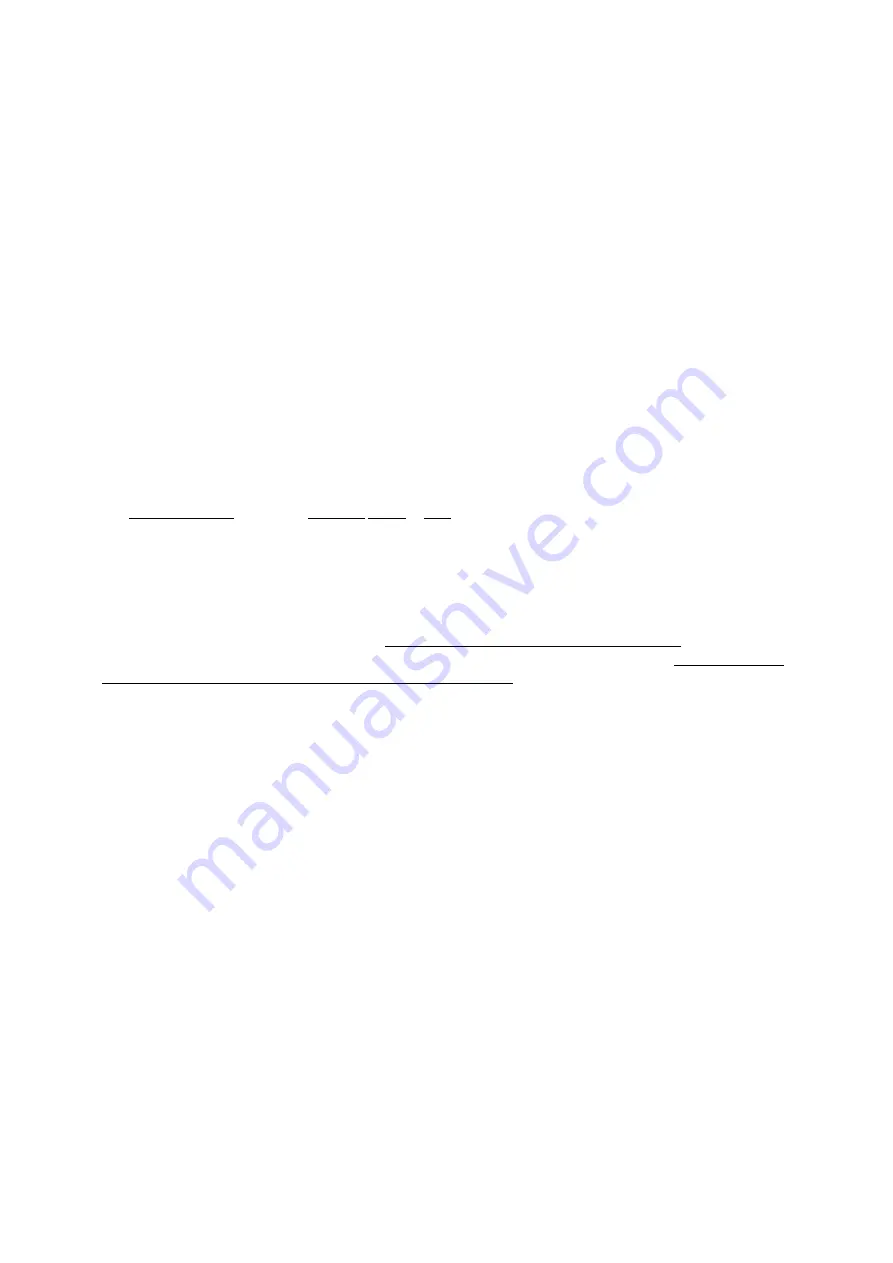
Ambic Equipment Ltd - AutoFoamer Operating Notes
-3 -
AF7500 (01.01.15)
Introduction
The AutoFoamer is designed to be installed using twin distribution tubes of 4mm bore (1/4” outside diameter) –
the BLACK tube supplies compressed air; the GREY /BLUE tube supplies pressurised teat disinfectant chemical –
both at a low pressure 3 - 5 psi (0.2 - 0.4 Bar) – see Fig 1. Chemical and air are supplied to the foaming
applicators, which generate foam in the cup whilst the trigger is held depressed.
