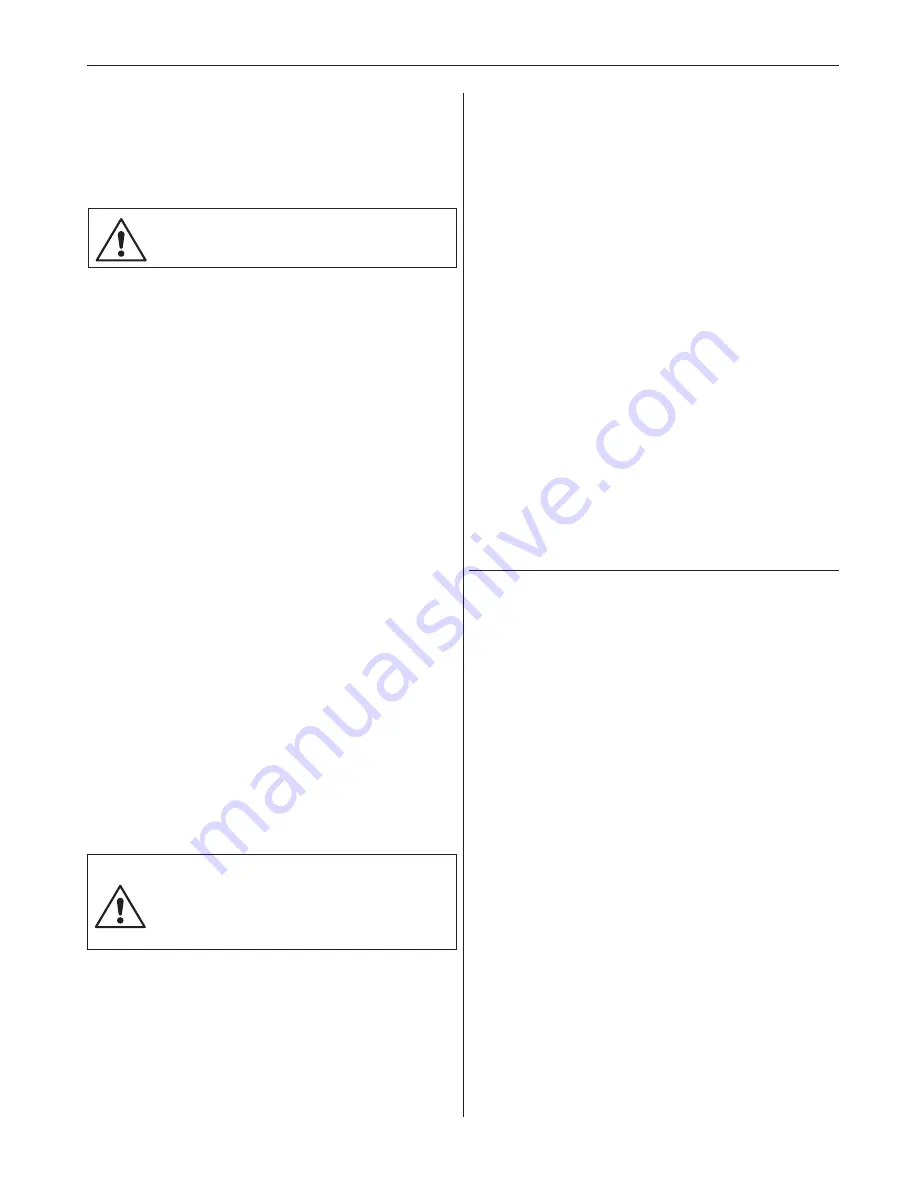
General Instruction for 230V Machines
7
These machines are supplied with a moulded 16 Amp
plug and 3 core power cable. Before using the machine,
inspect the cable and the plug to make sure that neither
are damaged. If any damage is visible, have the damaged
item inspected/repaired by a suitably qualified person.
If it is necessary to replace the plug, it is preferable to
use an ‘unbreakable’ type that will most resist damage.
Only use a 16 Amp plug, and make sure the cable clamp
is tightened securely. Fuse as required. If extension leads
are to be used, carry out the same safety checks on them,
and ensure that they are correctly rated to safely supply
the current that is required for your machine. Remember,
most machines or tools have handles or holding
positions, the power cable is not one of them.
