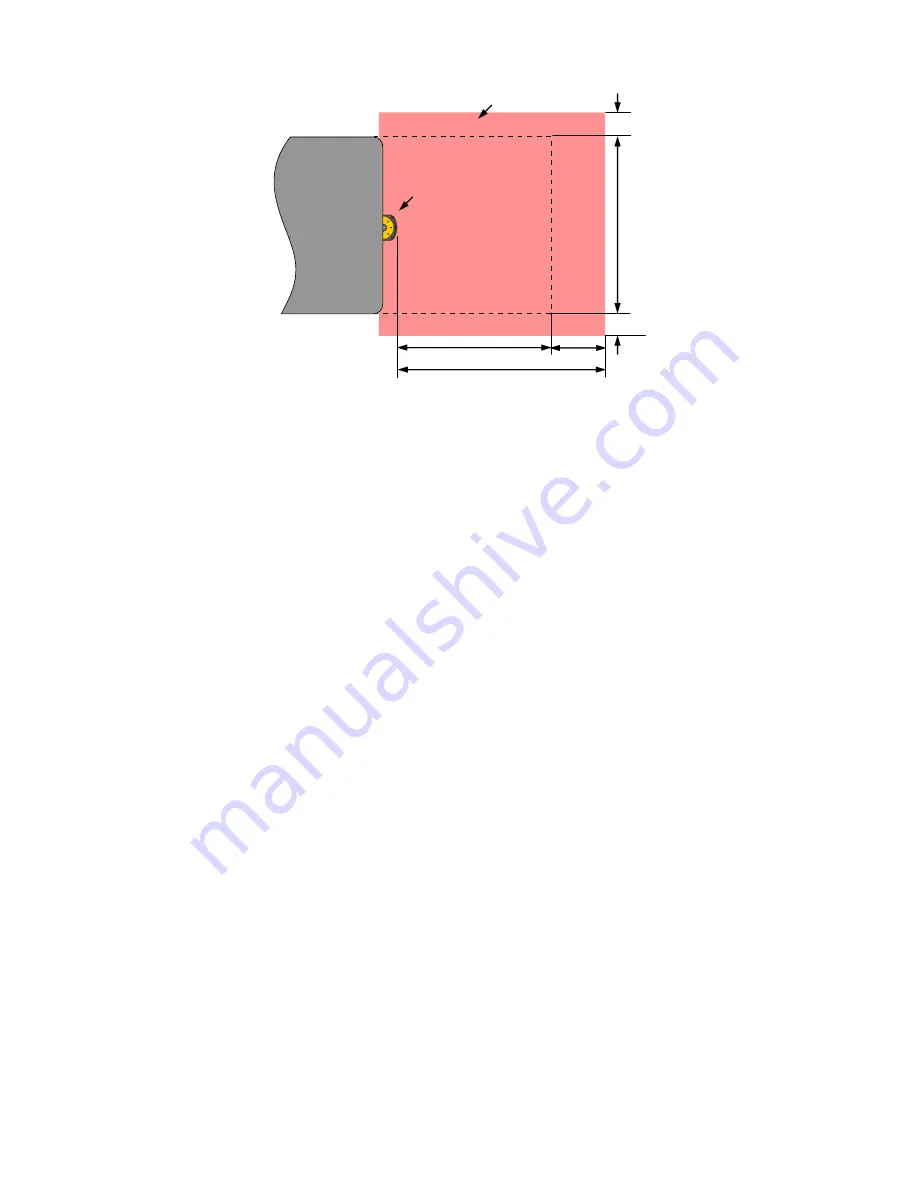
D
D
SD
Z
RIGHT
Z
LEFT
Z
LEAD
Scanner
Safety Zone (SZ)
Mobile
Vehicle
Mobile
Vehicle
Figure 28. Calculating the minimum distance in a mobile vehicle application
D
SD
= [V
MAX
× (T
S
+ T
R
)] + D
B
where:
D
SD
= Stopping distance in mm
V
MAX
= the maximum velocity as stated by the manufacturer of the mobile vehicle
T
S
= maximum stop time (in seconds) of the mobile vehicle (see note 1 below)
T
R
= maximum response time (in seconds) of the Scanner (see note 2 below)
D
B
= Braking Distance at full load and speed as stated by the manufacturer of the mobile vehicle and other
environmental factors (see note 3 below)
Notes
1. T
S
for the mobile vehicle should be supplied by its manufacturer. T
S
must include the response time of all devices or
controls that react to stop the vehicle (e.g., UM-FA-9A Safety Module), which are added to determine the total time
to cause braking/stopping. If all devices are not included, the calculated distance (D
SD
) will be too short and serious
injury could result.
2. Braking Distance (D
B
) should incorporate factors such as brake deterioration and environmental factors that can
impact braking (such as loose dirt/gravel, wet/moisture, icing, etc.) which can add 10% or more to the
manufacturer’s stated distance. It should be noted that braking distance is not a linear function; it increases by a
square function as velocity increases.
3.9.3 Additional Distance Factors (Z) Specific for Mobile Applications
For mobile applications, two additional factors must be considered: Z
SM
and Z
amb
.
Z
SM
Measurement Tolerance Factor—For Horizontal Safety Zones (parallel approach): Z
SM
= 150 mm.
Z
amb
Retro Reflector Factor—The additional distance needed to account for measurement errors due to light interference
(see section 3.x.4) and/or reflections from highly reflective or shiny surfaces that are present in the scanning plan.
• No ambient interference Z
amb
= 0
• Ambient Interferences present Z
amb
= Value interpreted from the graph based on dust filter level
Z
F
Mobile Vehicle (AGV) Ground Clearance— The additional distance Z
F
is required if the mobile vehicle does not have
sufficient ground clearance (HF) such that there is no space under the vehicle or Scanner for the tips of feet. If the wheels
are mounted near the side wall, always add an additional distance Z
F
≥ 150 mm; otherwise Z
F
is determined according to
the following figure.
SX5 Safety Laser Scanner
www.bannerengineering.com - Tel: +1.763.544.3164
35