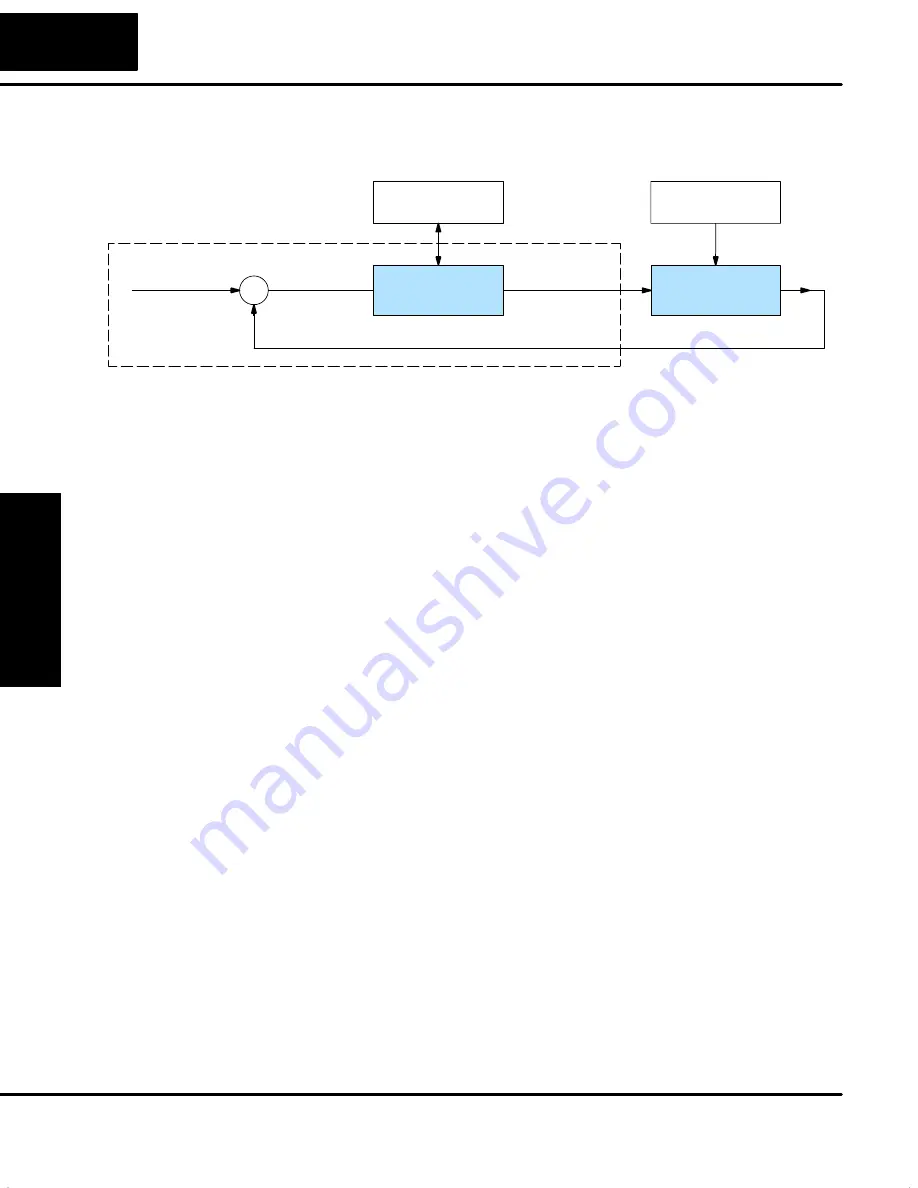
PID Loop Operation
Maintenance
and T
roubleshooting
8–4
PID Loop Operation
The key parts of a PID control loop are shown in the block diagram below. The path
from the PLC to the Manufacturing Process and back to the PLC is the “loop” in
“closed loop control.”
Process Variable
Loop
Calculation
Manufacturing
Process
Setpoint Value
Loop Configuring
and Monitoring
Control Output
External
Disturbances
S
Error Term
+
–
PLC System
Manufacturing Process
– the set of actions that adds value to raw materials. The
process can involve physical changes and/or chemical changes to the material. The
changes render the material more useful for a particular purpose, ultimately used in
a final product.
Process Variable
– a measurement of some physical property of the raw materials.
Measurements are made using some type of sensor. For example, if the
manufacturing process uses an oven, you will most likely want to control
temperature. Temperature is a process variable.
Setpoint Value
– the theoretically perfect quantity of the process variable, or the
desired amount which yields the best product. The machine operator knows this
value, and either sets it manually or programs it into the PLC for later automated use.
External Disturbances
– the unpredictable sources of error which the control
system attempts to cancel by offsetting their effects. For example, if the fuel input is
constant an oven will run hotter during warm weather than it does during cold
weather. An oven control system must counter-act this effect to maintain a constant
oven temperature during any season. Thus, the weather (which is not very
predictable), is one source of disturbance to this process.
Error Term
– the algebraic difference between the process variable and the
setpoint. This is the control loop error, and is equal to zero when the process variable
is equal to the setpoint (desired) value. A well-behaved control loop is able to
maintain a small error term magnitude.
Loop Calculation
– the real-time application of a mathematical algorithm to the
error term, generating a control output command appropriate for minimizing the
error magnitude. Various control algorithms are available, and the DL05 uses the
Proportional-Integral-Derivative (PID) algorithm (more on this later).
Control Output
– the result of the loop calculation, which becomes a command for
the process (such as the heater level in an oven).
Loop Configuring
– operator-initiated selections which set up and optimize the
performance of a control loop. The loop calculation function uses the configuration
parameters in real time to adjust gains, offsets, etc.
Loop Monitoring
– the function which allows an operator to observe the status and
performance of a control loop. This is used in conjunction with the loop configuring to
optimize the performance of a loop (minimize the error term).
The Basics of
PID Loops
Summary of Contents for DL05
Page 1: ...DL05 User Manual Automationdirect com ...
Page 2: ...DL05 User Manual Automationdirect com ...
Page 436: ...1B DL05 Error Codes In This Appendix Ċ Error Code Table ...
Page 443: ...1C Instruction Execution Times In This Appendix Ċ Introduction Ċ Instruction Execution Times ...
Page 459: ...1D Special Relays In This Appendix Ċ DL05 PLC Special Relays ...
Page 464: ...1E DL05 Product Weights In This Appendix Ċ Product Weight Table ...