WARNING
– Use only the GREY/BLUE tube for the CHEMICAL – the Black tube may be attacked by some
chemicals.
Safety
The AutoFoamer Foam Teat Dipping System is designed exclusively for use in milking installations. Any
application outside the use described in this operating manual will be taken to be not in accordance with the
intended purpose. The manufacturer/supplier will not be held responsible for any losses arising as a result of
such use. The user will take full responsibility for use. USE IN ACCORDANCE WITH THE INTENDED PURPOSE ALSO
INCLUDES COMPLYING WITH THE OPERATING MANUAL AND THE CONDITIONS FOR INSPECTION AND
MAINTENANCE.
Installation
(refer to Fig.1 & 1B, or 1C)
Electrical Installation -
should ideally be carried out by a Qualified Electrician – EXCEPT where a suitable
waterproof plug outlet is available. THIS ELECTRICAL SUPPLY SHOULD BE PROTECTED BY AN APPROPRIATE
EARTH LEAKAGE CIRCUIT BREAKER. IT IS RECOMMENDED THAT THE ELECTRICAL SUPPLY SHOULD BE SWITCHED
OFF AUTOMATICALLY WHEN THE VACUUM PUMP IS NOT IN OPERATION.
Pressurised Chemical
– is sucked up from a chemical container by peristaltic pump(s). The enclosure housing
the pump(s) of the AutoFoamer is rated at IP40 (IEC 60529), the power unit (A) must therefore be positioned
outside of the milking parlour in a dry location and close to a 220 –240V AC power socket (Power consumed:
1 pump = 120W ; 2 pumps = 240W). The 3-core power supply cord MUST remain accessible when the unit has
been installed and MUST be connected to Earth.
The large enclosure (
A1
) should be positioned no more than 2 metres vertically above the floor and no more
than 3 metres distant from the chemical container(s). For efficient and reliable operation the maximum vertical
distance from pump to distribution line should be less than 1 metre. Use the drilling template (page 31) to mark
out screw positions and fix the enclosure to a suitable flat wall, using the screws and plastic plugs supplied.
NOTE:
Allow sufficient space to the Right of the enclosure for mounting the
Pressure Reservoir Bottle
(
W
),
which
MUST
be in an UPRIGHT position, using a single screw (see Fig. 1B or 1C).
The small enclosure
(
A2
)
housing the Pressure Switch
(connected to the large enclosure by 4 metres of
armoured cable) should be screwed to a flat vertical surface (e.g. Wall) some 1-4 metres distant from the large
enclosure but as close as possible to the highest point of the distribution tubing. Use Cable clips supplied to
secure cable, but DO NOT SHORTEN armoured cable.
The chemical container(s) (D)
should be placed securely on the floor and the Inlet Tube(s) (
C
) from the pump
enclosure connected to the Inlet nipple(s) of the peristaltic pump(s) – each PVC inlet tube should be warmed
before pushing over the peristaltic pump nipple and securing with the stainless steel hose clips supplied. Make
sure that clips are fitted so that the barb of the fitting on the pump is central in the clip and do NOT over tighten
the clip (you risk breaking the plastic nipple). Drop the filter end of the inlet tube(s) into the chemical
container(s).
Low Pressure Air
is supplied, via the Regulator (B), from a DRY compressed air supply of 2-6 Bar (30-90 psi),
using suitable connection fittings (not supplied). The enclosure containing the Regulator is sealed to IP55 and
may be situated in any convenient, easily accessible location. The Non-Return Valve (
V
) is installed in the outlet
line to protect the compressor in the event of any Non-Return Valve failure elsewhere in the system. During the
initial system setting up process, it may be necessary to adjust the pressure regulator setting to obtain ideal
operating conditions for efficient foam production.
continued . . .