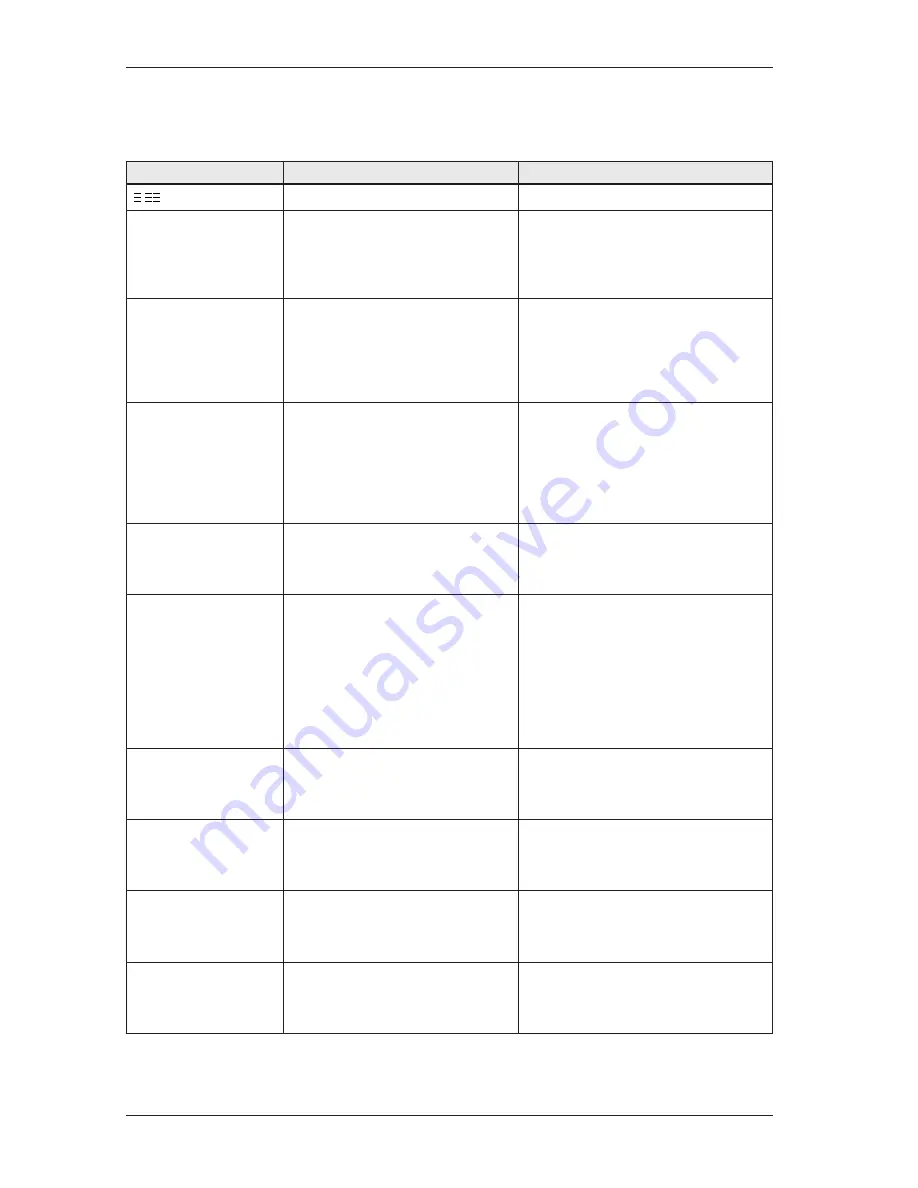
Service manual DW Outdoor
19
Display
Cause
Action
The door is open
Close the door
F:41
Temp stop fault
Temperature increase less than
5°C (41°F) in ten minutes. Program
continues with the process. Only
indicated in service menu.
Check
Element, thermistor, water level, circulation
pump, control unit and cables.
F:10
Overfi lling
Too much water in the machine
(pressure sensor) or fl oat activated. If
the water has not been emptied within
60 seconds, the program stops (drain
pump activated).
Check
Drain pump (blocked hose), fl ow meter,
inlet valve, leaks and cables.
F:42
Thermistor fault
Communication between the
thermistor and control unit has
stopped or the thermistor is reporting
temperatures greater than 80°C
(176°F). Program continues with the
process. Only indicated in service menu.
Check
Thermistor, plugs, wire harness, and control
unit.
F:12
Water inlet fault
< 80 pulses within 60 seconds or
correct number of pulses not achieved
within 255 seconds. Program stops.
Check
Water inlet, fl ow meter, inlet valve and
cables.
F:40
Inlet valve leakage
Water intake detected when inlet
valve deactivated in program sequence
or standby. In this case the machine
attempts to close the valve by opening
it for 2 seconds and then closing it
again. If water fl ow through the valve
is still detected any current program is
stopped (drain pump activated).
Check
Leak through inlet valve and fl ow meter.
F:43
Pressure sensor fault
Output signal > 4.8 V. The program
continues. Only indicated in service
menu.
Check
Pressure sensor, control unit and cables.
F:11
Water outlet fault
Water not drained after 120 seconds
draining. Program stops.
Check
Drain pump, hoses, drain hose fi ttings,
control unit and cables. Also check whether
fi lter is blocked.
F:44
Turbidity sensor fault
Only indicated in service menu. The
machine assumes high turbidity in case
of “uncertainty” in the auto program.
Check
Water quality, fi lters, turbidity sensor and
drain system.
F:45
Spray arm diverter fault
Position switch always closed or open.
The program continues. Only indicated
in service menu.
Check
Spray arm diverter (functioning gearbox,
switches and cables).
Troubleshooting
Fault and information codes
Audible signal sounds when a fault is indicated on the display.