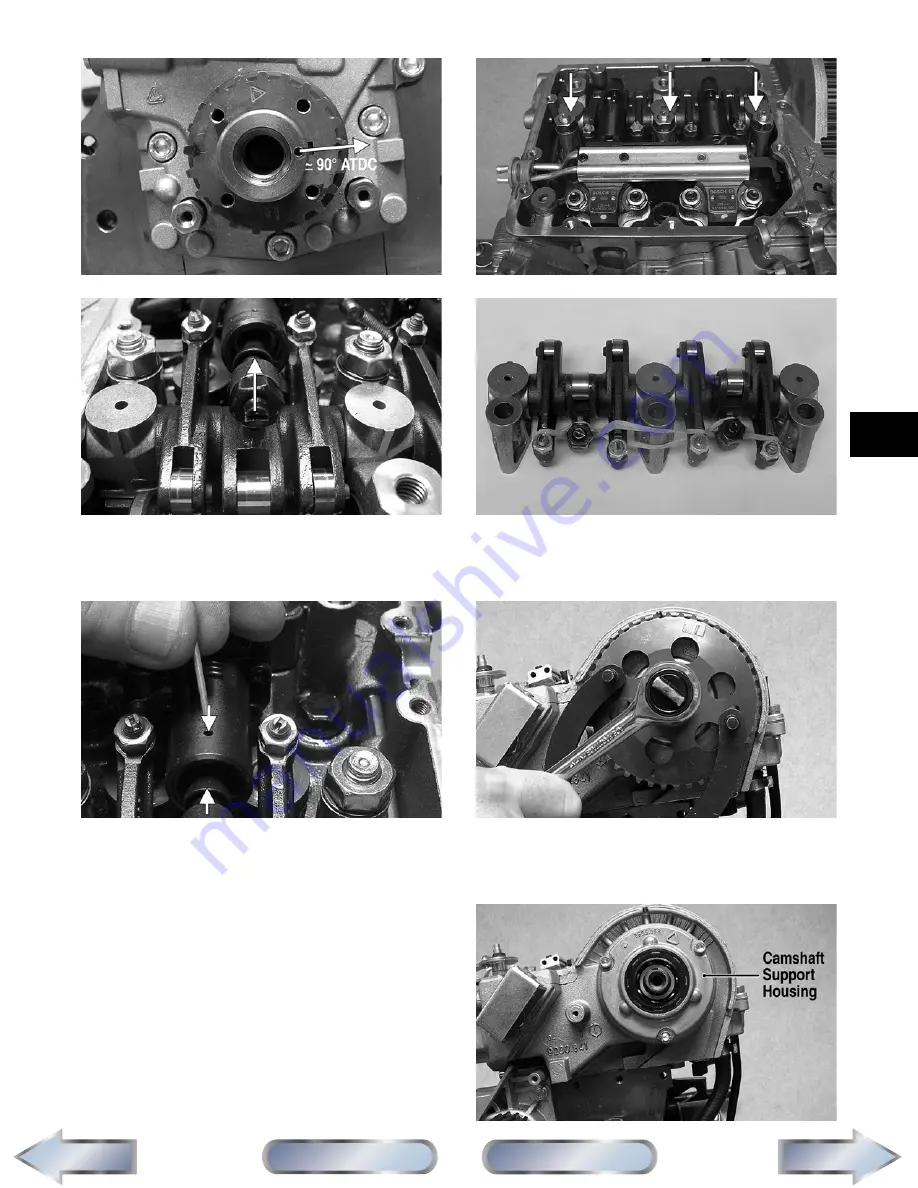
3-15
3
DE275A
DE404A
9. Place a holding pin into the injector pump barrel;
then rotate the camshaft until the second injector is
fully compressed and install a holding pin.
DE328A
10. Remove the three nuts securing the rocker arm
assembly to the cylinder head; then using rubber
bands, bind the rocker arms together and lift the
assembly off the mounting studs being careful to
keep the injector push rods with the injector it was
originally installed in.
DE260C
DE529
11. Using an appropriate holding tool, remove the cap
screw securing the camshaft drive pulley to the
camshaft; then remove the pulley.
DE276
12. Remove the camshaft support housing; then
remove the speed governor flyweight assembly.
Account for an O-ring.
DE245A
Next
Back
Section
Table of Contents
Manual
Table of Contents
FOR ARCTIC CAT ATV DISCOUNT PARTS CALL 606-678-9623 OR 606-561-4983
www.mymowerparts.com