Good Working Practices/Safety
Mains Powered Tools and Machines
Primary Precautions
Workplace/Environment
The following suggestions will enable you to observe
good working practices, keep yourself and fellow
workers safe and maintain your tools and equipment in
good working order.
WARNING!! KEEP TOOLS AND EQUIPMENT OUT
OF THE REACH OF YOUNG CHILDREN
KEEP THE WORK AREA AS UNCLUTTERED AS
IS PRACTICAL, THIS INCLUDES PERSONNEL
AS WELL AS MATERIAL. UNDER NO
CIRCUMSTANCES SHOULD
CHILDREN BE ALLOWED IN WORK AREAS.
The machine is not designed for use outside. Keep the
machine clean; it will enable you to more easily see any
damage that may have occurred. Clean the machine with
a damp soapy cloth if needs be, do not use any solvents
or cleaners, as these may cause damage to any plastic
parts or to the electrical components. It is good practice
to leave the machine unplugged until work is about
to commence, also make sure to unplug the machine
when it is not in use, or unattended. To avoid inadvertent
‘start up’, if your machine is not fitted with a NVR system,
ensure the switch is always returned to the OFF position.
Once you are ready to commence work, remove any
tools, objects or items that could inadvertently get
‘sucked up’ by the machine and place safely out of the
way. Re-connect the machine, ensuring the power cable
is not ‘snagged’ or routed where it could be tripped over
as you move about the workshop; it is not too close to
an unguarded heat source, or is laid over or around a
sharp edge. If the work you are carrying out is liable to
generate flying grit, dust or chips, wear the appropriate
safety clothing, goggles, gloves, masks etc. If the work
operation appears to be excessively noisy, wear
ear-defenders. If you wear your hair in a long style,
wearing a cap, safety helmet, hairnet, even a sweatband,
will minimise the possibility of your hair being caught
up in the rotating parts of the machine, likewise,
consideration should be given to the removal of rings
and wristwatches if these are liable to be a ‘snag’ hazard.
Consideration should also be given to non-slip footwear,
etc.
Do not
use this machine if you are tired, your attention is
wandering or you are being subjected to distraction.
Do not
use this machine within the designated safety
areas of flammable liquid stores or in areas where there
may be volatile gases. There are very expensive, very
specialised machines for working in these areas. Above
all,
OBSERVE….
make sure you know what is happening
around you, and
USE YOUR COMMON SENSE.
Specific Safety for Dust
Extractors
Do not
use this machine as a vacuum cleaner, try to keep
the waste medium to wood by products.
Do not
uplift workshop floor debris (stones, nails, screws,
paper etc., etc). Be aware that wood dust is an explosive
medium.
Do not
allow any ‘naked light’ source to occur anywhere
near the machine. This includes cigarettes, matches, etc,
and do not place the machine near any unprotected
light bulbs, that could possibly get broken.
The suction force is generated by a high speed fan unit.
This has the potential to amputate fingers, grab loose
clothing (ties etc.,) and ‘bat’ large chips etc, at high
speeds. Keep all guarding in place, and if access to the
fan becomes necessary (due to blockage etc.,)
Disconnect the machine from the mains supply and
ensure the fan has come to a complete stop before
putting your hands anywhere near to it.
If you are not using ‘clear’ extraction hose, periodically
remove the hose to check that the inlet to the machine
is not getting restricted. (The safety guard grill of the
inlet duct can be particularly irksome in this way, as long
strand shavings etc., can wrap around the grill fret.)
Keep the particle filter clean. The machine relies on its
ability to ‘blow’ air through the filter, to generate good
Summary of Contents for CT-90H
Page 4: ...What s Included 4 CT 90H Extractor 1 6 7 8 9 10 11 12 2 3 4 5 ...
Page 6: ...What s Included 6 CT 90HB Extractor 23 26 27 a b c d e f g h i j k 24 25 ...
Page 23: ...Exploded Diagram Parts List 23 CT 90H ...
Page 24: ...Exploded Diagram Parts List 24 CT 90HB ...
Page 26: ...Exploded Diagram Parts List 26 CT 90H Filter Assembly CT 90HB Filter Assembly ...