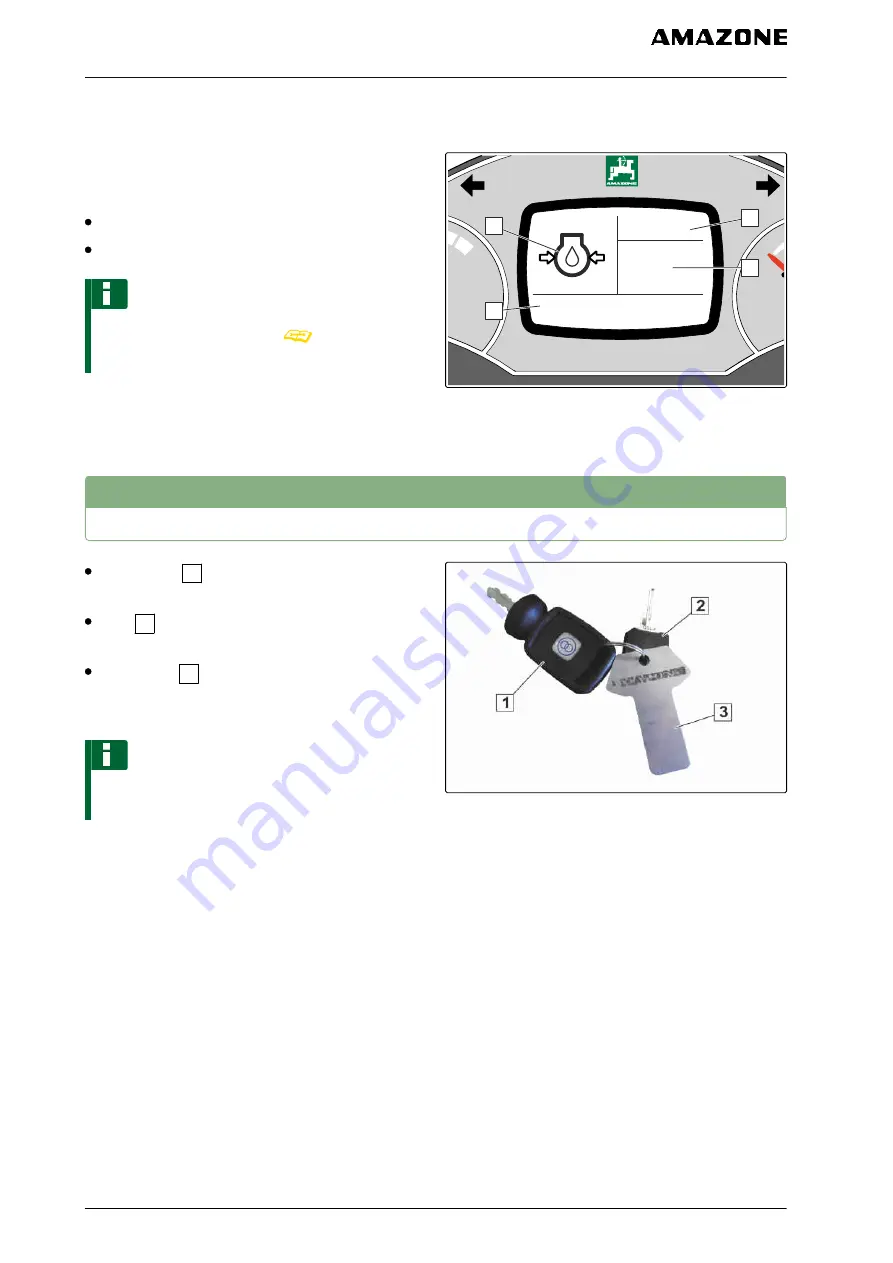
3.18.5.4 Maintenance mode
The information
"Perform maintenance"
appears at
the following intervals:
After the first 50 operating hours.
Every additional 250 operating hours.
NOTE
In addition, the control lamp
lights up on the
dashboard.
After finishing maintenance work, the maintenance
interval can be reset.
Engine oil pressure
1850,0 h
Error
6273
1
3
4
2
CMS-I-00002428
3.19
Key
Ignition key
1
, to start and switch off the
machine.
Key
2
, to open the seat carrier and the toolbox
beside the driver's seat.
Special key
3
, to open the protective lid on the
belt drive guard and the side cover in front of the
radiator.
NOTE
Lost keys can be reordered from AMAZONE by
indicating the vehicle ID no.
CMS-I-00002360
CMS-T-00002756-B.1
CMS-T-00002618-B.1
3 | Product description
Key
MG6399-EN-II | D.1 | 11.03.2020
48
Summary of Contents for Profihopper 1500 SmartLine
Page 153: ......