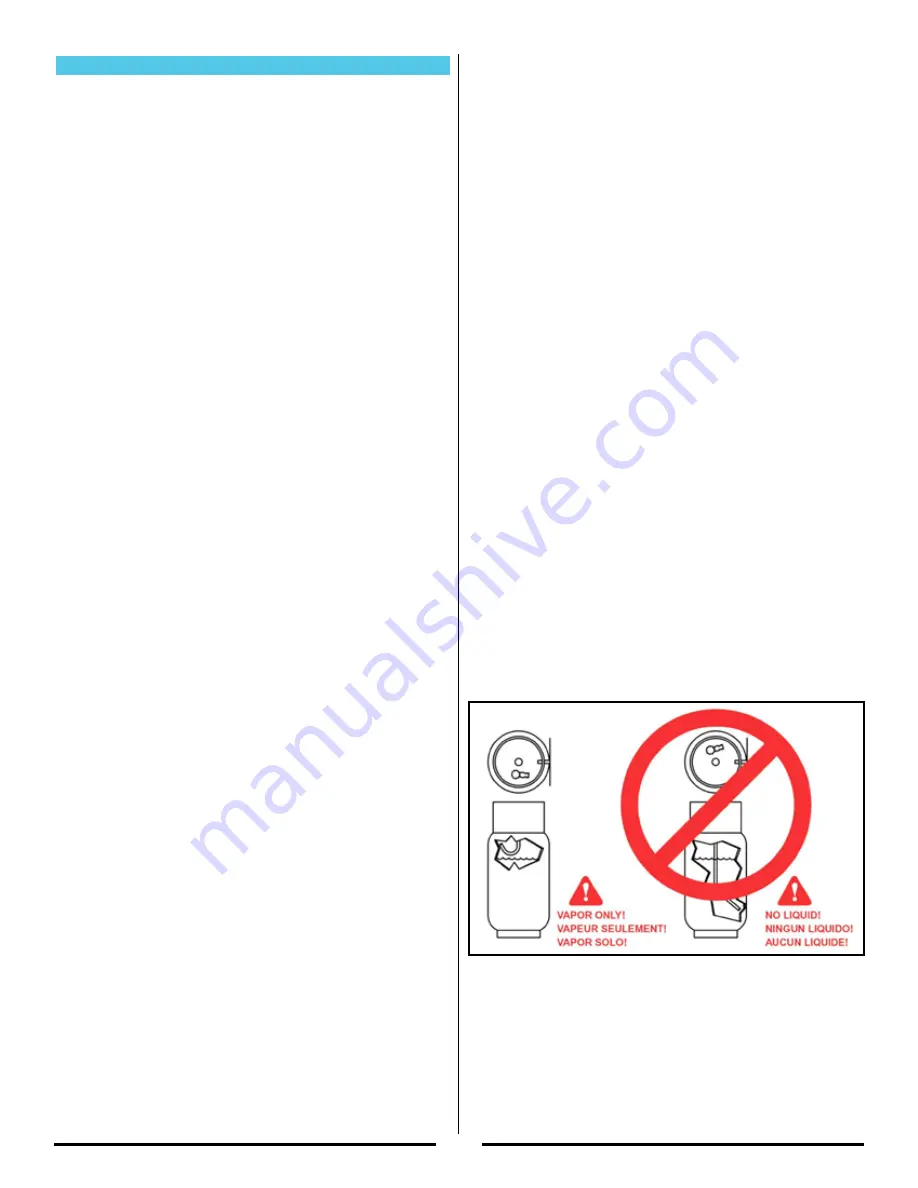
7
Safety Precautions
Anyone operating the machine should read the
following carefully and be informed of potentially
dangerous operating conditions. Operators should
be familiar with the location and use of all safety
devices on the machine. Do not use the machine
if it is not in proper operating condition, and report
any damage or operation faults immediately.
DANGER!
