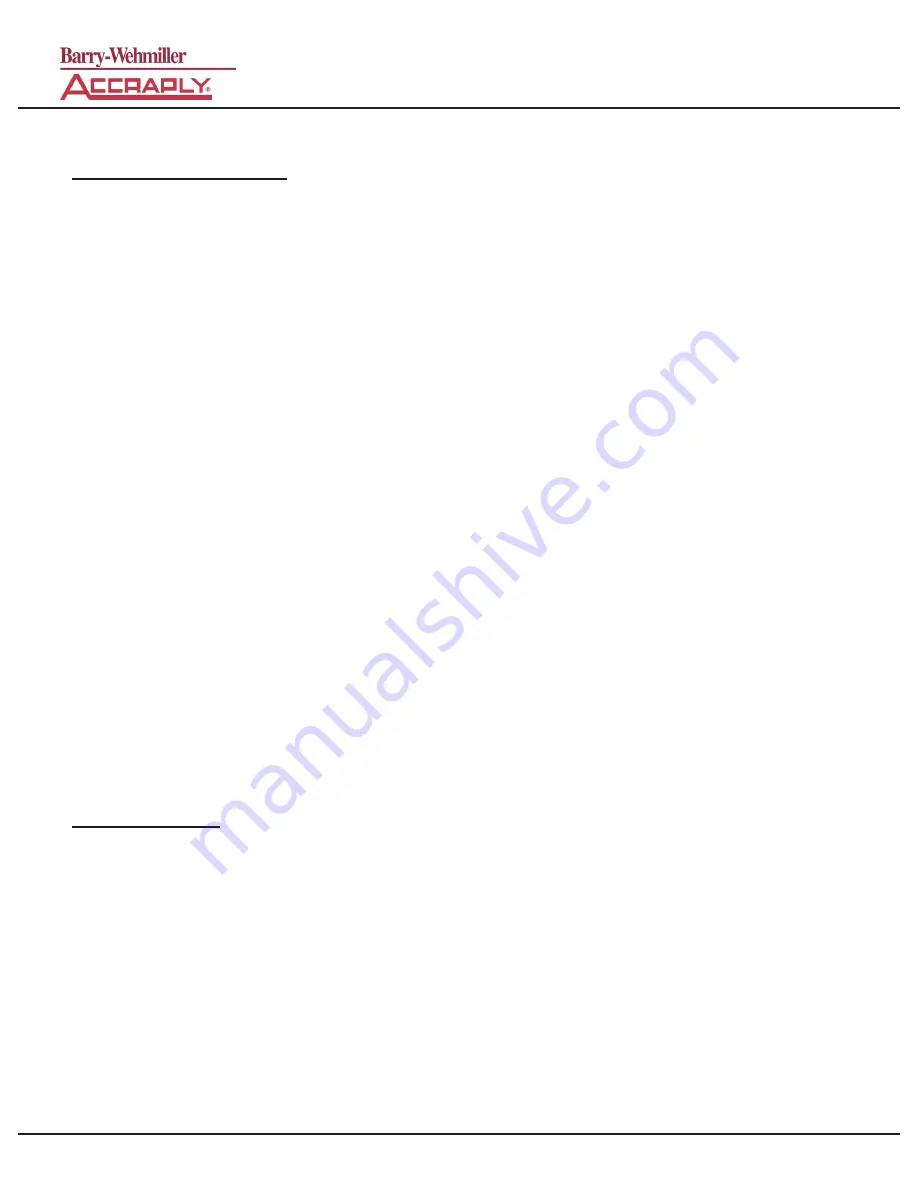
17
SECTION 1: SYSTEM OPERATION
1.3.6 General System Process
NORMAL OPERATING MODE:
1. The product will be presented to the labeling system by a conveyor supplied by the customer. The product will
be presented with the long side leading. The product will be transferred to the labeling system conveyor across a
transfer plate.
2. There will be a set of opposing spacing wheels at the infeed end of the conveyor. The spacing wheels will be
running slower than the labeling conveyor to ensure a gap between products.
