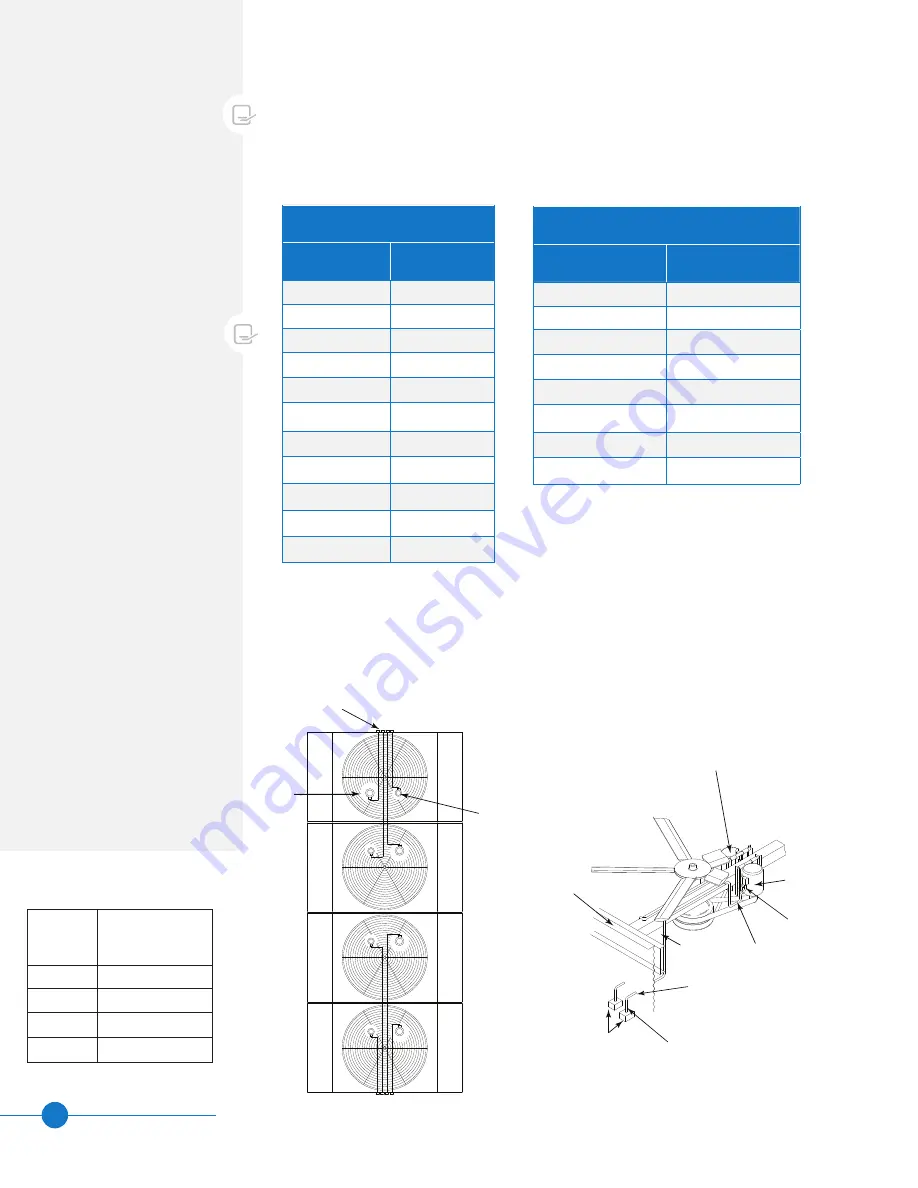
14
Motor Location and Conduit Installation
Use the following drawings and notes when installing electrical conduit for cooling towers
supplied with the BALTIDRIVE
®
Power Train, BALTIGUARD™ Fan System, gear drives, or
the ENDURADRIVE™ Fan System. Notice the table for weight adds for two-speed motors
and the BALTIGUARD™ Fan System.
Weights given in
Tables 6
and
7
represent the additional weight when an optional 2-speed
motor or BALTIGUARD™ Fan System is ordered. These weights should be added to the
standard unit weight.
BALTIGUARD™ Fan System Motor Weight Add
Motor HP
Weight (lbs)
3
100
5
110
7.5
160
10
175
15
300
20
260
25
390
30
440
Table 6.
2-Speed Motor Weight Add
[1]
Table 7.
BALTIGUARD
™
Fan System Motor Weight Add
[2]
2-Speed Motor Weight Add
Motor HP
Weight (lbs)
7.5
140
10
185
15
90
20
80
25
210
30
170
40
225
50
300
60
425
75
340
100 (gear only)
600
Figure 19.
Belt Drive Motor Location(s) for Models that Ship in One Section
See Note 4
on Page 14
Main Fan
Motor
Optional
BALTIGUARD™
Fan System Motor
Face A
Face B
Face B
Face A
Face B
Face A
Face B
Face A
CT-4
CT-3
CT-2
CT-1
Optional
BALTIGUARD™
Fan System Motor
Main Fan Motor
Conduit Box
Flexible Conduit (Allow Sufficient
Slack for Belt Tensioning)
Rigid Conduit
Hole in Casing Panel Should be Large
Enough to Accommodate Conduit
Seal with Waterproof Sealant
Rigid Conduit Outside Tower Turned
Down to Junction Box or Safety
Switch
Disconnect/Safety Switch
in Weatherproof Enclosure
Must be Rated for Proper
Voltage and Horsepower of
Fan Motor
Motor Detail for Main Motor (BALTIDRIVE® Power Train)
or BALTIGUARD™ Fan System (If Ordered)
Connection End
of Unit
Plan View
Number
of Cells
Configuration
1
CT-1
2
CT-1 & CT-4
3
CT-1, CT-2 & CT-4
4
CT-1 through CT-4
NOTES FOR FIGURES 19-21:
1.
Conduit must be water tight
and pitched downward to
allow condensation to drain
away from fan motor conduit
box. Therefore, do not run the
conduit through fan deck.
2.
All wiring must conform to
local and national electrical
codes. Junction box/safety
switch and all conduit from
fan motor conduit box to be
sized, provided, and installed
by others.
3.
Rigid conduit outside casing
panel must turn down to
junction box.
4.
On multi-cell units, use
separate conduit lines for
each fan motor. Run conduit
through adjacent cells to
junction box and or disconnect
switch on front/rear cell.
NOTE:
1.
Weights given represent the
additional weight when a
2-speed motor is ordered
and should be added to the
standard unit weight.
2.
If the optional BALTIGUARD™
Fan System is ordered, weights
given are for each BALTIGUARD
motor and should be added to
the standard unit weight.