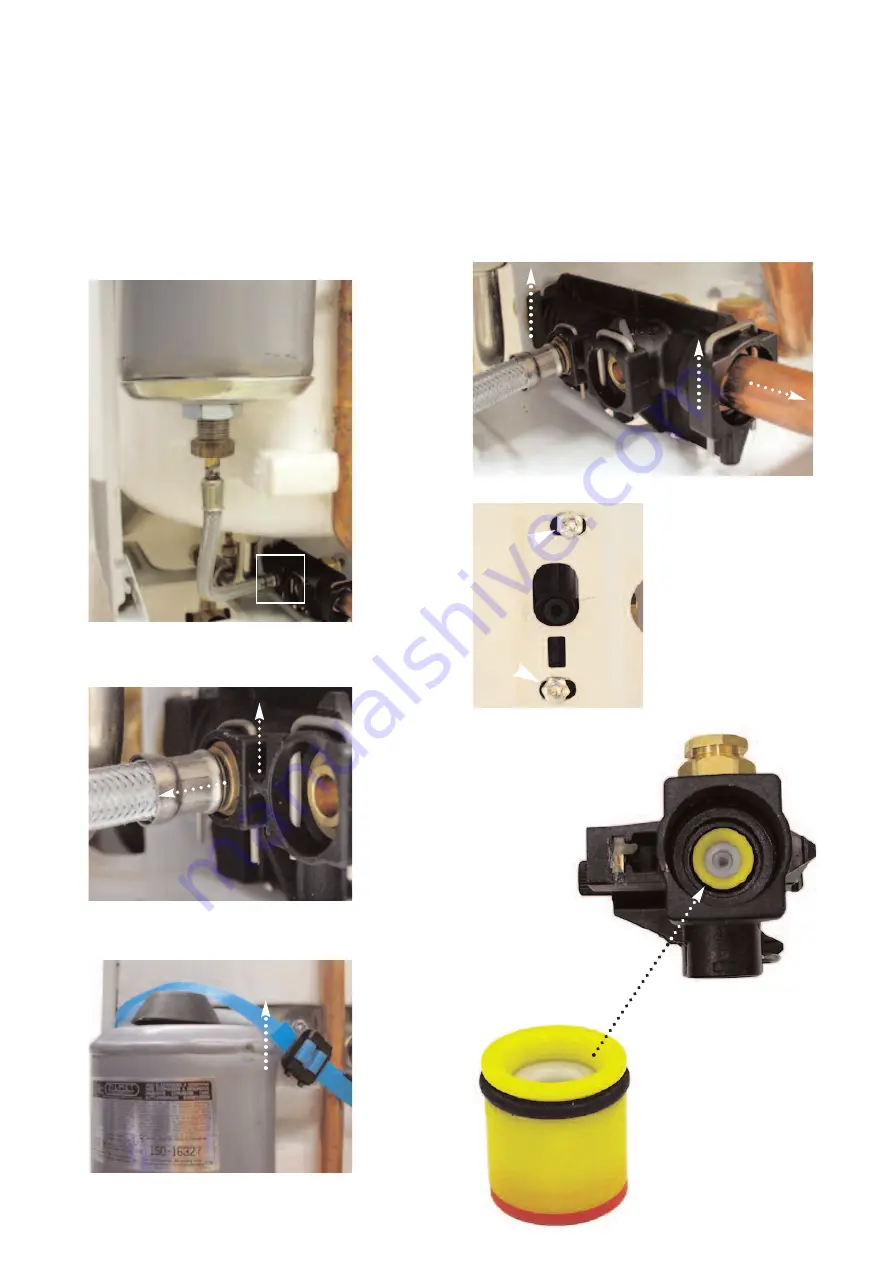
55
18.6.14 Removing the D.H.W. expansion vessel
1. Remove the casing as in step 18.2.1 ;
2. Remove the clip (see Fig. 18.79 & 18.80);
3. Pull up the first tie on the top of the expansion vessel (see
Fig. 18.81) ;
4. Pull up the expansion vessel to disengage it from the
second tie;
5. Reassemble in reverse order.
18.6.15 Removing the flow limiter
1. Carry out steps 18.2.1 and 18.2.2;
2. Remove the two clips and remove the pipe (see Fig. 18.82);
3. Remove the two screws (see Fig. 18.83) and pull the block
toward you;
4. Remove the limiter from the block (see Fig.18.84);
5. Reassemble in reverse order.
Fig. 18.79
Fig. 18.81
Fig. 18.80
Fig. 18.82
Fig. 18.84
Fig. 18.83
Fig. 18.85
Summary of Contents for GENUS 30 Plus
Page 30: ...30 Airpressure Swi tch Ear th Ear th 13 Electrical System Diagrams FIG 12 4...
Page 62: ...62...
Page 63: ...63...