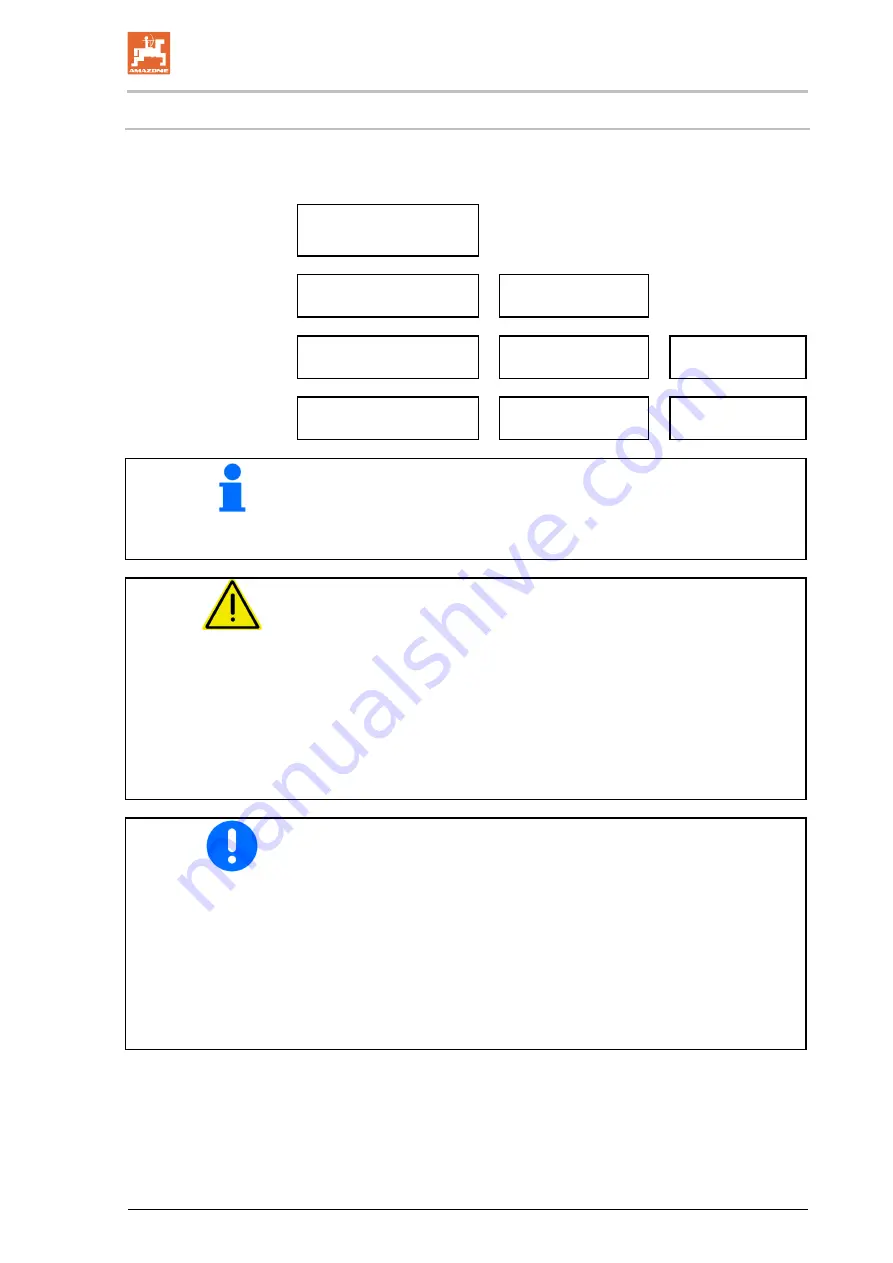
Commissioning
Cenius03-2TX BAG0112.13 07.21
71
6.1.1.7 Table
Actual value according to
calculation
Approved value ac-
cording to tractor
instruction manual
Double approved
load capacity (two
tyres)
Minimum ballast
front/rear
/
kg
--
--
Total weight
kg
≤
kg
--
Front axle load
kg
≤
kg
≤
kg
Rear axle load
kg
≤
kg
≤
kg
•
You can find the approved values for the total tractor weight,
axle loads and load capacities in the tractor registration papers.
•
The actually calculated values must be less than or equal to
(
≤
) the permissible values!
WARNING
Crush, cut, entanglement, pulling in and impact hazards caused
by poor stability and insufficient steering and braking capacity
of the tractor.
It is forbidden to couple the machine to the tractor used as the basis
for calculation, if
•
One of the actual, calculated values is greater than the approved
value.
•
There is no front weight (if required) attached to the tractor for
the minimum front ballast (G
V min
).
•
Ballast your tractor with weights at the front or rear if the tractor
axle load is exceeded on only one axle.
•
Special cases:
ο
If you do not achieve the minimum ballast at the front
(G
V min
) from the weight of the front-mounted machine (G
V
),
you must use ballast weights in addition to the front-
mounted machine.
ο
If you do not achieve the minimum ballast at the rear
(G
H min
) from the weight of the rear-mounted machine (G
H
),
you must use ballast weights in addition to the rear-
mounted machine.