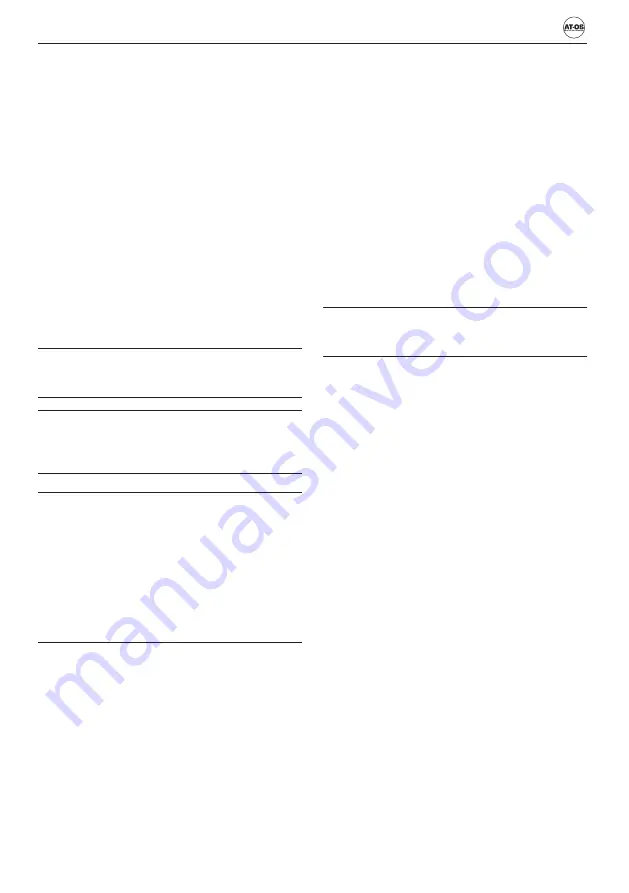
English
25
Sequence:
- Fill the insert by arranging the trays in the specific
slots;
- Insert the insert in the basket;
- Insert the basket in the tank up to the stop;
- Close the door, start the program.
Instruments: Surgical Instruments
Insert type: Instrument holder insert
Sequence:
- Fill the insert by placing the trays in the appropriate
slots upside down;
- Insert the insert in the basket;
- Insert the basket in the tank up to the stop;
- Close the door, start the program.
HAZARD. Be very careful when inserting pointed or
sharp instruments. Always insert the instruments
starting from the bottom, and possibly wearing
protective gloves.
b
Perforated baskets and supports do not
provide protection against pointed and/or
sharp instruments.
a
WARNING. Failure to follow these
recommendations may cause injury. Pay the
utmost attention when loading/unloading
the instruments to be washed.
6.2.4 Treatment of dental instruments
a
WARNING.
Insert
only
instruments
suitable for automatic treatment in
thermodisinfector devices, according to the
manufacturer’s instructions. In particular,
follow the information provided by the same
manufacturer. Despite compliance with
the manufacturer’s instructions, in case of
damage or alteration of the instruments, the
responsibility will be borne by the instrument
manufacturer.
Correct program
Before starting the treatment, check that:
- The external surface of the instruments is clean of
material residues (E.g. dental cement, etc.).
- The air and spray channels must be clean.
- Finally, carry out a test.
Use the recommended liquids (see paragraph «5.5.2
Liquid use and storage»).
Care of the instruments
Major manufacturers recommend drying the spray/
air/water channels immediately after cleaning and
disinfection using clean compressed air with suitable
maintenance products.
It is recommended to follow the specific instructions.
6.2.5 Treatment of ophthalmic instruments
- Only insert instruments designed for automatic
treatment in thermodisinfector. Carefully follow
the instructions provided by the instrument
manufacturer.
- Do not insert instruments intended for interventions
on the optic nerve and which come into contact with
the retinal tissue.
In case of damage or alteration of the instruments
despite compliance with the manufacturer’s
instructions, the responsibility will still be borne by the
instrument manufacturer.
a
WARNING. The treatment of ophthalmic
instruments requires the use of purified
water.
Comply with the following for automatic treatment:
- Use a slightly alkaline liquid for cleaning. Use a citric
acid-based neutraliser for neutralisation. Never use
liquids for rinsing.
- Rinse the hollow instruments after the application
and check that the purified water passage is free
before the automatic treatment.
- Insert the hollow instruments into the rinse bar,
specially designed for this use.
- Make sure that no deposits form on the instruments.
- Dry the hollow instruments with compressed air
after the treatment in order to remove all residual
humidity.
- Follow the manufacturer’s instructions with regard
to the maintenance of instruments/accessories for
loading.
6.3 Programs
The machine leaves the factory programmed with
three separate use programs already entered in the
settings menu.
To select the programs available, use key 1, 2 or 3
(on the control panel Fig. 12) depending on the most
suitable program for the level of dirt of the load.
The following table shows the correct programs for
each type of load.