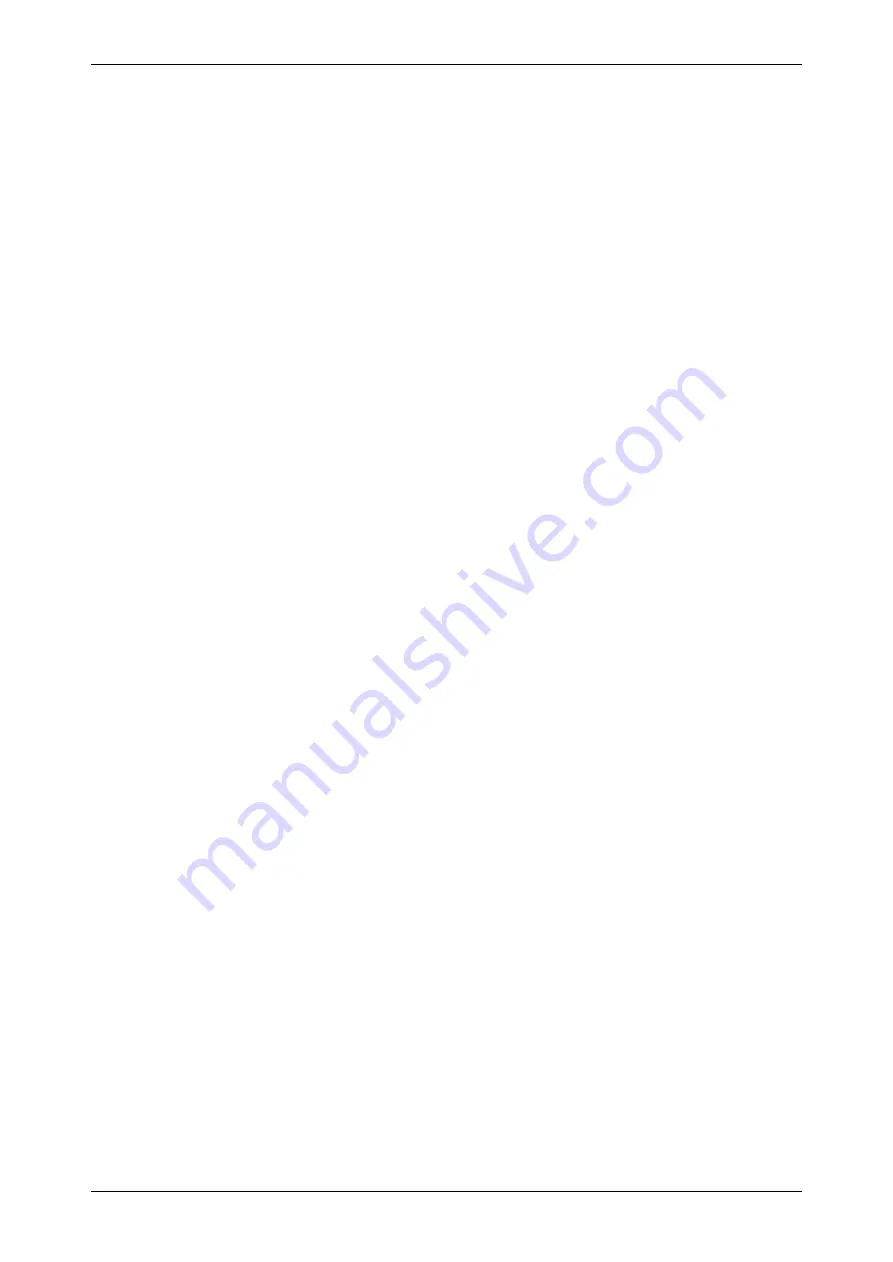
COMMISSIONING
62
| MVE User Manual (710-17074-00G)
5.
Either
•
check the test report on insulation resistance values for motor, input and output cables etc., or
•
witness the test performed by others
6.
Check that the auxiliary/control supply is as expected.
1.
Measure and record the voltage between each phase and a neutral point.
2.
Measure and record the voltage between each phase and earth.
7.
Check that the neutral point is properly earthed (at least on the LV supply transformer side, but preferably also at the
main distribution board).
Measure and record the voltage between the neutral point and earth.
•
Check that the voltage at all electronic power supply connectors is 22-26 VAC.
•
Check that the voltage for the contactors (at the connector block) match the voltage for the contactor coil circuit (as
specified on schematic diagrams, see 13-A2).
8.
Connect the 24 VAC connector to the power interface PCB. Ensure that the power supply LED illuminates and the
fibre-optic TX LED flashes. For more information on LED locations, see
Terminations on the Power Interface Board
on
page 20.
9.
Connect the 24 VAC connector to the controller. Ensure that the start-up message is displayed on the LCD (indicating the
software versions, see
User Manual Version
on page 2).
10.
Connect the 24 VAC connectors to the gate drive circuits. Ensure that the LEDs on each circuit board illuminate. For
more information on the gate drive board applicable to your product version,
see Terminations for Adapter Board and
Gate Drive Board
on page 22.
8.3
Operating Tests
Motor simulation
Use the MVE simulation functions to ensure that the soft starter is connected correctly to associated equipment.
1.
Disconnect the soft starter from the mains supply.
2.
Set the date and time and all necessary parameters.
3.
Operate the Run Simulation using the keypad on the controller (see
Run Simulation
on page 33).
1.
Check that the relays on the power interface PCB operate and activate the MV contactors. Also ensure that the firing
signals are received at the gate drive board on each phase’s power assembly.
2.
Check that the following LEDs activate at each stage of the simulation (see
Terminations on the Power Interface
Board
on page 20):
•
LEDs ‘FIRE 1’ and ‘MC’ during starting
•
LEDs ‘FIRE 2’, ‘BC’ and ‘BPR’ during running
•
LEDs ‘FIRE 3’ and ‘MC’ during stopping.
4.
Operate the Protection Simulation and confirm that the MVE responds as expected (see
Protection Simulation
on page
5.
Operate the Output Signal Simulation and confirm that the MVE provides output signalling as expected (see
Output
Signal Simulation
on page 34).
6.
Confirm that the soft starter trips if the thermistor link is not present.
Low Voltage Test Mode
The MVE can be connected to a low voltage motor (
≤
500 VAC) for testing. To conduct the low voltage test you need to use an LV
motor test resistor assembly (part number 995-03946-00). This allows the user to thoroughly test the soft starter and its
associated power and control circuits. The low voltage test mode provides a means of testing the soft starter's configuration
without requiring a full medium voltage test facility.
During the low voltage test, the soft starter's control input, relay output and protection settings can be tested. Low voltage mode is
not suitable for testing soft starting or soft stopping performance.
The FLC for the low voltage motor must be
≥
5 A (see parameter 1A
Motor Full Load Current
). The typical value for parameter 2D
Current Limit
is 130%.