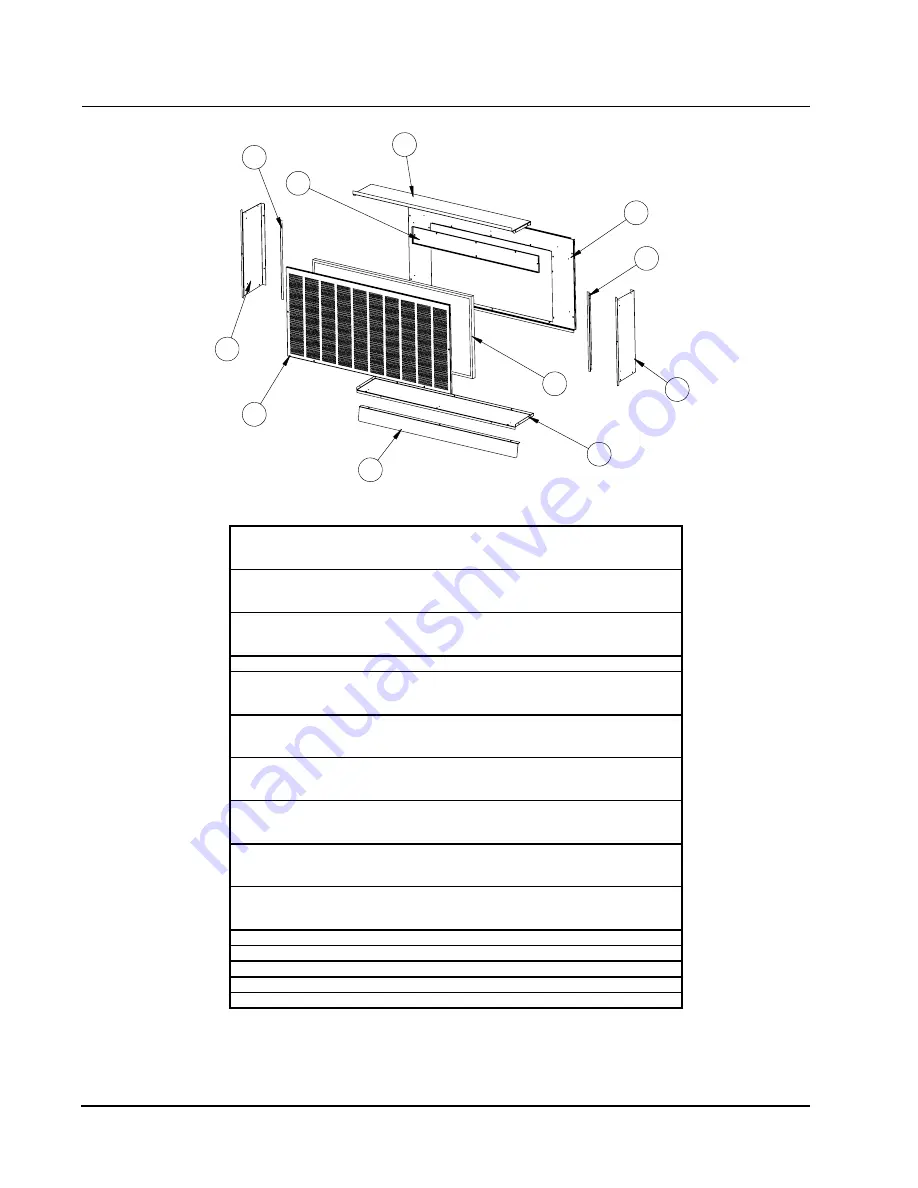
Manual 2110-1456A
Page
10 of 11
FREECOOLING AIR HOOD
SEXP-752A
Dwg. No.
Part Number
Description
1
1
1
115-285-*
115-292
k
115-293
Hooded Front Door
Hooded Front Door
Hooded Front Door
2
2
2
113-545-*
113-569
k
113-570
Bottom Divider Bracket
Bottom Divider Bracket
Bottom Divider Bracket
3
3
3
S127-494-*
S127-563
k
S127-503
Hood Bottom
Hood Bottom
Hood Bottom
4
7003-080
Mist Filter 31-1/4" x 15-7/8" x 7/8"
5
5
5
S101-984-*
S101-1033
k
S101-1013
Right Side
Right Side
Right Side
6
6
6
105-1346
105-1346
k
105-1370
Side Filter Angle
Side Filter Angle
Side Filter Angle
7
7
7
553-667-*
553-711
k
553-702
Hood Mounting Door
Hood Mounting Door
Hood Mounting Door
8
8
8
S107-345-*
S107-355
k
S107-356
Hood Top
Hood Top
Hood Top
9
9
9
553-613
553-634
k
553-631
Filter Door
Filter Door
Filter Door
10
10
10
S101-873-*
S101-997
k
S101-882
Left Side
Left Side
Left Side
920-0390
Complete Hood Assembly - Beige
920-0391
Complete Hood Assembly - White
920-0392
Complete Hood Assembly - Buckeye Gray
920-0421
Complete Hood Assembly - Stainless Steel
920-0408
Complete Hood Assembly - Aluminum
E
x
terior cabinet parts are manufactured with various paint color options. To ensure the
proper paint color is received, reference the following codes:
Beige -X
Buckeye Gray -4
White -1
k
Exterior cabinet parts are manufactured from stainless steel Code "S"
Exterior cabinet parts are manufactured from aluminum Code "A"
SEXP-752 A
6
2
9
5
6
8
3
10
1
7
4
Summary of Contents for MULTI-TEC W18ABP Series
Page 2: ......
Page 12: ......
Page 18: ...Manual 2100 479 Page 6 of 11 FIGURE 1 TYPICAL AIR CONDITIONING SYSTEM COOLING CYCLE MIS 369 ...
Page 19: ...Manual 2100 479 Page 7 of 11 FIGURE 2 TYPICAL HEAT PUMP SYSTEM COOLING CYCLE MIS 368 ...
Page 24: ......
Page 63: ......
Page 108: ......
Page 111: ......
Page 123: ......
Page 126: ......