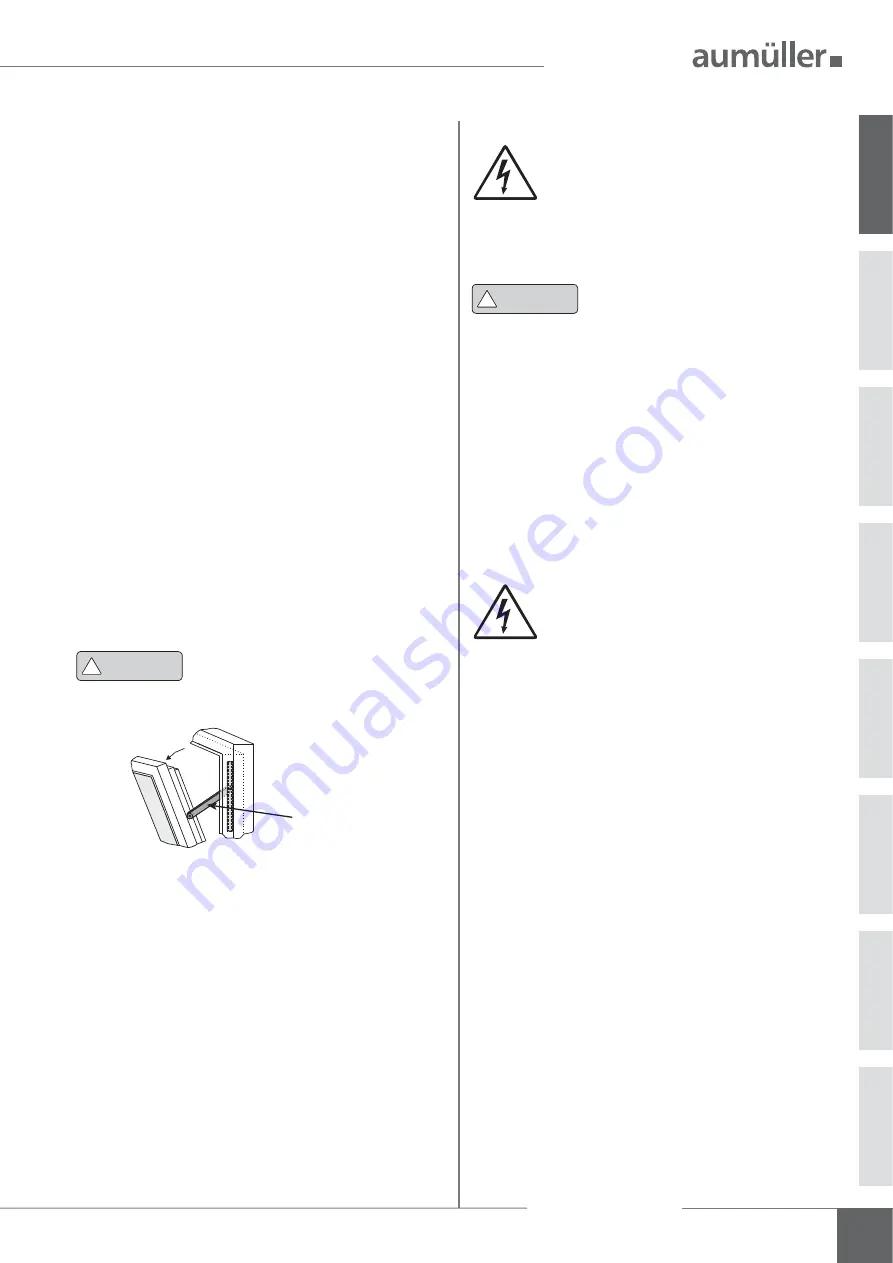
7
Assembly Instruction
KS 4 S12 24V DC R
S
AFETY
INSTRUCTIONS
safety scissors
!
W
ARNING
!
W
ARNING
Crush and shear points
To avoid injuries,
crushing and shear points
between
casement and frame must be secured
against entrapment
up to an installation height of 2,5 meters above the
fl oor
with appropriate measures. This can be achieved e.g.
by using contact-based or contactless protective devices
against entrapment, which stop the motion through cont-
act or through interruption by a person. At a force higher
than 150 N at the main closing edge the motion must stop
within 20 mm. A warning symbol at the opening element
must indicate this clearly.
Unintentional or independent opening or falling
Casements are to be hinged or secured such way that in
case one of the mounting elements fails it will not crash /
slam down or move in an uncontrolled manner by e.g. using
double suspensions, safety scissors, casement stays.
Tilting windows shall be equipped with safety scissors or
similar devices to avoid damages and risks of injury for
persons through improper installation and operation. The
safety scissors must be adjusted to the opening stroke of
the drive (see technical data) to avoid blocking. The opening
width of the safety scissors must be bigger than the drive
stroke.
Routing cables and electrical connection
Routing or installing electrical lines and connections may
be performed only by approved specialist companies. Never
operate drives, control units, operating elements and sen-
sors at operating voltages and connections contrary to the
specifi cations of the manufacturer.
All relevant instructions shall be observed for the in-
stallation, specifi cally:
• VDE 0100 Setting up high-voltage systems up to 1000 V
• VDE 0815 Wiring cables
• Specimen Guideline on Conduits German designation
(MLAR).
Commissioning, operation and maintenance
After the installation and after each modifi cation in the set
up all functions shall be checked with a trial run. It shall
be ensured that drive and casement are set correctly and
that security systems, if available, are functioning properly.
After the installation of the system is completed the
end-user shall be introduced to all important operating
steps. If necessary, he must be advised of all remaining risks /
dangers.
The end-user shall be instructed in intended use of the
drives and, if necessary, the safety instructions. The end-user
shall be specifi cally instructed that no additional forces,
except for the pressure and tension in the opening and
closing direction of the casement, may be applied to the
spindle, chain or lever of the drive.
The types of cable, cable lengths and cross-sections shall
be selected in accordance with the manufacturer’s technical
data. If necessary, the cable types shall be coordinated with
the competent local authorities and energy supply com-
panies. Low-voltage lines (24 V DC) shall be routed
separate from the high-voltage lines. Flexible cables may
not be fl ush-mounted. Freely suspended cables shall be
equipped with strain reliefs.
Clamping points shall be checked for tightness of threa-
ded connections and cable ends. Access to junction boxes,
clamping points and external drive control systems shall be
ensured for maintenance work.
Damaged mains supply lines of drives
with plug connectors may only be re-
placed by the manufacturer or qualifi ed
service / maintenance personnel!
Power cables which are fi xed to the drive
casing cannot be replaced. If the cable is
damaged the device must be scrapped!
The movable casement must be secured
against unintentional or independent
opening as well as falling down.
All-pole disconnecting devices shall be instal-
led in the permanent electrical installation or
external Control Unit for the drive.
The mains supply lines 230 V / 400 V AC shall
be protected separately!
Cables must be laid such way that they cannot
be sheared off, twisted or bent during opera-
tion. Drive cables laid into closed window
profi les must be protected by insulating
tubes with a suffi cient temperature resistance.
Through holes shall be equipped with cable
sleeves!
01