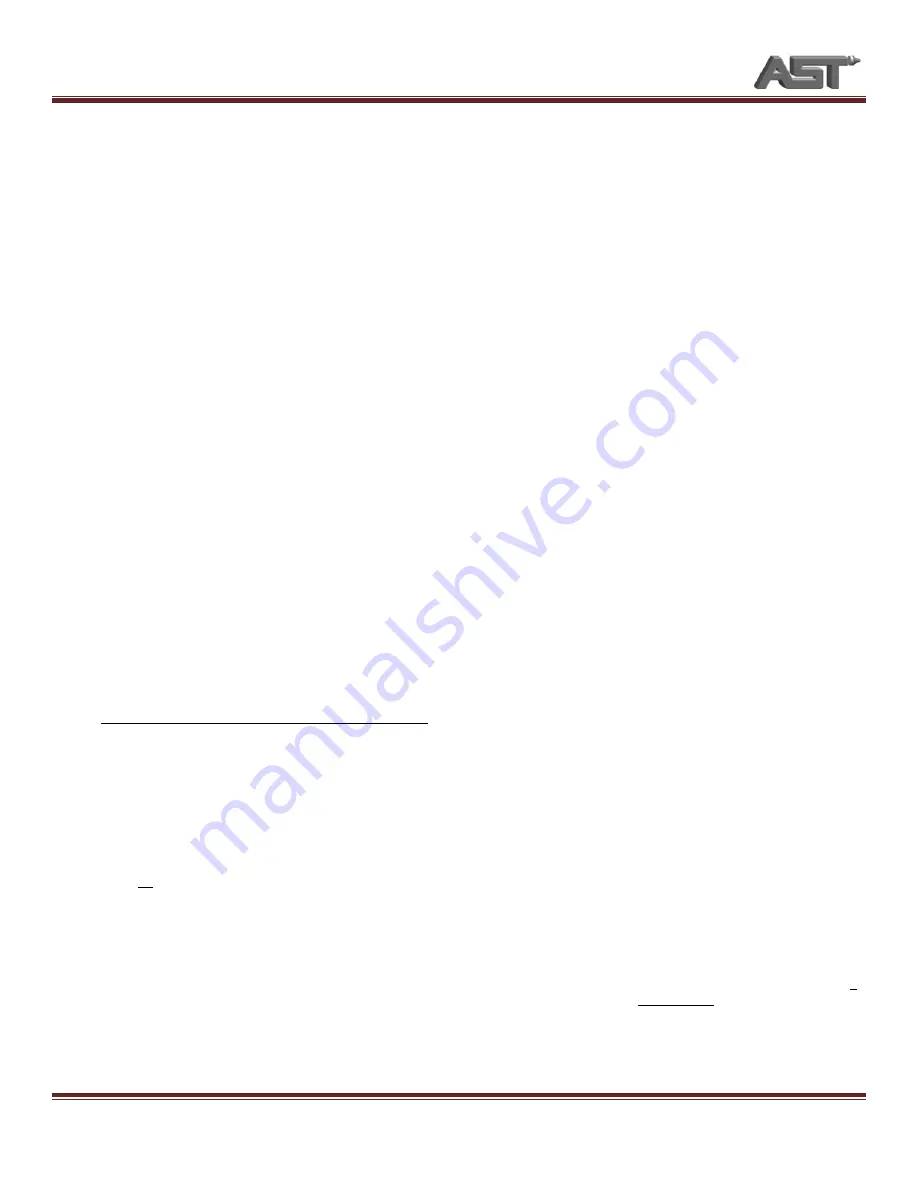
SHUT-DOWN PROCEDURES
60089-05
Page 10
PUMP CLEANING PROCEDURE
The following is the recommended procedure for removing,
inspecting, cleaning and reinstalling GMP pumps. Please
use all safety devices such as but not limited to gloves and
eye protection. When working with solvents do so in a well-
ventilated area free of combustible items. Take every effort
not to mar or damage any surfaces that come in contact
with materials.
Disassembly
o
Remove tank & inlet [assuming all material has been
removed from tanks].
Open bleed valve on top of inlet block, if supplied.
Remove tank straps, if supplied.
Remove (3) of the 4 bolts attaching inlet to back of
pump
Loosen fourth bolt to allow inlet to come off pump
and drain any remaining material. Remove bolt and
tank after enough material is drained.
Discard o-ring between inlet & pump (12498).
Clear any foreign objects, crystallized or partially
hardened material from tank & inlet block.
Cleaning of residues from pump
o
Partially disassemble & clean pump
Remove four bolts attaching inlet to back of pump.
Back of pump should pull off shaft & front section.
Excessive force should be used only with extreme
caution to prevent damage to the pump (Be careful
to not lose the two alignment pins, which prevent
incorrect assembly of pump. Clean pins if
necessary).
Clean bolts of any material.
Prevent any damage to all interior surfaces of pump.
Carefully remove outer stator ring housing.
Assuming that any crystallized material is located
between stator (internal teeth) and rotor (external
teeth), soak area in contact with material in a
compatible solvent to soften.
Gently remove & clean stator. Rotor should be
carefully cleaned at this time while still mounted on
pump shaft. Use nylon brushes instead of steel if
possible to preserve surface finished.
Keep all parts, except for o-rings.
All residues of old material are to be removed from
all internal surfaces of the pump parts.
Test to see if pump shaft can be turned.
Check to see if motor will turn by turning on the
machine briefly.
Remove chain and turn sprocket. Use a wrench,
if necessary.
If pump shaft will turn, further disassembly is
unnecessary unless material is leaking from
shaft seals (check behind drive sprocket).
Once completely clean, re-assemble pumps. *Note:
Mechanical side of pumps cannot be assembled
incorrectly if the two (2) guide pins are in place.
Use new o-rings. The use of petrolatum grease is
recommended to lubricate all internal surfaces
immediately before installation and may make re-
assembly easier along with future servicing of
pump.
Lubricate pumps using zerks supplied. Use only
petrolatum grease for this purpose.
SHORT TERM SHUTDOWN PROCEDURE:
The following
is the recommended procedure for storing equipment for a
short period of time. Please note that some items included
in this procedure are not included with all supplied
equipment. Please use all safety devices such as but not
limited to gloves and eye protection. When working with
solvents do so in a well-ventilated area free of combustible
items. Take every effort not to mar or damage any surfaces
that come in contact with materials.
Pump Unit Dry
o
Pump remaining material.
Remove static mixer and/or spray attachment.
Operate machine until no material is being
dispensed. Check that hoses are allowed to drain
completely (hoses should lead “downhill” towards
dispense valve).
Clean dispense valve & reapply layer of compatible
lubricant.
o
Flush System
Use only a cleaning solution most effective for
removing your material. Consult material
manufacturer for recommendations. Carefully
observe all health and safety precautions listed on
all labeling.
Fill each tank a minimum of 1/3 with a compatible
cleaning solution.
Set pump speed control to slow setting.
Operate machine until cleaning solution begins to
come out of the machine.
Allow machine to sit for a period of time, depending
on the effectiveness of the cleaning solution, not
more than one hour. Most solvents will not damage
any component unless allowed to remain in system.
Continue pumping cleaning solution into container
until machine is again empty. Observe cleaner as it
is being pumped. As solution is pumped, it should
appear to become clean. If this is not observed, the
same cleaner, after impurities have settled, can be
re-loaded into machine and procedure repeated – if
it is pumped out immediately. Do not allow any
settled material back into system.
(Continued on Page 11)