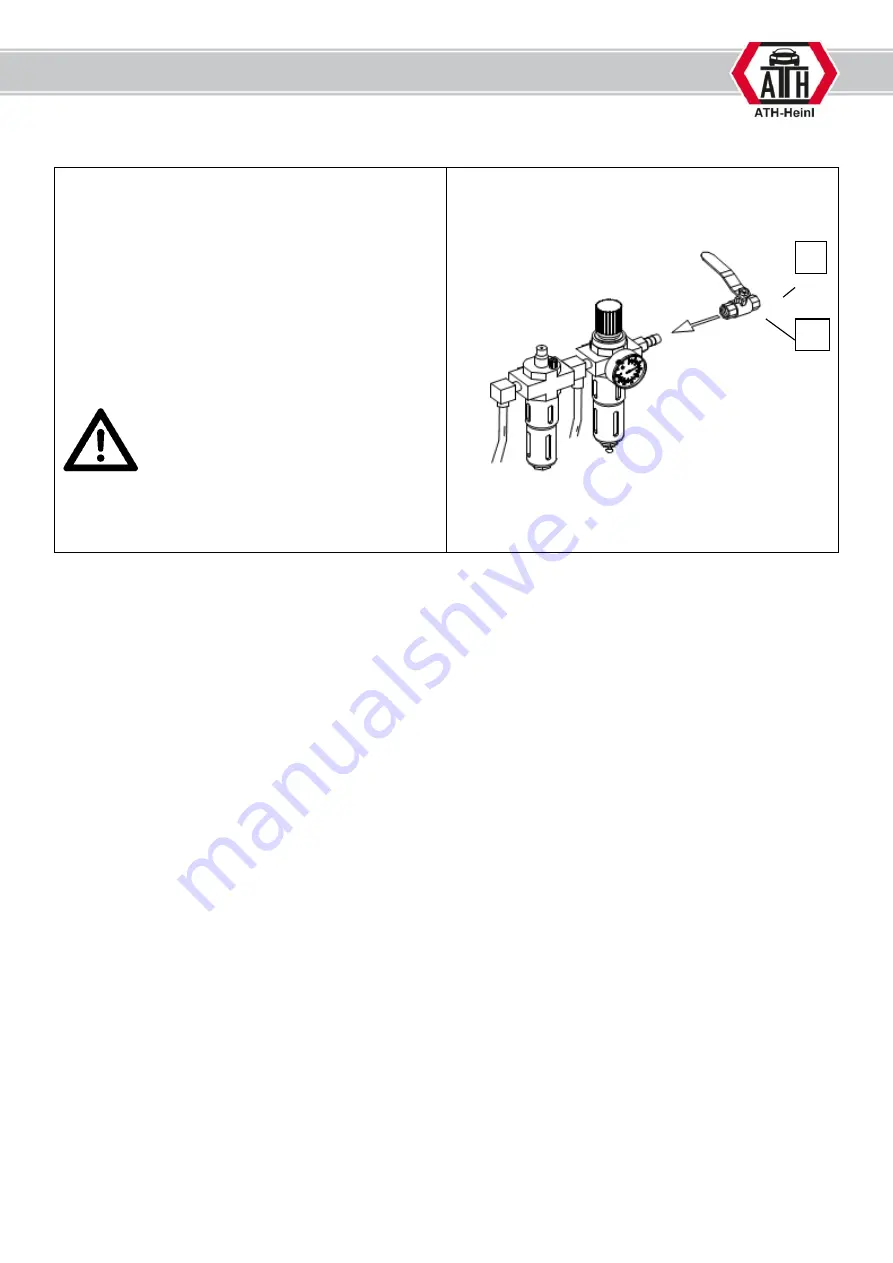
© Copyright ATH-Heinl GmbH & Co. KG, 2017, All rights reserved. / Printing errors and technical changing´s reserved / Version: 02/2017
- 22 -
9.
Pneumatic connection
The air pressure should correspond to the technical
data.
The maximum or minimum pressure guarantees a
perfect function without any damage.
It is recommended to use a shut-off valve (D -
NOT included).
Connect the compressed air supply to the
maintenance unit (4).
For correct setting, all instructions in the article
"Maintenance and Service Instructions" must now
be observed.
D
4
Summary of Contents for ATH W82
Page 2: ...USER S MANUAL ATH W82 ...