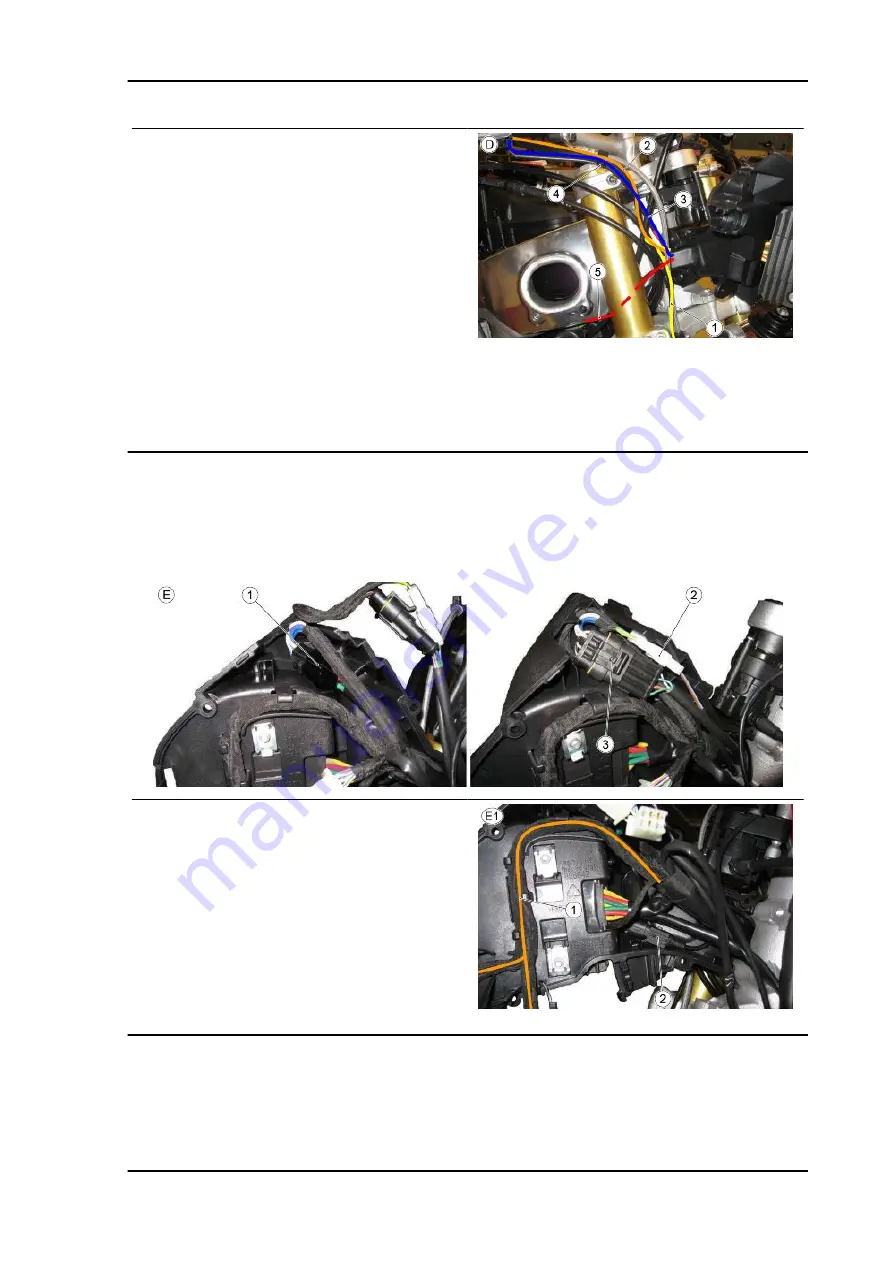
TABLE D
1. Speed sensor cable harness routing inside the
cable grommet and between throttle cables and
frame
•
Ensure that the cable grommet is not
interfering with the steering damper
during its movement
2. Right switch cable harness routing
3. Rubber clamp
4. Front stop switch cable harness routing
5. Main cable harness routing
TABLE E - INSTRUMENT HOLDER SUPPORT
•
First connect the regulator connector (1) and place it as shown in the figure
•
Connect the stop connector (2) and then the right light switch connector (3) and place them
as shown in the figure.
TABLE E1 - INSTRUMENT HOLDER SUPPORT
•
Place the branch (1) in the correspond-
ing tongues as shown in the figure
•
Fit the front ABS sensor (2) as shown
in the figure
•
Place the clamps (3) to then fasten the
main cable harness.
TUONO V4 R
Electrical system
ELE SYS - 101
Summary of Contents for TUONO V4 R 2010
Page 1: ...SERVICE STATION MANUAL B043120 TUONO V4 R ...
Page 4: ......
Page 6: ...INDEX OF TOPICS CHARACTERISTICS CHAR ...
Page 51: ...INDEX OF TOPICS SPECIAL TOOLS S TOOLS ...
Page 59: ...INDEX OF TOPICS MAINTENANCE MAIN ...
Page 81: ...INDEX OF TOPICS TROUBLESHOOTING TROUBL ...
Page 90: ...INDEX OF TOPICS ELECTRICAL SYSTEM ELE SYS ...
Page 107: ...TABLE C2 DEMAND SENSOR 1 Demand sensor TUONO V4 R Electrical system ELE SYS 107 ...
Page 217: ...INDEX OF TOPICS ENGINE FROM VEHICLE ENG VE ...
Page 237: ...INDEX OF TOPICS ENGINE ENG ...
Page 341: ... Turn the engine with the heads facing upward Tighten the screw 24 TUONO V4 R Engine ENG 341 ...
Page 351: ...INDEX OF TOPICS POWER SUPPLY P SUPP ...
Page 361: ...INDEX OF TOPICS SUSPENSIONS SUSP ...
Page 397: ...INDEX OF TOPICS CHASSIS CHAS ...
Page 419: ...INDEX OF TOPICS BRAKING SYSTEM BRAK SYS ...
Page 431: ...INDEX OF TOPICS COOLING SYSTEM COOL SYS ...
Page 442: ...INDEX OF TOPICS BODYWORK BODYW ...