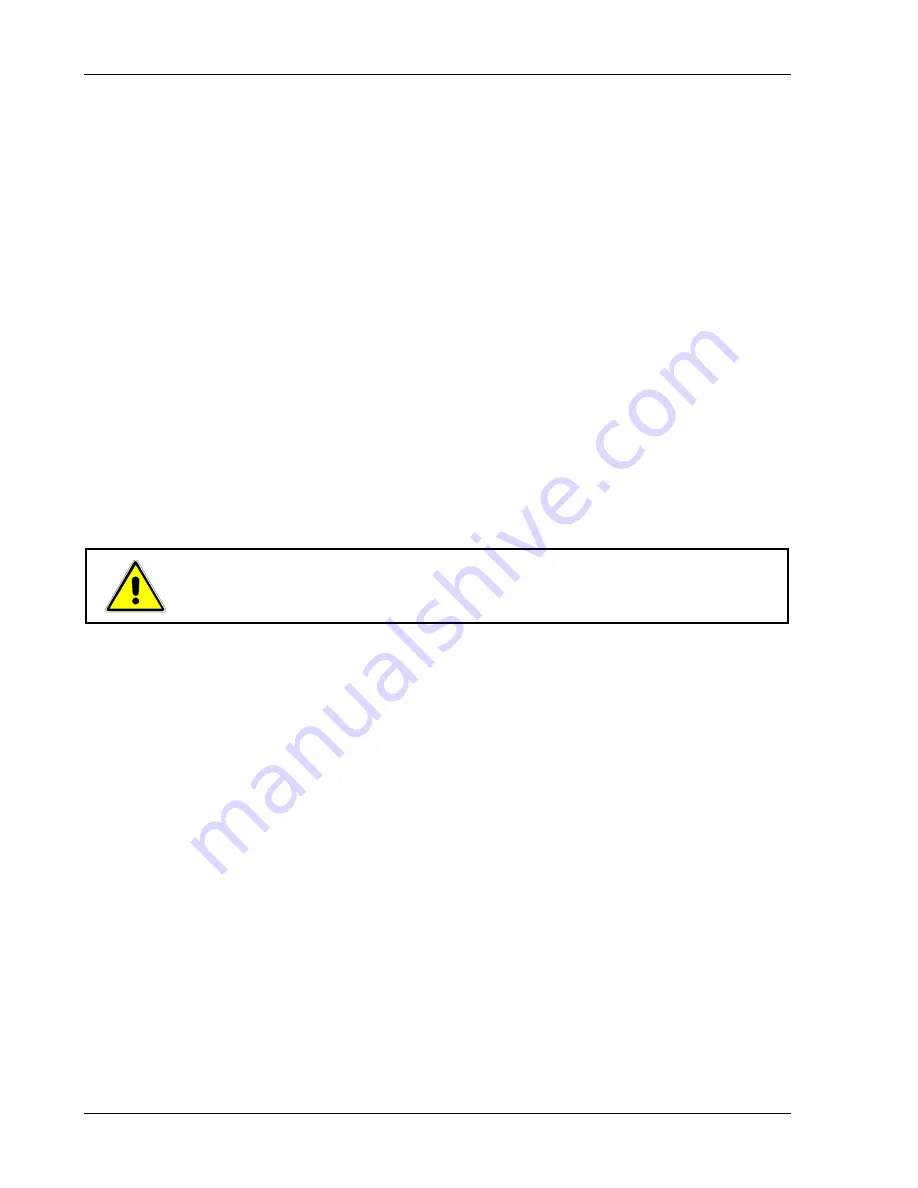
Basic Operation
DLM-E 3kW & 4kW Series Power Supplies
6. Adjust the voltage control to the required voltage (this will be the maximum compliance
voltage for applications using current mode operation).
7. Adjust the current control to the required current limit setting.
8. Release
the
V&I PREVIEW
button.
9. Press
the
ENABLE/STANDBY
switch to the
ENABLE
position to apply power to the
load.
10. The output Voltmeter and Ammeter will now display the actual values being supplied to
the load.
3.3
Using Remote Sensing
Remote sensing is used during voltage mode operation to shift the power supply's regulation
point from its output terminals (default sense point) to the load or distribution terminals by using
a separate pair of wires to monitor the load voltage. Remote sensing allows the power supply to
compensate for voltage losses in the load lines which would otherwise degrade the regulation of
the supply. The sense line connection points are located on the rear panel J11 connector.
Section 4.2 Configuring for Remote Programming, Sensing, and Monitoring
has more
information about making J3 connector changes.
CAUTION!
Do not use remote sensing with multiple supplies connected in series
or in parallel.
3.3.1
Connecting Remote Sense Lines
The DLM–E Series units are shipped with the rear panel J11 Sense connector jumpered for
local sensing of the output voltage. With local sensing, the output voltage is regulated at
the output. This method does not compensate for voltage losses in the load lines, so it is
recommended only for low current applications or applications for which load regulation is
not essential.
To connect remote sense lines, refer to Figure 3–3 and to the following procedure:
1. Ensure the power supply is turned OFF. Allow several minutes to elapse to dissipate
stored energy before altering J11 connector pin connections.
2. Remove the local sense jumpers connecting J11 pin 1 (positive sense) and pin 3
(negative sense or return sense) to the local bus bar or connector.
3. Connect the positive sense lead from the load to J11 pin 1 and the negative lead to
J11 pin 3. Use shielded–twisted pair wiring of 22 AWG or larger for sense lines.
4. Ground the sense line shield, at one point only, to the power supply's return output
connection at the load, or, to the power supply's return output at its output terminal, or to
the power supply's chassis.
3-4
M362000-01 Rev E
Summary of Contents for Sorensen DLM-E
Page 2: ......
Page 3: ......
Page 4: ......
Page 6: ...viii M362000 01 Rev E This page intentionally left blank...
Page 8: ...x M362000 01 Rev E This page intentionally left blank...
Page 10: ...xii M362000 01 Rev E This page intentionally left blank...
Page 12: ...xiv M362000 01 Rev E This page intentionally left blank...
Page 18: ......