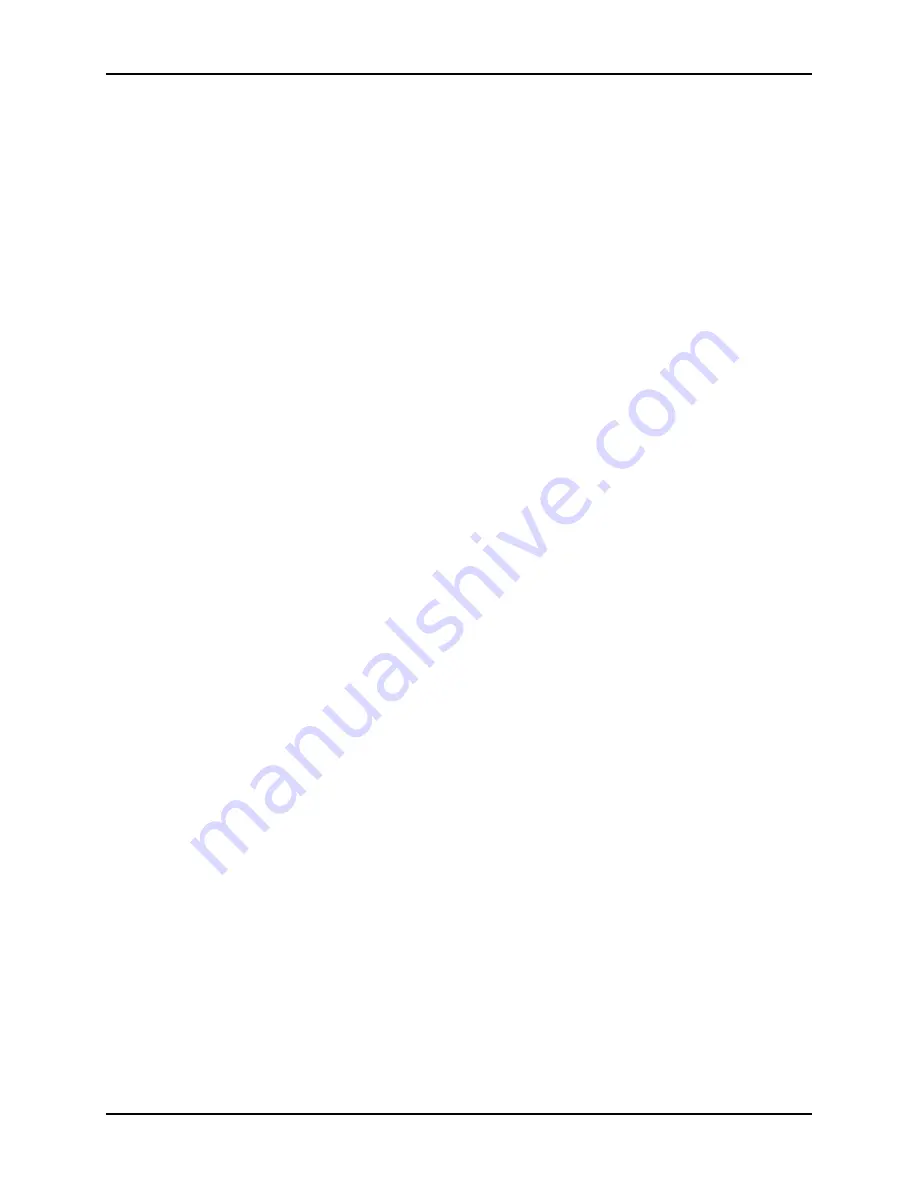
Multi-Zone Gas Monitors
iv
P/N: 3015-5074 Rev 11
2.8.2. Saving and Sending Programs .....................................................................................20
2.8.3. Trend Data ..................................................................................................................20
2.8.4. Converting the TRE ND Text File to a Microsoft Excel File ..............................................20
2.8.5. Saving and Printing Screens and Logs ..........................................................................20
2.8.6. USB Type Laptops .......................................................................................................20
2.9. Optional Current Loop Interfaces ..............................................................................................21
2.9.1. Optional 4–20 mA DC Outputs......................................................................................21
2.9.2. 4-20 mA DC Connections .............................................................................................22
2.10. Connecting External Alarms .....................................................................................................23
2.10.1. Overview.....................................................................................................................23
2.10.2. Connection ..................................................................................................................23
SECTION 3. SETUP PROGRAMMI NG .............................................................................................25
3.1. Initial Power Up .......................................................................................................................25
3.2. Data Display Screen ................................................................................................................25
3.3. Navigating to the 1st Setup Screen ...........................................................................................25
3.4. Navigating to the 2nd Setup Screen ..........................................................................................25
3.4.1. Location ......................................................................................................................26
3.4.2. Number of Zones Installed............................................................................................26
3.4.3. Alarm Acknowledge Mode ............................................................................................26
3.4.4. Audible Alarm ..............................................................................................................26
3.4.5. Zone Hold ...................................................................................................................27
3.4.6. Detection Limit.............................................................................................................27
3.4.8. Loop Mode ..................................................................................................................27
3.4.7. Loop2 Factor ...............................................................................................................27
3.4.9. Re-Zero Mode .............................................................................................................28
3.5. Navigating to the 3rd Setup Screen...........................................................................................28
3.5.1. Overview.....................................................................................................................28
3.5.2. Baud Rate ...................................................................................................................28
3.5.3. Node Address .............................................................................................................28
