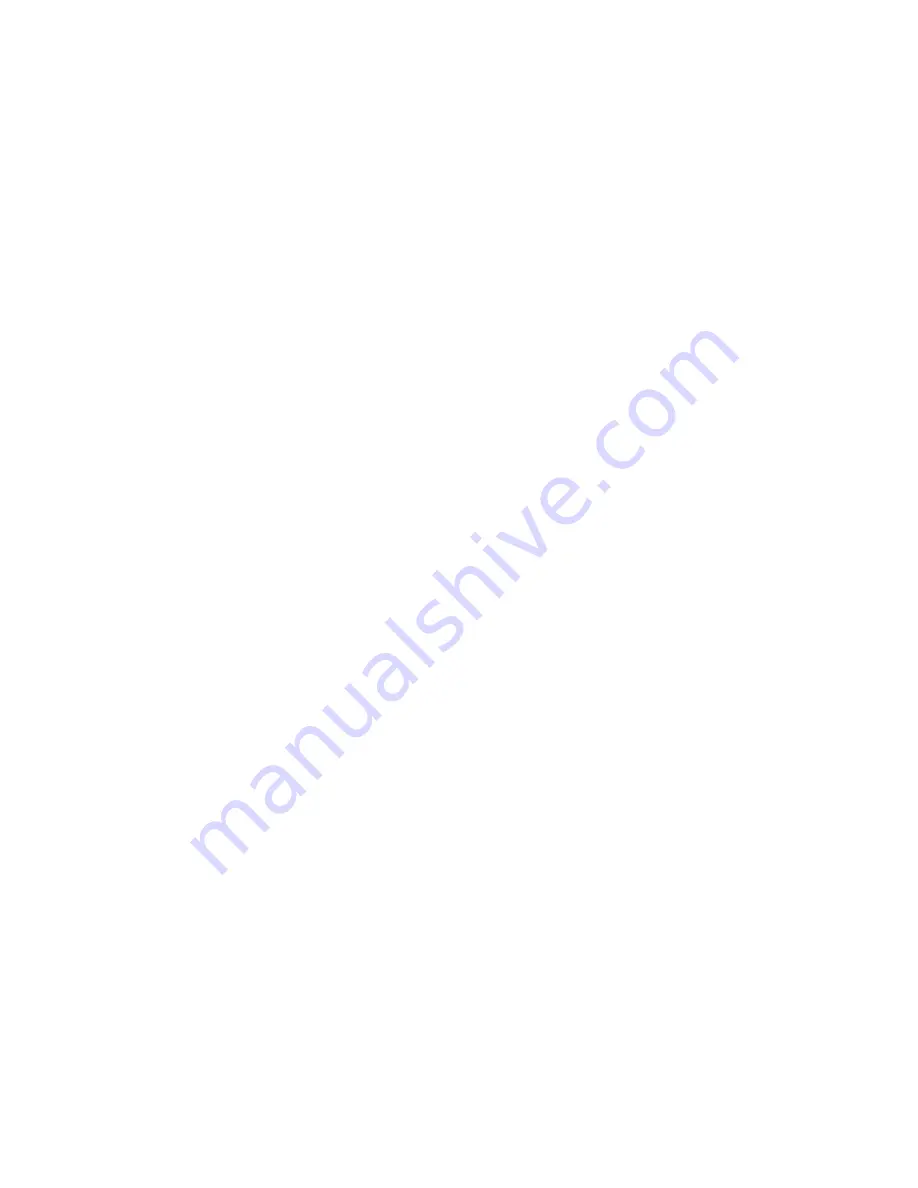
MODEL 300 COMBUSTION ANALYZER
Instruction 24-9223
6-1
6
REPLACEMENT PARTS, ACCESSORIES,
AND DIAGRAMS
This Section contains the following information:
• Replacement Parts List
• Wiring Diagram
• Accessories List
6.1
REPLACEMENT PARTS LIST
Item
Part Number
AC Power Supply:
120 VAC Input ....................................... 304-1706
240 VAC Input ......................................... 24-0508
Battery Pack.................................................. 24-0537
Battery Charger:
12 VDC Input ........................................... 24-0527
240 VAC Input ......................................... 24-0528
120 VAC Input ......................................... 24-0529
Control Panel Screw ..................................... 01-7276
Filter/Trap Assembly:
Complete Assembly.................................. 24-0642
Filter (Box of 3) ........................................ 24-0683
Instruction Manual ....................................... 24-9223
Printer Assembly:
Printer ...................................................... 24-0995
Paper (box of 5 rolls) ................................ 24-0980
Printer Screw ........................................... 01-7096
Probe Assembly:
Complete Assembly.................................. 24-7131
Knurled Nut ........................................... 102-0876
O-Ring ...................................................... 05-5124
Particulate Trap ....................................... 24-0477
Plug, K-Type (yellow body) ...................... 24-0615
Probe-Stop ................................................ 24-0434
Trap Plug ................................................. 24-0485