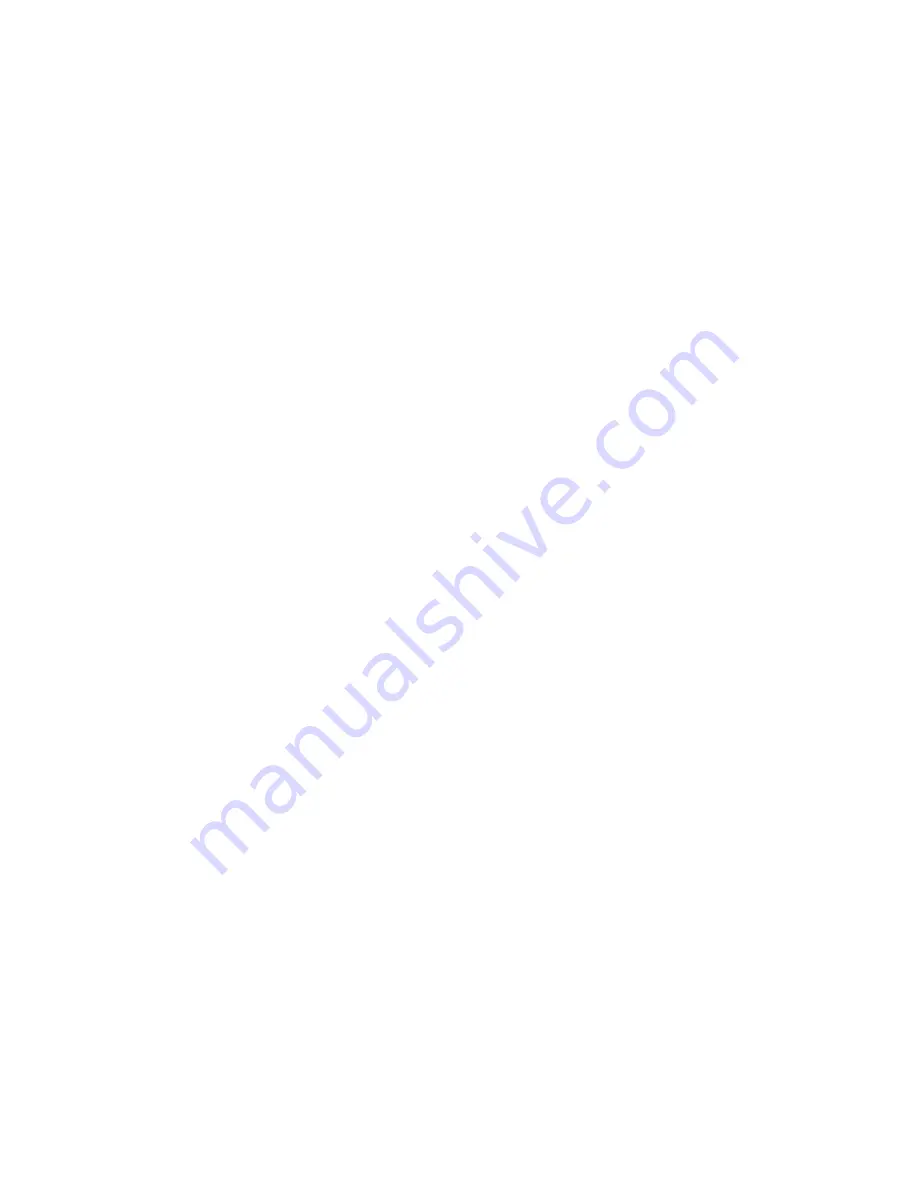
August 2012
L010796
10
Methods of Communication
There are two methods for sending commands to the DPE25611. One is to directly talk to the
DPE25611 by using Direct Talk Mode. This is usually used with a computer or PLC (Programmable
Logic Controller), where the computer or PLC gives the DPE25611 serial commands to off-load its
processor. For example: A PLC can utilize its outputs to toggle the DPE25611’s inputs and gain con-
trol of variable speeds, variable programs, variable distances, etc. Simply using the DPE25611 as
the intelligent pulse generator, a PLC can remove some of the tasks that were not meant for ladder
logic or any PLC processing time.
The second way to give commands to the DPE25611 is to use the software program SMC60WIN to
either manually control, or to write and send programs. This method is used when the DPE25611
is the main controller. For example: A DPE25611 can replace simple motion control and replace I/O
functional when minimal quantities of I/O are required to control specific machinery. Simple motion
profiles that can operate with 6 or less inputs and 8 or less outputs can utilize a DPE25611 controller.
Baud Rate
A term used frequently is serial data communications, a “baud” is defined as the reciprocal of the
shortest pulse duration in a data word signal, including start, stop, and parity bits. This is often taken
to mean the same as “bits per second”, a term that expresses only the number of “data” bits per
second. Very often, the parity bit is included as an information or data bit.
The DPE25611 accepts
a baud rate of 38400 only
.
Axis Selection
Each DPE25611 is addressed using a programmable register allowing the PC to address up to
DPE25611’s from one port. The Default axis is “0”. To change the axis, use the SMC60WIN software
or the “~” command. To verify or check the axis, use the SMC60WIN software or the “%” command.
The axis designation is nonvolatile and will remain the same until changed by the user.
Controller Status LED
When powered and operated properly, the status LED will be green. When an error occurs, the LED will
change to RED, and an error code will be generated in the error code register. To read and clear the
error with the software, click on the “Verify Parameters” button located in the “Motion Tab”. To read and
clear the error while in “Direct Mode”, use the error code “!” command. Once the error has been read and
cleared, the LED will return to green and the error code register will be cleared to 0. Refer to the table on
page 39 for a complete list of the error codes.
Technical Support
Everyone needs assistance on occasion. If you have problems using any of the equipment covered by
this manual, please read the manual to see if it will answer your questions. Be sure to look in the Trouble-
shooting Section located near the back of this manual. If you need assistance beyond what this manual
can provide, you may call the factory direct for application assistance. If possible, have this manual in
hand. It is often helpful to have the controller connected to a computer with the software installed.
Section 3: Controller Functions
July 2018