3.5.4. Password ....................................................................................................................28
3.6. Additional Service Feat ures ......................................................................................................29
3.6.1. Service Timeout...........................................................................................................29
3.6.2. DE T Digipot .................................................................................................................29
3.6.3. Node Address .............................................................................................................30
3.6.4. Sensor Temperature Coefficient (For Factory Use Only).................................................30
3.6.5. Password ....................................................................................................................30
3.6.6. Acquiring Temperature Coefficient (For Factory Use Only) .............................................30
3.6.7. IR Digipot ....................................................................................................................30
3.7. Establishing the CO
2
Sensor Baseline.......................................................................................30
SECTION 4. GENERAL OP ERATION ..............................................................................................31
4.1. Functional Overview ................................................................................................................31
4.2. The Zone Setup Screen ...........................................................................................................31
4.2.1. Location ......................................................................................................................31
4.2.2. Gas/Refrigerant Type...................................................................................................31
4.2.3. Distance......................................................................................................................32
4.2.4. Zone Temperat ure .......................................................................................................32
4.2.5. Current Detection Reading ...........................................................................................32
4.2.6. Log Interval .................................................................................................................32
4.3. Navigating to the 2nd Zone Setup Screen .................................................................................32
4.3.1. Leak Level ..................................................................................................................33
4.3.2. Spill Level ...................................................................................................................33
4.3.3. E vacuation Level .........................................................................................................33
4.3.4. Re-S etting the Peak PPM Value ...................................................................................33
4.4. Alarms ....................................................................................................................................33
Summary of Contents for MultiZone
Page 52: ...Multi Zone Gas Monitors 46 P N 3015 5074 Rev 11 ...
Page 58: ...Multi Zone Gas Monitors 52 P N 3015 5074 Rev 11 ...
Page 60: ...Multi Zone Gas Monitors 54 P N 3015 5074 Rev 11 ...
Page 71: ...Multi Zone Gas Monitors P N 3015 5074 Rev 11 65 APPENDIX C SYSTEM MENU MAP ...
Page 72: ...Multi Zone Gas Monitors 66 P N 3015 5074 Rev 11 ...
Page 73: ...Multi Zone Gas Monitors P N 3015 5074 Rev 11 67 APPENDIX D AGENCY APPROVALS ...
Page 74: ...Multi Zone Gas Monitors 68 P N 3015 5074 Rev 11 ...
Page 76: ...Multi Zone Gas Monitors 70 P N 3015 5074 Rev 11 ...
Page 78: ...Multi Zone Gas Monitors 72 P N 3015 5074 Rev 11 ...