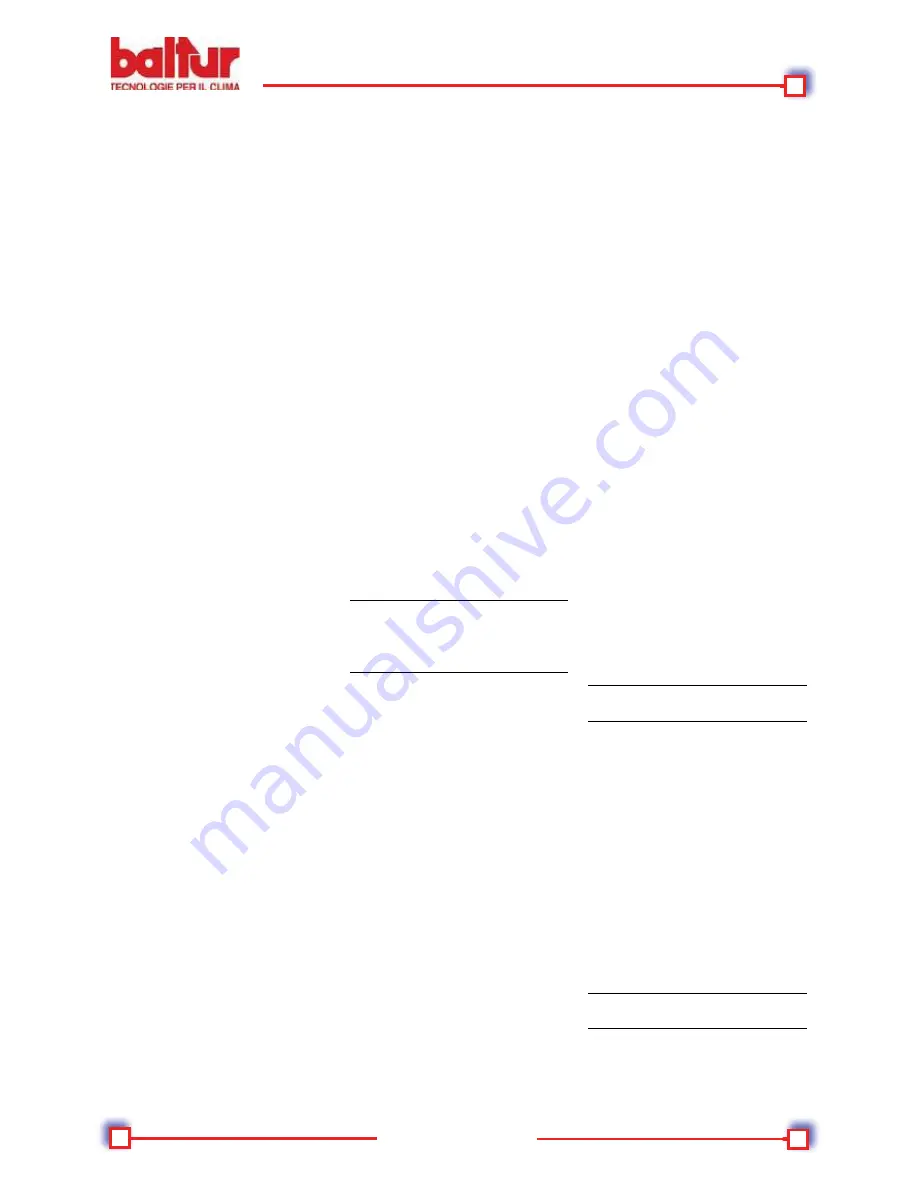
30 / 63
0006080480_200710
properly “grounded”. We must
point out that the minimum
value of the ionisation current to
ensure the working of the control
box is shown in the electrical
diagram; normally the ionisation
current is decidedly higher. To
check the ionisation current,
connect a microammeter with
an adequate scale “in series” to
the ionisation circuit. The high
isolation wire that comes from
the electrode must be inserted
to the negative (sign -) of the
microammeter.
5) With the burner on, adapt
delivery to that desired (methane
gas = 8550 Kcal/m
3
) by reading
the meter. Take two readings,
the second one exactly one
minute after the first one. The
difference between the two
readings schould be multiplied
by in order to obtain the flow per
hour (60 minutes). This output
can be modified by operating the
special regulator incorporated in
the valve (see the last pages for
a desciption of how to regulate
the valves).