Operate this machine in a well-ventilated
area. It is the responsibility of the machine operator,
machine owner, and the site manager to ensure that the
air exchange system where the machine is to be used is
in compliance with local building codes and is operating
properly. Failure to operate this machine in a well-
ventilated area could lead to sickness, injury, or death
from carbon monoxide (CO) exposure.
DANGER!
This machine emits CO, which is colorless,
odorless, non-irritating gas. The first symptoms of CO
exposure include headache, drowsiness, dizziness,
and nausea. If you should experience any of these
symptoms while operating the machine, shut off the
machine and go outside to get fresh air. Have the
machine tested for CO emissions by a qualified service
technician before using it again.
DANGER!
Prolonged or high exposure to CO may
result in vomiting, confusion, and collapse in addition
to loss of consciousness and muscle weakness. If
such symptoms occur, call 911 for emergency medical
attention. If you have experienced these symptoms,
DO NOT
operate this machine or any other propane
machine again until cleared by a physician. Excessive
exposure to CO can result in death.
DANGER!
Propane is a highly flammable fuel. If you
smell propane, shut off the machine immediately and
take it outside the building.
DO NOT
use the machine
again until a qualified service technician has corrected
the propane leak.
DO NOT
use or allow another person
to use an ignition source such as a cigarette lighter
near the propane machine.
DO NOT
smoke near the
propane machine.
DO NOT
vent a propane cylinder
inside a building.
DO NOT
store propane cylinders
inside a building.
DANGER!
This machine has parts, including the pad
assemblies, that can cause severe injury if these parts
are contacted while they are moving.
DO NOT
allow
any part of the body or clothing to come in contact
with these parts while they are moving.
DO NOT
try
to change attachments while the machine is running.
DO NOT
allow other people to come near the machine
while it is in operation.
DO NOT
allow the machine to
run unattended.
DO NOT
leave the machine in a place
where unauthorized or untrained personnel could use
the machine.
DO NOT
run the machine with the pad off
center, damaged or missing.
DO NOT
run machine with
unsecured guards and shields.
DO NOT
operate the
machine if the machine has loose parts.
DANGER!
Federal law and California State law
prohibits the following acts or the causing thereof: (1)
the removal or rendering inoperative by any person
other than for purposes of maintenance, repair,
or replacement, of any device or element of design
incorporated into any new engine for the purpose
of emission control prior to its sale or delivery to the
ultimate purchaser or while it is in use, or (2) the use of
the engine after such device or element of design has
been removed or rendered inoperative by any person.
Among those acts presumed to constitute tampering are
the acts listed below:
DO NOT
tamper with the original
emission related part.
l
Throttle body and internal parts
l
Spark plugs
l
Magneto or electronic ignition system
l
Air cleaner elements
l
Crankcase
l
Cylinder heads
l
Breather chamber and internal parts
l
Intake pipe and tube
l
Regulator
l
Fuel lock-off
WARNING!
Overfilled or liquid withdraw cylinders can
damage the fuel system and create a fire hazard.
DO
NOT
overfill the cylinder or use a liquid withdraw
cylinder on the machine. If the regulator freezes stop
the burnisher and take the cylinder outside. Inspect
cylinder, if a vapor withdraw cylinder, use gloves or
pliers to open bleeder valve and purge cylinder until
only vapor is escaping. If it is a liquid withdraw cylinder,
replace with a vapor withdraw cylinder. Both cylinders
are shown below.
Summary of Contents for Pioneer Eclipse PE440ST
Page 1: ...Propane Stripping Machine PE440ST Operator s Manual...
Page 2: ......
Page 30: ...30 Electrical Schematic with SafeSense...
Page 31: ...31 Electrical Schematic with Optional SafeStop...
Page 32: ...32 Electrical Schematic without SafeSense...
Page 33: ...33...
Page 34: ...34 Connections with SafeSense...
Page 36: ...36 Connections with SafeStop...
Page 37: ...37 Connections with SafeStop continued...
Page 38: ...38 Connections without SafeSense...
Page 52: ...52 Transport Cart Assembly RF037800 052311 6 5 3 2 4 4 7 1...
Page 54: ......
Page 58: ......
Page 59: ......