3. Once the product has cleared the spacing wheels, it will contact a fixed turn bar that will cause the product to start
turning. Once it has turned to a certain point, the product will trigger a sensor. The sensor will signal a pneumatic
turn cylinder to actuate. The cylinder will extend and contact the product to assist in turning it. The product will
then travel into a set of guide rails to guide the product into the labeling station.
4. At the labeling station, the product will trigger a product sensor which will initiate the label sequence. A label will
be dispensed by the 204 label applicator onto the top of the product at the leading corner. The label will be flagged
off the leading corner. The 204 label applicator will be programmed to dispense a second label at a set distance
relative to the first label. The distance will be based on pulses received from an installed speed following encoder.
The second label will be flagged off the trailing edge of the product.
5. The product will then travel to the custom label wipe-down station. The product will trigger wipe-down sensor just
before it runs into a closed stop gate. The wipe-down sensor will initiate the wipe-down sequence. A squaring
device cylinder will actuate to square up the product. A cylinder mounted above the product will extend and apply
pressure to the top of the product. This will ensure the lid will be held closed tightly. The second cylinder will
then extend. Fingers mounted on the cylinder will wipe both labels down the sides. The second cylinder and the
squaring device cylinder will retract and then checker sensors will inspect the product for label presence. Products
with two present labels will be considered a pass. Products without two present labels will be considered a fail.
Once the result is determined, the hold-down cylinder will retract. If the inspection is a pass, the stop gate will
open and the product will travel down the conveyor. At the trailing edge of the wipe sensor, the gate will close
and wait for the next product. If the inspection is a fail, the stop gate will remain closed and the product will
immediately be ejected into a reject bin. Ejected products will be verified by an eject verification sensor. This
sensor will also act as a bin full sensor.
6. The passing products travel to the end of the conveyor to a transfer plate where it will eventually be pushed onto
another customer supplied conveyor.
CHALLENGE MODE:
Challenge mode is selectable by use of a selector switch on the main control panel. When Challenge mode is on, the
system process is as follows.
1. Spacing wheels are stopped and labeler is inhibited in challenge mode.
2. Operator places a product on the conveyor between the guiderails, upstream from the labeler in the orientation
that it would normally be labeled.
3. The product travels through the labeling station but does not receive any labels.
4. The product enters the wipe-down station and the normal wipe-down sequence occurs. The checker operates
as normal. Passing products (if the product was already pre-labeled) will go to the end of the conveyor, failing
products will be ejected.
GENERAL INFORMATION
Summary of Contents for Accraply 204RH
Page 2: ......
Page 6: ......
Page 8: ......
Page 29: ...21 SECTION 1 SYSTEM OPERATION 1 3 9 P ID GENERAL INFORMATION ...
Page 44: ......
Page 49: ...080800 07411 Infeed Metering Wheels ...
Page 59: ...600895 07411 Control Electrical NO DRAWING AVAILABLE ...
Page 82: ......
Page 84: ......
Page 86: ...2 SECTION 3 ELECTRICAL DRAWINGS 200000 07411 Sheet 1 of 9 ...
Page 87: ...3 SECTION 3 ELECTRICAL DRAWINGS 200000 07411 Sheet 2 of 9 ...
Page 88: ...4 SECTION 3 ELECTRICAL DRAWINGS 200000 07411 Sheet 3 of 9 ...
Page 89: ...5 SECTION 3 ELECTRICAL DRAWINGS 200000 07411 Sheet 4 of 9 ...
Page 90: ...6 SECTION 3 ELECTRICAL DRAWINGS 200000 07411 Sheet 5 of 9 ...
Page 91: ...7 SECTION 3 ELECTRICAL DRAWINGS 200000 07411 Sheet 6 of 9 ...
Page 92: ...8 SECTION 3 ELECTRICAL DRAWINGS 200000 07411 Sheet 7 of 9 ...
Page 93: ...9 SECTION 3 ELECTRICAL DRAWINGS 200000 07411 Sheet 8 of 9 ...
Page 94: ...10 SECTION 3 ELECTRICAL DRAWINGS 200000 07411 Sheet 9 of 9 ...
Page 95: ...11 SECTION 3 ELECTRICAL DRAWINGS 621593 Pnu Schematic ...