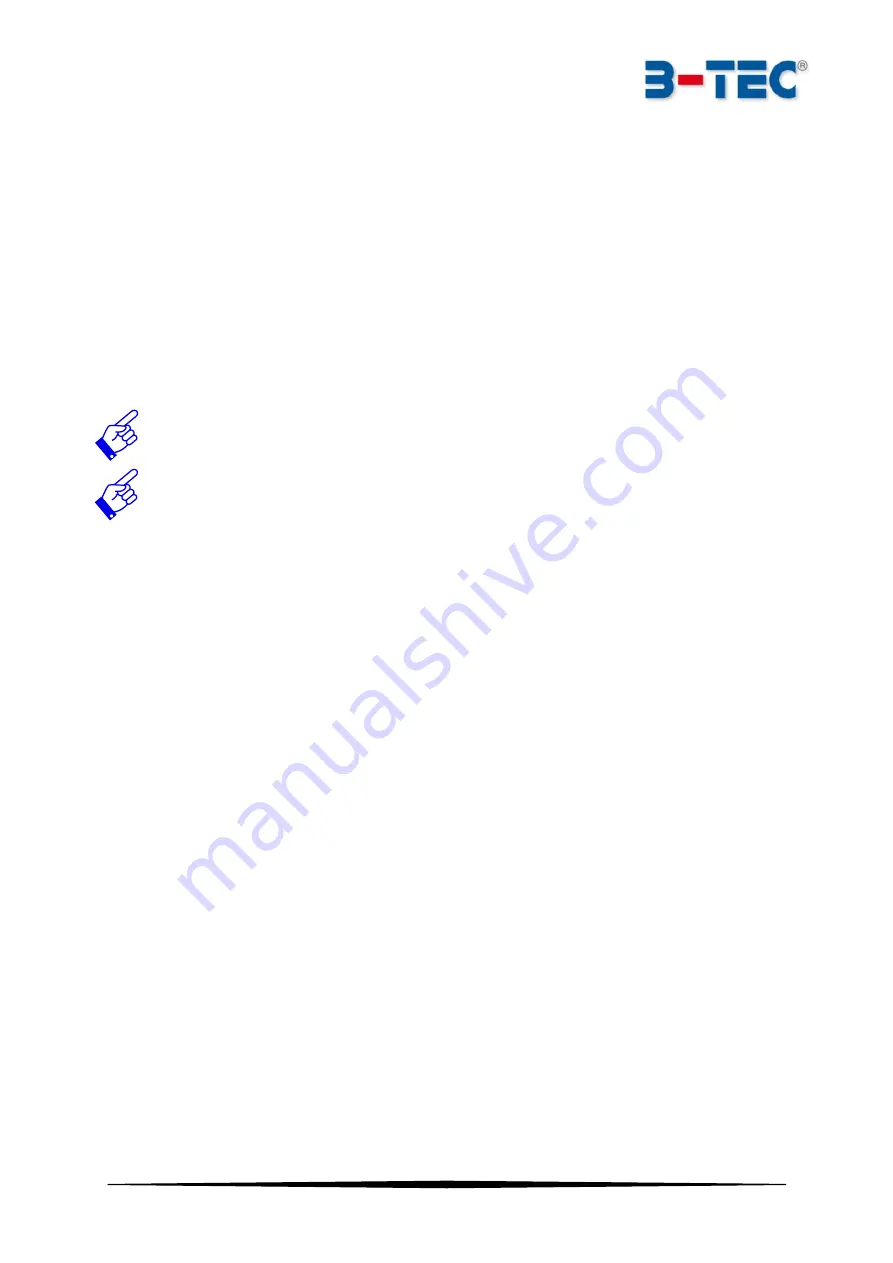
Cleaning Device d-800 Page 21
equipment and facility engineering
7.
Since the solvent is circulated when the timer is used, it will be heavily contaminated after a
certain period. If a paint film remains on the spray gun after the main cleaning cycle, the gun
has to be cleaned manually using the fresh solvent jet.
8.
For automatic rinsing, close the door again and press and hold the rinse button (red button)
for 3-4 seconds. Thinner is drawn from the 30 l drum on the left side. The spray gun is rinsed
on the inside and outside with fresh thinner.
9.
Open the door to the automatic cleaning chamber and dry the spray gun with the cup and
cover in their mounting brackets. Use the jet gun for this procedure.
10.
The spray gun is clean. Reassemble and bring it back into production.
Clean the spray gun as soon as possible after the painting process.
Before insert the spray gun, unscrew the cover from the cup and empty out the remaining
paint into a collecting container. For example the B-TEC residue collecting station RST-01.
The more thoroughly the cup is emptied, the longer the solvent or cleaner can be used.
Following these steps will ensure optimal cleaning results and long machine life.
8.3 Adjusting Facilities
Slightly above the pumps are color-coded throttle-valves for following adjusting:
Green: Brush
Blue: Clear rinse
Red: Jet automatic (After Y-connector explicitly adjusting of the hose for flushing spray guns.)