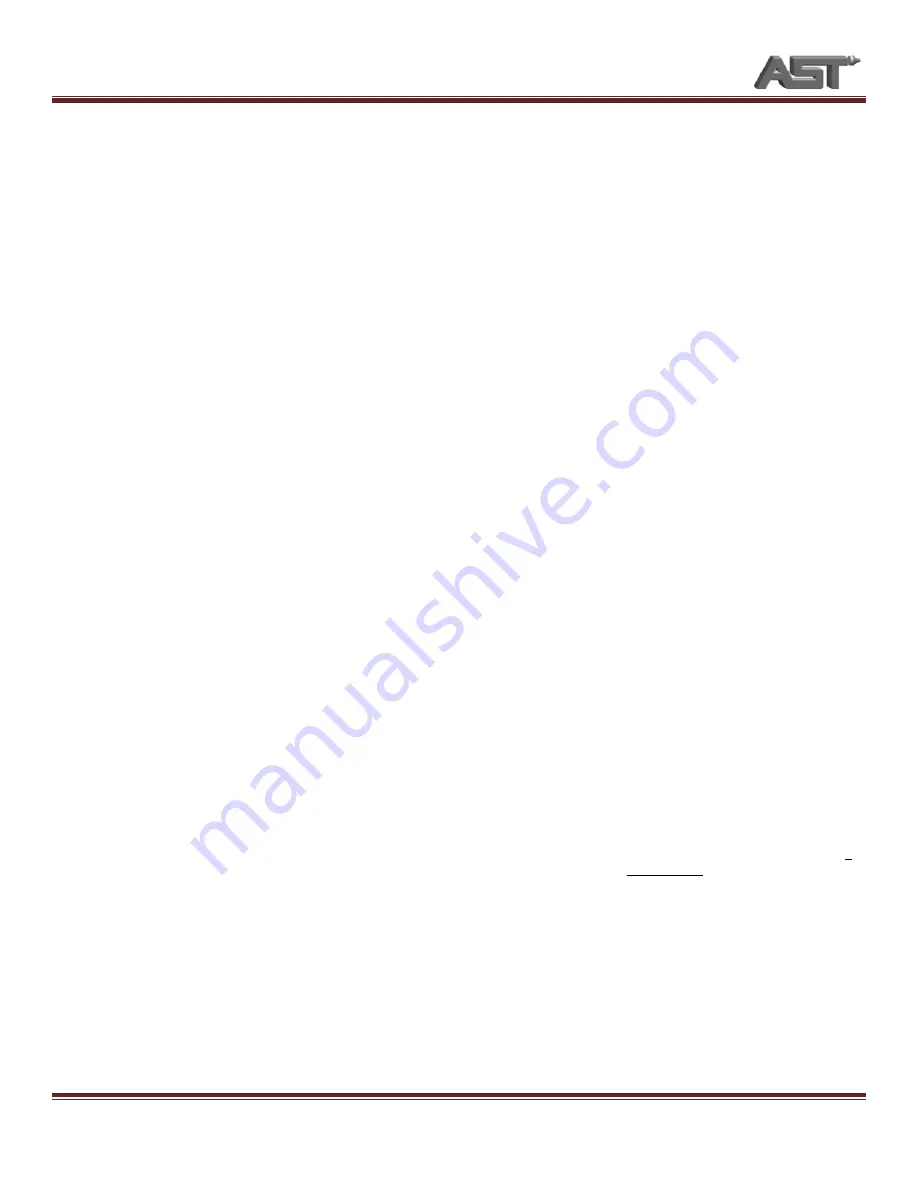
SHUT-DOWN PROCEDURES
60089-05
Page 11
o
Tank/Material Feed System
Clean & inspect tank lid sealing gaskets. Repair
with RTV Silicone as necessary.
Check make up air lines from desiccant canister to
tank. Remove or repair any blockages.
Clean inside of tanks, concentrating on any material
built up that might wind up in pumps.
Start-up Procedure
o
Prepare system for loading
Pre-season startup checks outlined below should be
performed in advance of any intended use.
AST assumes previous shut-down procedure was
followed.
Connect electrical power.
Test operation of machine. Verify that oil loaded
into machine comes out both ports on the
dispense valve when triggered.
Operate system until empty.
o
Flush system with compatible solvent
Fill each tank a minimum of 1/3 full with a
compatible cleaning solution.
Operate and observe behavior of system.
Verify that flow is coming out of both ports in
dispense valve.
Operate system until empty. Please not that it is not
harmful to run machine dry.
If possible, temporarily disconnect material hoses
from dispense valve and allow any trapped solvent
to drain.
Fill zerks on dispense valve with petrolatum grease
until lubricant coming out of ports is clean.
o
Load & Test Material
Load each material into correct tank. Remember to
keep one lid on while filling the other tank.
Set motor speed to low (30%) and actuate trigger,
operating system until correct material comes out
both ports of dispense valve.
Operate system until two streams of material come
out of dispense valve. Release trigger and wipe
manifold.
Attach static mixer to dispense valve. Make several
test shots of material in small cups or on aluminum
foil and allow curing.
Discard static mixer, wipe manifold clean, and re-fill
manifold with petrolatum grease.
Check cured material for flaws and inconsistencies.
See “Troubleshooting” section in operator’s manual
if any problems are observed.
END OF SEASON SHUTDOWN PROCEDURE
The following is the recommended procedure for storing
equipment for an extended period of time. Please note that
some items included in this procedure are not included with
all supplied equipment. Please use all safety devices such
as but not limited to gloves and eye protection. When
working with solvents do so in a well-ventilated area free of
combustible items. Take every effort not to mar or damage
any surfaces that come in contact with materials.
Pump Unit Dry
o
Pump remaining material.
Remove static mixer and/or spray attachment.
Operate machine until no material is being
dispensed. Check that hoses are allowed to drain
completely (hoses should lead “downhill” towards
dispense valve).
Clean dispense valve & reapply layer of petrolatum
grease.
o
Flush System
Use only a cleaning solution most effective for
removing your material. Consult material
manufacturer for recommendations. Carefully
observe all health and safety precautions listed on
all labeling.
Fill each tank a minimum of 1/3 with a compatible
cleaning solution.
Set pump speed control to slow setting.
Operate machine until cleaning solution begins
coming out of machine.
Allow machine to sit for a period of time, depending
on effectiveness of cleaning solution, not more than
one hour. Most solvents will not damage any
component unless allowed to remain in system.
Continue pumping cleaning solution into container
until machine is again empty. Observe cleaner as it
is being pumped. As solution is pumped, it should
appear to become clean. If this is not observed, the
same cleaner, after impurities have settled, can be
reloaded into machine and procedure repeated – if it
is pumped out immediately. Do not allow any
settled material back into system.
o
Tank/Material Feed System
Clean & inspect tank lid sealing gaskets. Repair
with RTV Silicone as necessary.
Clean inside of tanks, concentrating on any material
built up that might wind up in pumps.
o
Re-fill System for Storage
Fill tanks with compatible oil/lubricant and trigger.