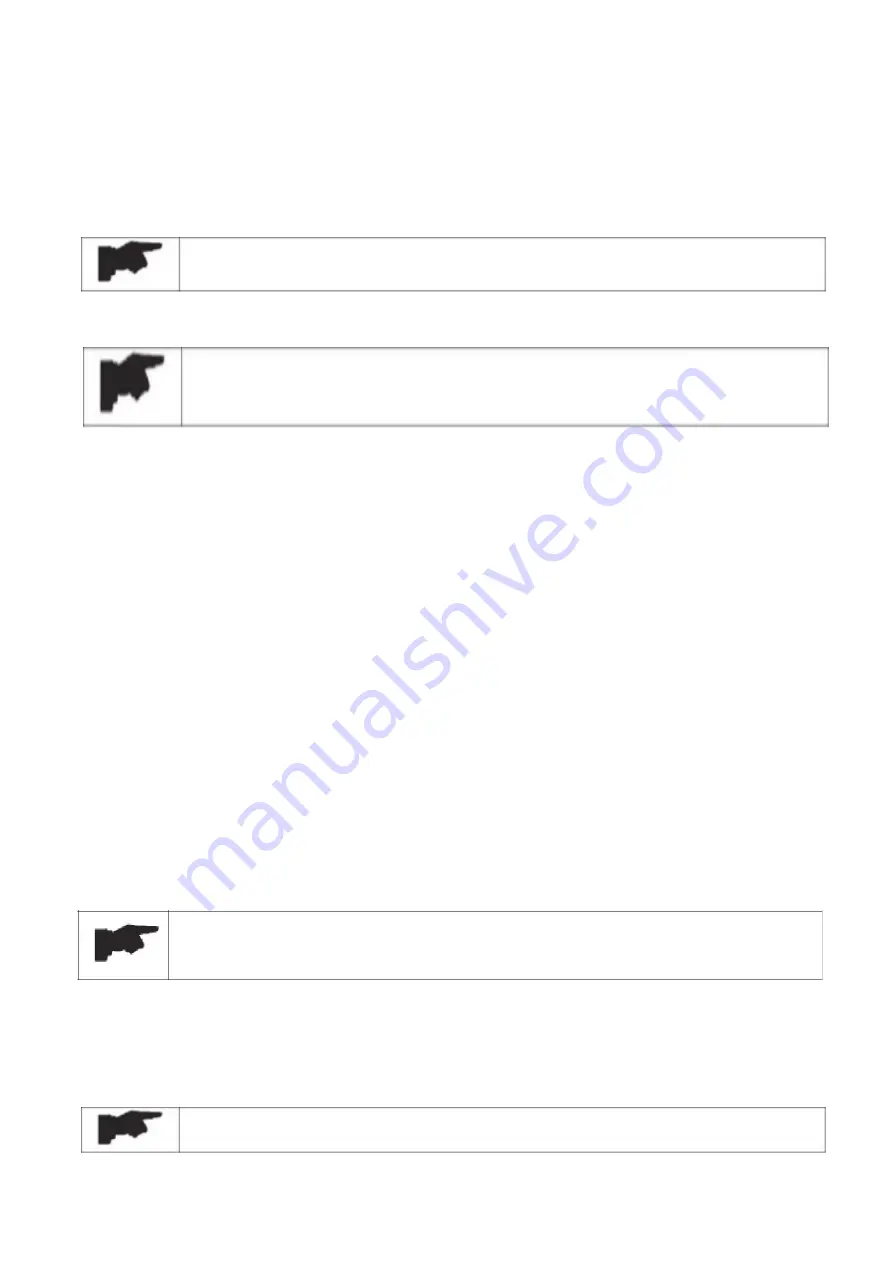
20
Remove the oil level plug on the oil tank and pour oil in the tank about 10 liters.
Raising the lift slowly by pressing the lifting button until the lift reaches the full height.
DO NOTcontinue pressing the button after lift reaches full height.
Damage to motor can occur if continued.
Repeat raise and lower the lift completely at least 3 times to bleed the trapped air inside the
cylinder.
If the oil level plug is lost or broken, order the replacement. The oil tank must be
vented well.
7.12 CHECK BEFORE START-UP
During START UP procedure, observe all operating components and check for
proper installation and adjustment. DO NOT attempt to raise vehicle until a
thorough operation check has been completed.
7.12.1 GENERAL CHECKS
Make sure to check that the columns are plumb;
Make sure to check the lift anchored to the ground and all anchor bolts tightened.
Make sure to check the electrical system feeding voltage is equal to that specified in the nameplate
on the motor;
Make sure to check the electric system connection in conformity of the electric plan shown as the
electric diagram (fig. 6) and for proper grounding.
Make sure to check all plastic sliders are on the position and greased properly.
Make sure to check all pins are installed correctly and greased properly.
Make sure to check all bolts, nuts and screws are tightened securely.
Particularly, below checks must be followed:
7.12.2 MECHANICAL SAFETIES FOR PROPER INSTALLATION
Check to make sure that the safeties in four columns are engaging uniformly. If not, repeat the
adjustment procedure described in the chapter 7.7.
Check to make sure that both the back-up safety and the slack cable safety for proper operation.
Check to make sure that the safety release handle for proper operation.
7.12.3 STEEL CABLE FOR PROPER INSTALLATION
There will be some initial stretching of the cables in the beginning. It will be
necessary to re-adjust the cables a week after the first week, then three months
thereafter. Failure to do this will cause uneven lifting.
Check to make sure that all cables are routed correctly and are on the correct pulleys.
Raise the lift off all safety locks until the cables are supporting the lift and check that all cables
are adjusted in the same tension and the lift can be raised evenly. If not, repeat the adjustment
procedure described in the chapter 7.7.
If the oil level plug is lost or broken, order the replacement. The oil tank must be
vented well.