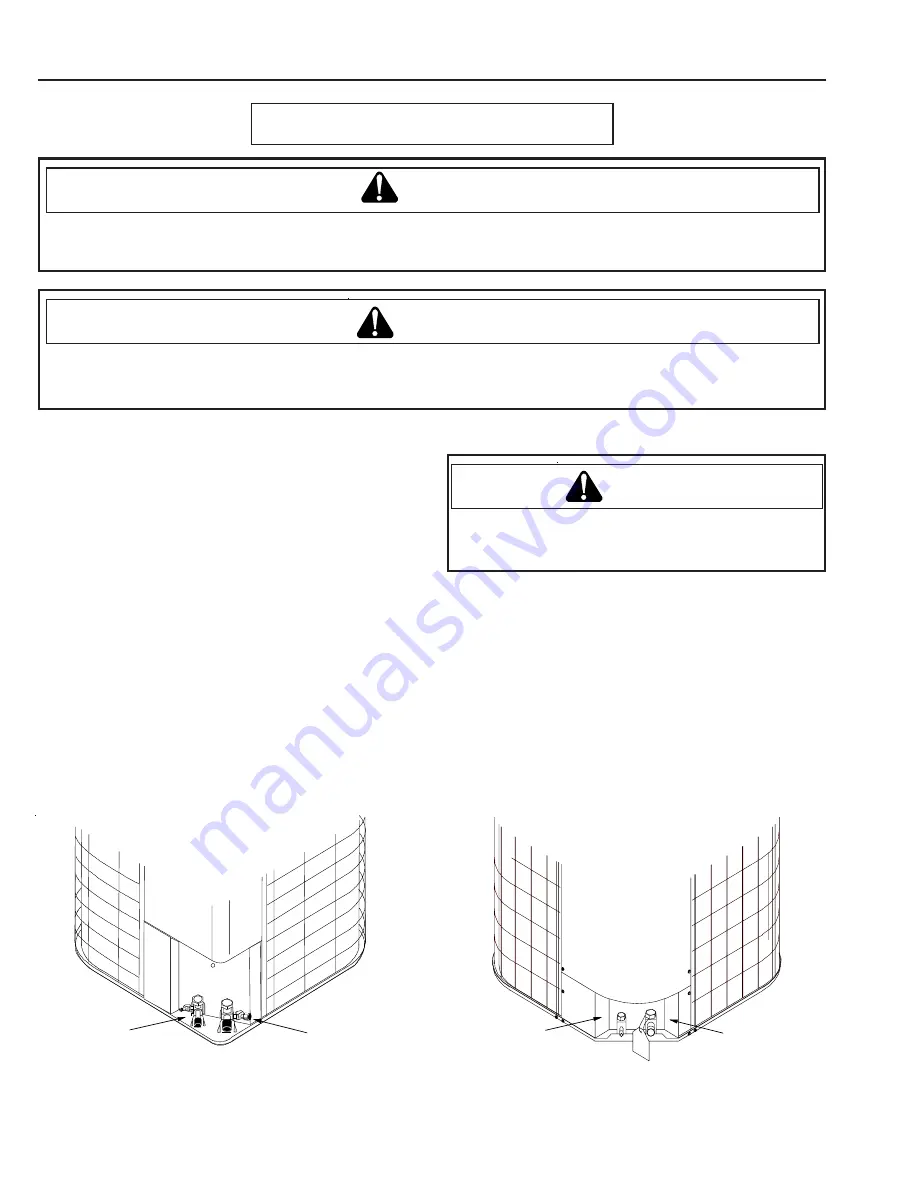
6
Leak Testing
WARNING
To avoid the risk of fire or explosion, never use oxygen, high pressure air or flammable gasses for leak testing of a
refrigeration system.
Safe Refrigerant Handling
WARNING
To avoid possible explosion, the line from the nitrogen cylinder must include a pressure regulator and a pressure
relief valve. The pressure relief valve must be set to open at no more than 150 psig.
1. Be sure both hand valves on the gauge manifold are
closed relative to the center port (i.e., turned in all
the way.) Attach this gauge manifold to the service
valves on the unit (see Figure 2). Do not open the
unit service valves. Do not use refrigerant from the
unit for leak testing - it has been precisely measured
at the factory for optimum performance.
2. Connect a cylinder of dry nitrogen to the center port
on the gauge manifold.
3. Open the hand valve a minimal amount on the line
coming from the nitrogen cylinder.
4. Open the high pressure valve on the gauge mani-
fold. Pressurize the refrigerant lines and the indoor
coil to 150 psig (1034 kPA). To reach 150 psig, you
may need to further open the hand valve on the ni-
trogen cylinder.
WARNING
To avoid possible explosion or equipment damage,
do not exceed 150 psig when pressure testing.
After you reach 150 psig, close the valve on the nitrogen
cylinder. Disconnect it from the gauge manifold. If you plan
to use an electronic leak detector, add a trace of R-22 to the
system (if permitted by current EPA regulations).
5. Place a chloride-free soap solution on all connections
and joints. If you see bubbles, you have a leak. Mark
these locations.
6. Use the gauge manifold to carefully release the nitro-
gen from the system. If leaks were found, repair them.
After repair, repeat the above pressure test. If no leaks
exist, proceed to system evacuation.
Figure 2
LIQUID LINE
SERVICE VALVE
VAPOR LINE
SERVICE VALVE
LIQUID LINE
SERVICE VALVE
VAPOR LINE
SERVICE VALVE