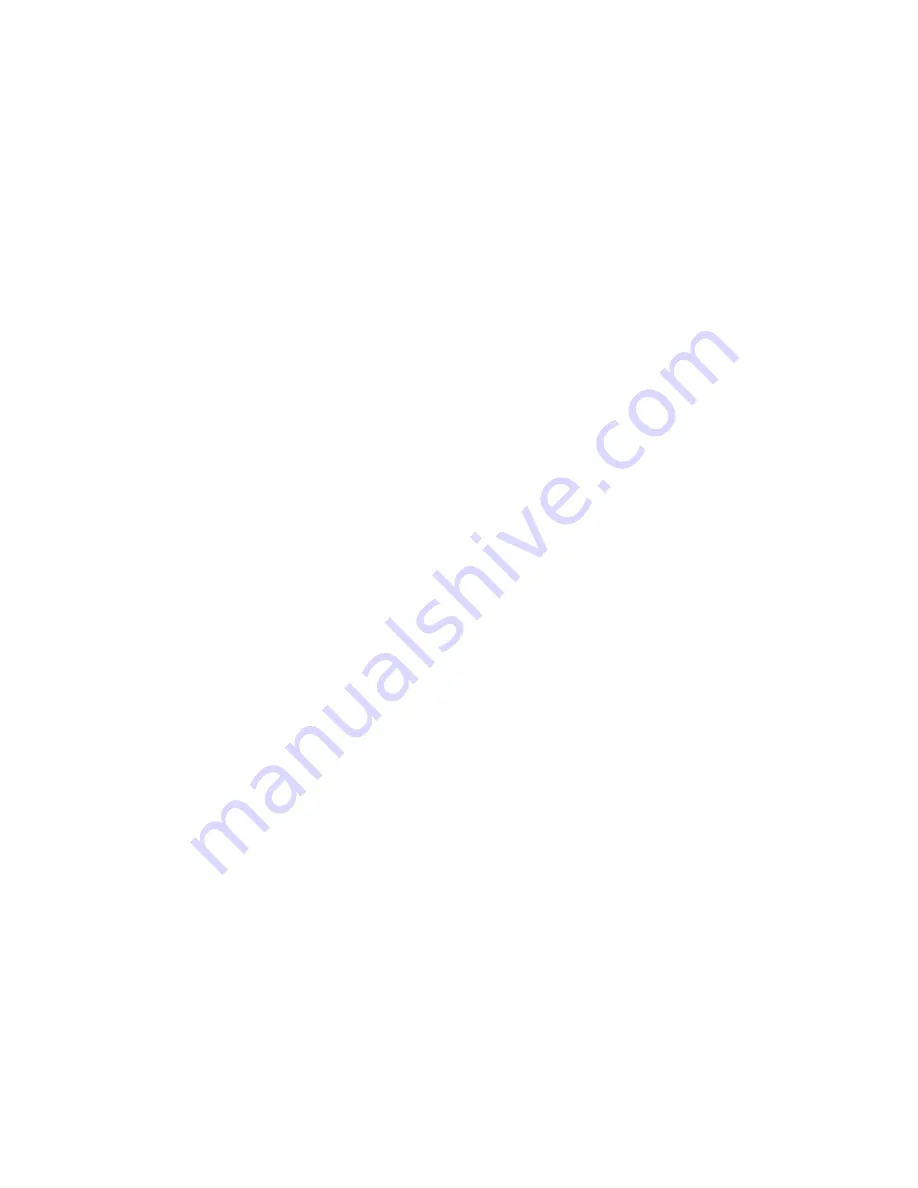
Appendix B FAQ
Q1:
What type of finger motions are possible with the BarrettHand™ and what servos and
mechanisms are used to control them?
A1:
The BarrettHand™ has 3 identical curling 2-joint fingers, each with its own built-in,
independent, high-performance brushless motor drive. A patented TorqueSwitch™
mechanism then channels torque from the motor to the two joints depending on:
1.
TorqueSwitch™
level set for that particular grasp
2.
Joint-torque status
In its full-open state, each finger's inner-link surface is almost parallel with the palm
plate, while the outer finger link is curled inward by 42 degrees. When a finger is
commanded to close under velocity or position control, the links move according to the
transforms in Section 9.5, the resulting motion will be curling, to promote form closure
before a grasp contact is initiated. If the outer fingertip makes first contact with an
object, it develops full force against the object until no motion is detected, at which point
the motor current may be removed since the finger joints become mechanically locked.
However, if the inner finger link makes first contact, the motor applies the torque to both
links until the TorqueSwitch™ level is reached. At this instant, the inner link is locked
into position mechanically, and all motor torque is shunted to the outer link, which stops
only at motor stall torque. The net result is highly effective grasping.
The patented finger-spread motion has two opposable fingers and one fixed finger. To
minimize the number of motors (and thereby the weight, bulk, heat, power, and cost of
the BarrettHand™), one motor drives the "spread" action of both fingers synchronously
and symmetrically about the palm.
The spread motion adds surprising dexterity. One design feature of the spread motion is
that, unlike the curling motions of each finger, the spread is highly backdrivable, so that
the spread compliance is controllable. By setting low spread compliance, the
BarrettHand™ dynamically finds the lowest energy state as the fingers close, resulting in
a firm and reliable grasp.
Q2:
Can the outer two finger joint motions be controlled independently?
A2:
No, the two joints are controlled by one servo-motor. Although the mechanism behaves
in an intelligent manner for grasping, we traded the second motor and motor electronics
for the TorqueSwitch™ mechanism to save weight, bulk, heat, power, and cost.
Q3:
How does the Torque Switch™ mechanism work and what is the clutch used for?
A3:
See Section 9.3 for information on how the TorqueSwitch™ mechanism works.
Q4:
What materials are the fingers made of, particularly the fingertips?
A4:
The finger tip and covers on the BH8-260 and later are anodized aluminum. Nylon tip
and covers are optional. The finger links are made of aluminum and the gearing is made
of steel and bronze. The base shell is made of anodized aluminum on the BH8-260 and
later; Carbon-Kevlar composite before the BH8-260.
Some new BH8-280 hands have a cast urethane blue material for the finger tip that
presently has a durometer of 80 but this may be lowered to 70 for future hands. Finger
tips will likely change so please ask about them if you have a need for special finger tips.
Barrett is working on black rubber pads for customers without pressure profile sensor
tips.
Page 82 of 89