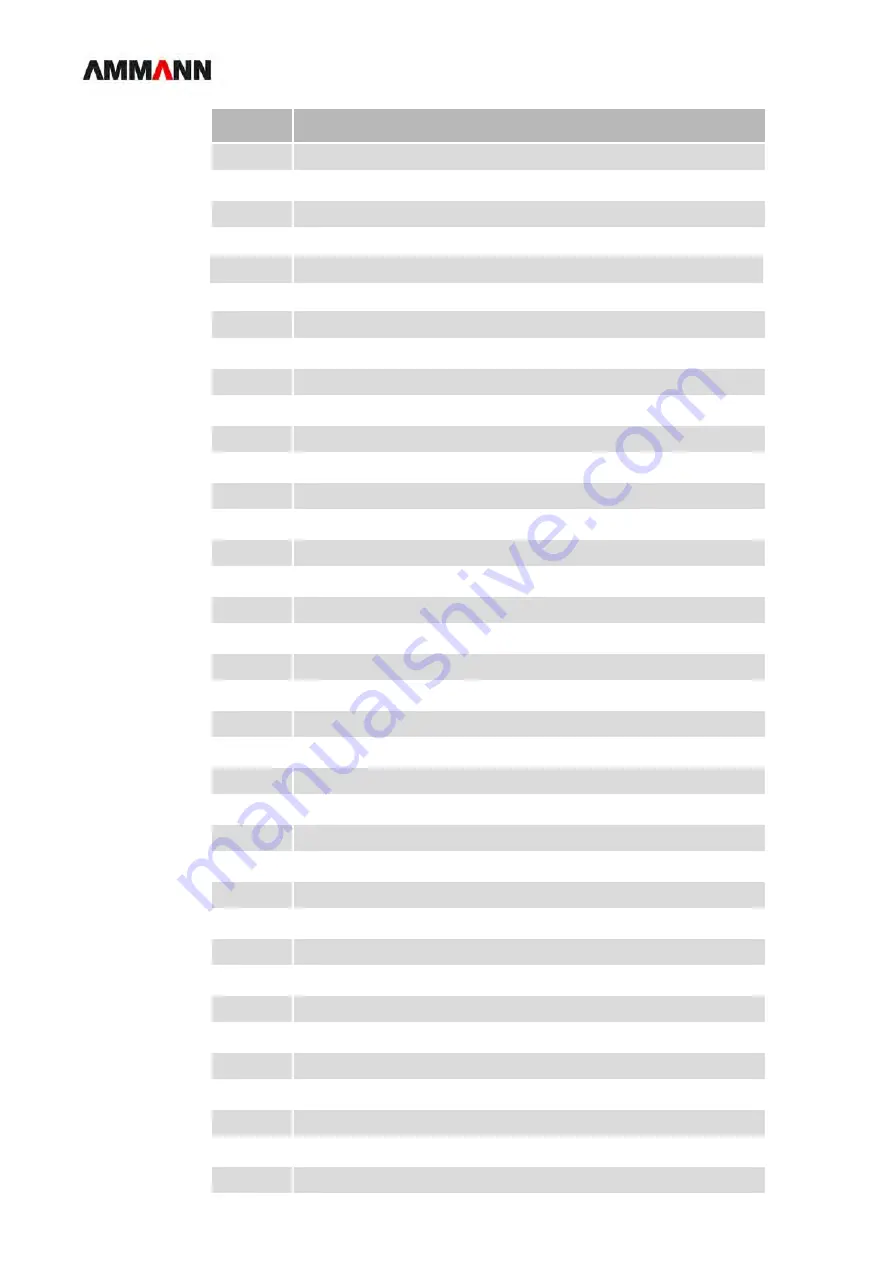
152
ARX 1
120
1281
A
|
24.
07.
2013
K14
Relay, light
K15
**
Relay, front vibration
K16
**
Relay, rear vibration
K17
Relay, brake-light
M1
Starter motor
M2
Hydraulic oil cooler
M3
Diesel pump
M4
Sprinkler pump
M11
Sprinkler pump, anti-adhesive
N1
Controller
N2
Display unit
N3
Measuring transducer, asphalt temperature
P1
Operating hours counter
R1
Pre-heating coil
R11
Seat heating
S1
Switch, ignition
S2
Switch, emergency stop
S3
Operating lever sensor, right
S4
Operating lever switch, right
S5
Potentiometer, sprinkler
S6
Switch, work gear
S7
Switch, vibration automation
S8
Switch, rear vibration
S9
Switch, horn
S10
Switch, parking light / dipped light
S11
Switch, revolving warning light, work light
S12
Switch, hazard flasher
S13
Switch, indicator
S14
**
Switch, vibration selector
S15
*
Operating lever sensor left
S16
*
Operating lever switch, left
S17
Switch, parking brake
S18
*
Battery cut-off switch
S19
*
Switch, flow divider
S20
*
Switch, edge cutter, up
Element
Description
K18
**
Relay, altitude solenoid power supply
K19 **
Control unit of altitude solenoid power supply
Summary of Contents for 6120529
Page 2: ......
Page 4: ......
Page 6: ...6 ARX 1 1201281 A 24 07 2013 ...
Page 12: ...12 ARX 1 1201281 A 24 07 2013 ...
Page 13: ...13 1201281 A 24 07 2013 1General ...
Page 18: ...18 ARX 1 1201281 A 24 07 2013 ...
Page 19: ...19 1201281 A 24 07 2013 2Product description ...
Page 26: ...26 ARX 1 1201281 A 24 07 2013 ...
Page 27: ...27 1201281 A 24 07 2013 3Safety information ...
Page 38: ...38 ARX 1 1201281 A 24 07 2013 ...
Page 39: ...39 1201281 A 24 07 2013 4Structure and function ...
Page 43: ...43 1201281 A 24 07 2013 5Operating and display elements ...
Page 52: ...52 ARX 1 1201281 A 24 07 2013 ...
Page 53: ...53 1201281 A 24 07 2013 6Commissioning ...
Page 55: ...55 1201281 A 24 07 2013 7Operation ...
Page 69: ...69 1201281 A 24 07 2013 8Options ...
Page 85: ...85 1201281 A 24 07 2013 9Maintenance ...
Page 124: ...122 ARX 1 1201281 A 24 07 2013 ...
Page 125: ...123 1201281 A 24 07 2013 10Repair ...
Page 134: ...132 ARX 1 1201281 A 24 07 2013 ...
Page 135: ...133 1201281 A 24 07 2013 11Storage ...
Page 138: ...136 ARX 1 1201281 A 24 07 2013 ...
Page 139: ...137 1201281 A 24 07 2013 12Transport ...
Page 144: ...142 ARX 1 1201281 A 24 07 2013 Fig 12 6 Roller s center of gravity ...
Page 145: ...143 1201281 A 24 07 2013 13Disposal ...
Page 148: ...146 ARX 1 1201281 A 24 07 2013 ...
Page 149: ...147 1201281 A 24 07 2013 14Appendix ...
Page 162: ...160 ARX 1 1201281 A 24 07 2013 ...
Page 165: ......