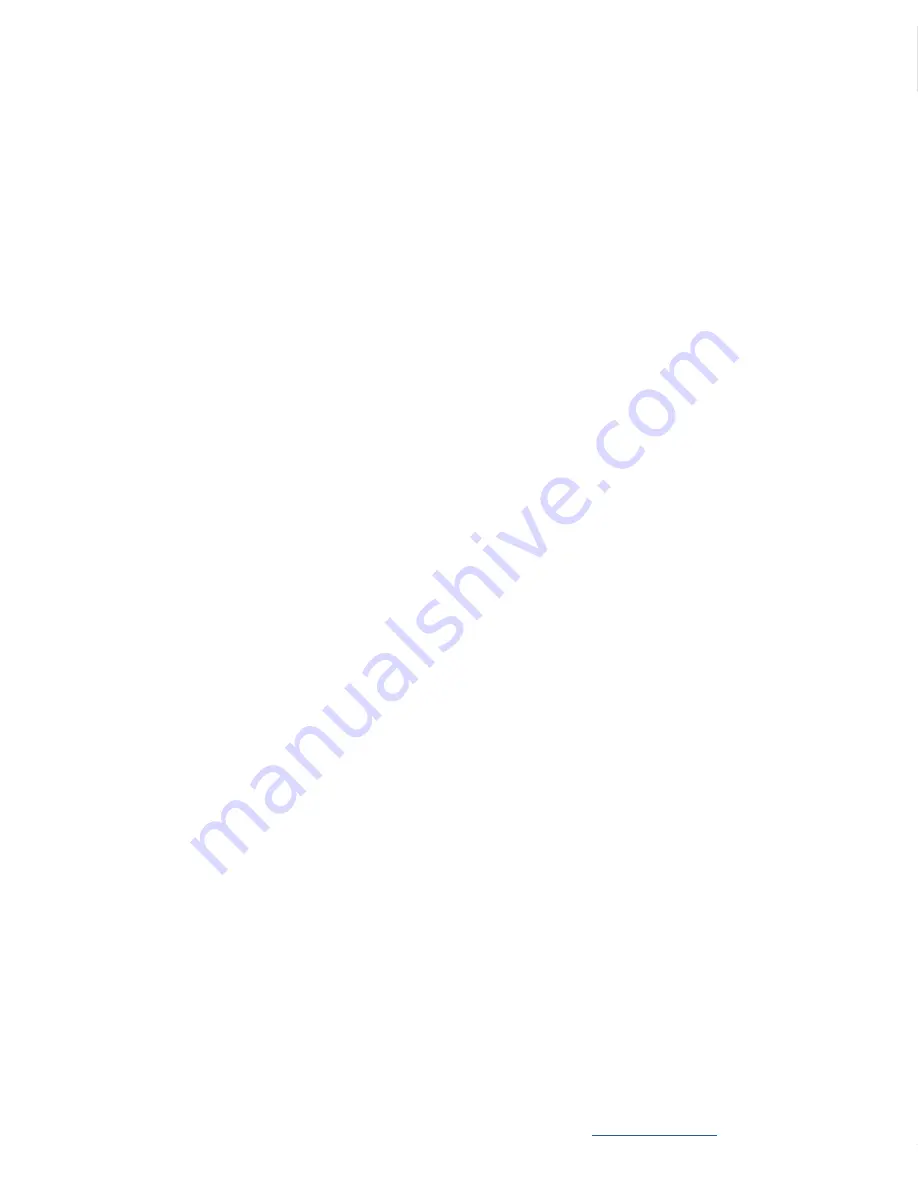
To obtain a PDF of this manual, visit our Products page at
.
Copyright Notice © 2021 AMETEK Process Instruments. All rights reserved.
The information and descriptions in this document are the sole property of AMETEK Process Instruments and may not be copied, reproduced, disseminated, or
distributed without explicit written permission from AMETEK Process Instruments.
The statements, configurations, technical data, and recommendations in this document are believed to be accurate and reliable at the time of this publication,
but AMETEK Process Instruments assumes no responsibility or liability for any errors or inaccuracies that may appear in this document.
AMETEK Process Instruments is not responsible for any infringement of patents or other rights of third parties that may result from the use of this document. The
content of this document is furnished for informational purposes only, is subject to change without notice, and does not represent a commitment or guaranty by
AMETEK Process Instruments.
AMETEK Process Instruments makes no warranty, express or implied, with respect to the content of this document. AMETEK Process Instruments shall not be
liable for any loss or damage, including consequential or special damages, resulting from any use of this information, even if loss or damage is caused by AMETEK
Process Instruments as a result of negligence or any other fault.
Summary of Contents for AMEVision
Page 78: ...PN 9000 165 VE Rev P WDG V AMEVision Modbus Map A 2 Thermox AMEVision Display User Interface ...
Page 79: ...PN 9000 165 VE Rev P EventMask 1 Bit definitions AMEVision Modbus Information A 3 ...
Page 80: ...PN 9000 165 VE Rev P WDG 5 Command Definitions A 4 Thermox AMEVision Display User Interface ...
Page 81: ...PN 9000 165 VE Rev P Status Mask Bit definitions AMEVision Modbus Information A 5 ...
Page 83: ...PN 9000 165 VE Rev P EventMask 2 Bit definitions AMEVision Modbus Information A 7 ...