6) Control that combustion occurs
correctly by using the appropriate
instruments (CO
2
= about 10%
for methane gas - CO max. =
0.1%).
7) After regulation, turn the burner
off and on again several times
to check that ignition occurs
correctly.
8) N.B. On some burner models,
the thermostat of the 2nd
flame must be at 2 contacts (in
exchange); please do refer to
the eletric diagram of the specific
burner, in case you haven’t the
thermostat in exchange at two
contacts, please do refer to
the diagram 0002050151. With
the burner switched off at the
general switch, switch on the
second flame thermostat and
set it by adjusting the control on
the servo so that the air shutter
opening is at the appropriate
level for the second flame (see
0002932130). Open the gas
flow regulator on the valve to
archive the appropriate delivery
rate for the second flame (main
flame).
9) Switch off the general switch to
start up the burner. When the
has started up it is necessary to
check as previously shown, the
gas delivery and the combustion
with the appropriate instruments.
When the results are known,
necessary, proceed with varying
the gas delivery and relative
combustion air in order to adapt
delivery to that required for the
specific case (boiler potentiality).
It’s also necessary to check
if the CO
2
and CO values are
adequate (CO
2
max. = about
10% for methane gas and CO
= 0.1%).
10) Control the efficiency of the
safety devices: the “shut down”
(by detaching the ionisation
electrode cable), the air pressure
switch, the gas pressure switch,
the gas pressure switch and the
thermostats).
AIR REGULATION ON THE
COMBUSTION HEAD
(see
BT 8769/2 and 0002932171)
The combustion head is equipped
with a regulating device which closes
and opens the air passage between
the disk and the head. By closing the
passage it’s possible to achieve high
pressure upstream the disk for low
inputs as well. High velocity and tur
-
bulence ensure a better penetration in
the fuel, an optimum mixture and good
flame stability. It might be necessary
to have high air pressure upstream
the disk in order to avoid flame pul
-
sation and it’s considered practically
indispensable when the burner is
operating with a pressurised furnace
and/or thermal load. It’s evident from
the above, that the device which clo
-
ses the air on the combustion head
should be put in such a position as
to
always
obtain a decidedly high
air pressure value behind the disk.
It’s advisable to regulate in such a
way as to achieve a closing of the
air on the head; this will necessitate
a considerable opening of the air
shutter which regulates the flow to
the burner’s fan suction. Obviously,
these adjustments should be carried
out when the burner is operating at
maximum delivery desired. In prac
-
tice, start regulating by putting the
device which closes the air on the
combustion head in an intermediate
position, start up the burner and
make trial adjustments as previously
described.
When maximum delivery desired
has been reached, proceed with
correcting the position of the device
which closes the air on the combu
-
stion head; move it backwards or
forwards in such a way as to obtain
an air flow suitable to the delivery,
with the air regulation shutter in
suction considerably open.
When
reducing the air passage on the
combustion head, avoid closing it
completely.
N.B. Check that ignition occurs
regularly, because if the passage
between the disk and the head is
closed, it could occur that the air ve-
locity is so high as to render ignition
difficult. If this happens, gradually
open the regulator until it reaches
the correct position and ignition oc-
curs regularly. This position should
be definitive.
MAINTENANCE
The burner does not require special
maintenance, but it is good practice to
check periodically that the gas filter is
clean and that the ignition electrode is
efficient. It is also necessary to verify
that the ignition electrode’s spark is
produced between the same electro
-
de and the disk. The combustion
head may need cleaning. During re-
assembly, special attention must be
paid to centring exactly the electrodes
(ignition and flame detection) in order
to avoid them going to earth or short-
circuiting which would result in the
“shut down” of the burner.
USE OF THE BURNER
The burner operates fully automati
-
cally, therefore it is non necessary to
carry out any kind at adjustment during
its operating.
Summary of Contents for SPARKGAS 20P - 20PW
Page 2: ......
Page 23: ...32 63 0006080480_200710...
Page 24: ...33 63 0006080480_200710...
Page 31: ...61 63 0006080480_200710...
Page 32: ...62 63 0006080480_200710...
Page 33: ...63 63 0006080480_200710...