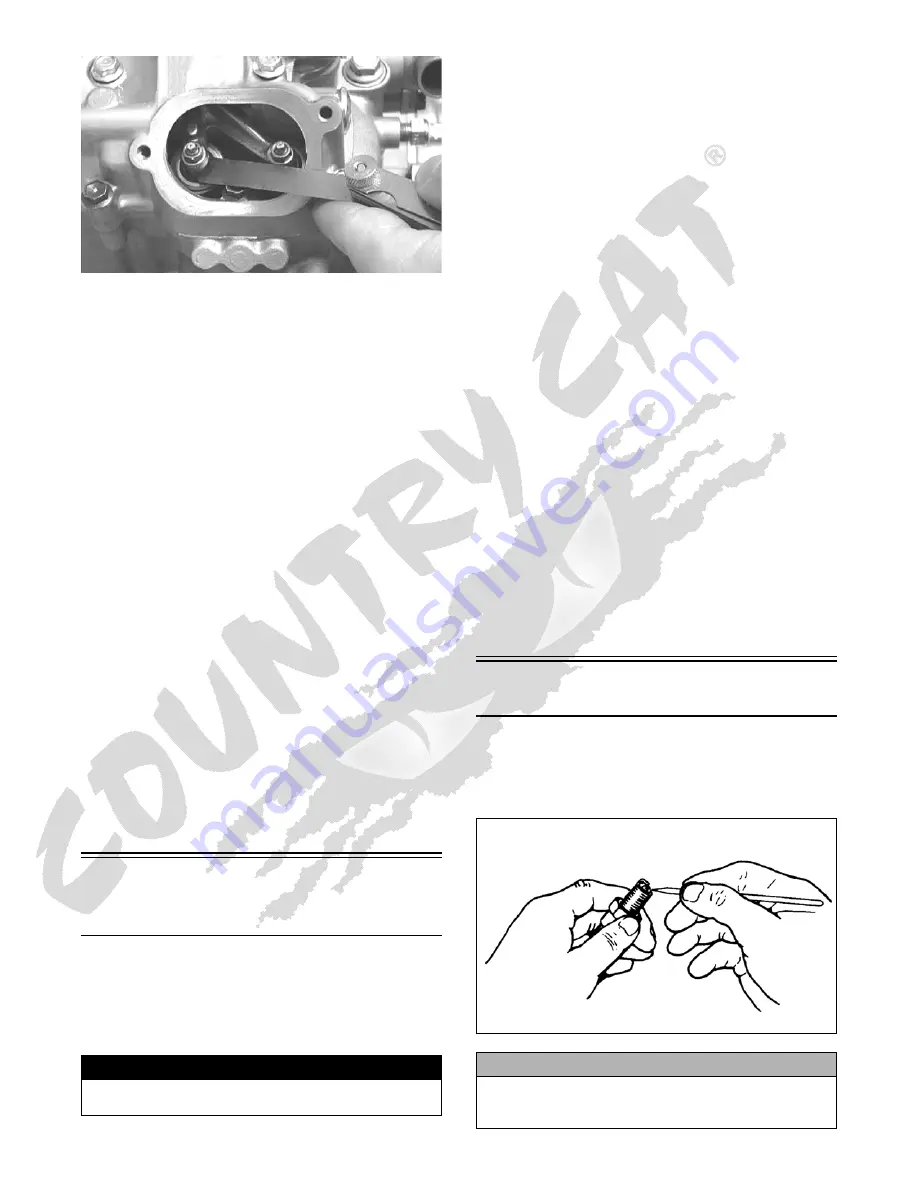
10
CC007DC
Valve Adjuster Procedure
A. Place the Valve Clearance Adjuster onto the jam
nut securing the tappet adjuster screw; then rotate
the valve adjuster dial clockwise until the end is
seated in the tappet adjuster screw.
B. While holding the valve adjuster dial in place, use
the valve adjuster handle and loosen the jam nut;
then rotate the tappet adjuster screw clockwise
until friction is felt.
C. Align the valve adjuster handle with one of the
marks on the valve adjuster dial.
D. While holding the valve adjuster handle in place,
rotate the valve adjuster dial counterclockwise
until proper valve/tappet clearance is attained.
NOTE: Refer to the appropriate specifications in
Feeler Gauge Procedure sub-section for the proper
valve/tappet clearance.
NOTE: Rotating the valve adjuster dial counter-
clockwise will open the valve/tappet clearance by
0.05 mm (0.002 in.) per mark.
E. While holding the adjuster dial at the proper
clearance setting, tighten the jam nut securely
with the valve adjuster handle.
3. Place the two valve inspection covers with O-rings
into position; then tighten the covers securely.
4. Install the spark plug; then install the timing inspec-
tion plug.
Testing Engine
Compression
To test engine compression, use the following procedure.
1. Remove the high tension lead from the spark plug.
2. Using compressed air, blow any debris from around
the spark plug.
3. Remove the spark plug; then attach the high tension
lead to the plug and ground the plug on the cylinder
head well away from the spark plug hole.
4. Attach the Compression Tester Kit.
NOTE: The engine must be warm and the battery
must be fully charged for this test.
5. While holding the throttle lever in the full-open posi-
tion, crank the engine over with the electric starter
until the gauge shows a peak reading of 95-115 psi
(five to 10 compression strokes).
6. If compression is abnormally low, inspect the
following items.
A. Verify starter cranks engine over at normal speed
(approximately 400 RPM).
B. Gauge functioning properly.
C. Throttle lever in the full-open position.
D. Valve/tappet clearance correct.
E. Valve not bent or burned.
F. Valve seat not burned.
NOTE: To service valves, see Engine/Transmission -
Servicing Top-Side Components.
7. Pour approximately 30 ml (1 fl oz) of oil into the
spark plug hole, reattach the gauge, and retest com-
pression.
8. If compression is now evident, service the piston
rings (see Engine/Transmission - Servicing Top Side
Components).
Spark Plug
A light brown insulator indicates that a plug is correct. A
white or dark insulator indicates that the engine may need
to be serviced. To maintain a hot, strong spark, keep the
plug free of carbon.
ATV-0051
! WARNING
Always wear safety glasses when using compressed
air.
CAUTION
Before removing a spark plug, be sure to clean the area
around the spark plug. Dirt could enter engine when
removing or installing the spark plug.