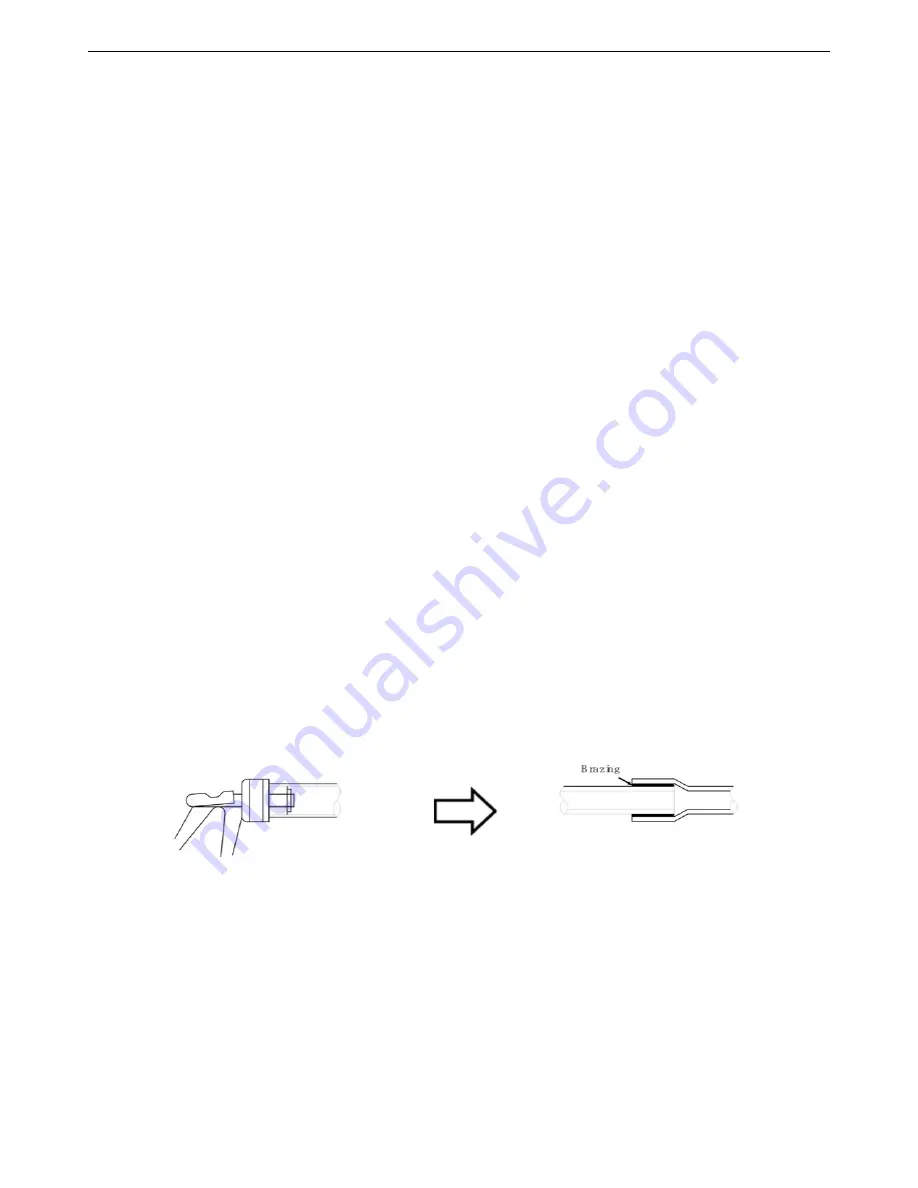
R32
Split Type - Air Source Heat Pump 20220105
54
2.5 Manipulating Copper Piping
2.5.1 Deoiling
Notes for installers
Lubrication oil used during some copper pipe manufacturing processes can cause deposits to form in R32
refrigerant systems, causing system errors. Oilfree copper piping should therefore be selected. If ordinary (oily)
copper piping is used, it must be cleaned with gauze dipped in tetrachloroethylene solution prior to installation.
Caution:
Never use carbon tetrachloride (CCl4) for pipe cleansing or flushing, as doing so will seriously damage the
system.
2.5.2 Cutting copper piping and removing burrs
Notes for installers
Use a pipe cutter rather than a saw or cutting machine to cut piping. Rotate the piping evenly and slowly,
applying even force to ensure that the piping does not become deformed during cutting. Using a saw or cutting
machine to cut piping runs the risk of copper shavings entering the piping. Copper shavings are difficult to
remove and pose a serious risk to the system if they enter the compressor or block the throttling unit.
After cutting using a pipe cutter, use a reamer/scraper to remove any burrs that have formed at the
opening,keeping the opening of the piping downwards to avoid copper shavings from entering the piping.
Remove burrs carefully to avoid scratches, which may prevent a proper seal being formed and lead to
refrigerant leakage.
2.5.3
Expanding copper piping ends
Ends of copper piping can be expanded so that another length of piping can be inserted and the joint
brazed.
Insert the expanding head of the pipe expander into the pipe. After completing pipe expansion, rotate the
copper pipe a few degrees to rectify the straight line mark left by the expanding head.
Caution
Ensure that the expanded section of piping is smooth and even. Remove any burrs that remain after cutting.
Expanding copper piping ends
2.5.4 Flared joints
Flared joints should be used where a screw thread connection is required
Notes for installers
Before flaring 1/2H (half hard) piping, anneal the end of the pipe to be flared.
Remember to place the flare nut on the piping before flaring.
Ensure the flared opening is not cracked, deformed or scratched, otherwise it will not form a good seal and
refrigerant leakage may occur.
The diameter of the flared opening should be within the ranges specified
When connecting a flared joint, apply some compressor oil to the inner and outer surfaces of the flared
opening to facilitate the connection and rotation of the flare nut, ensure firm connection between the sealing