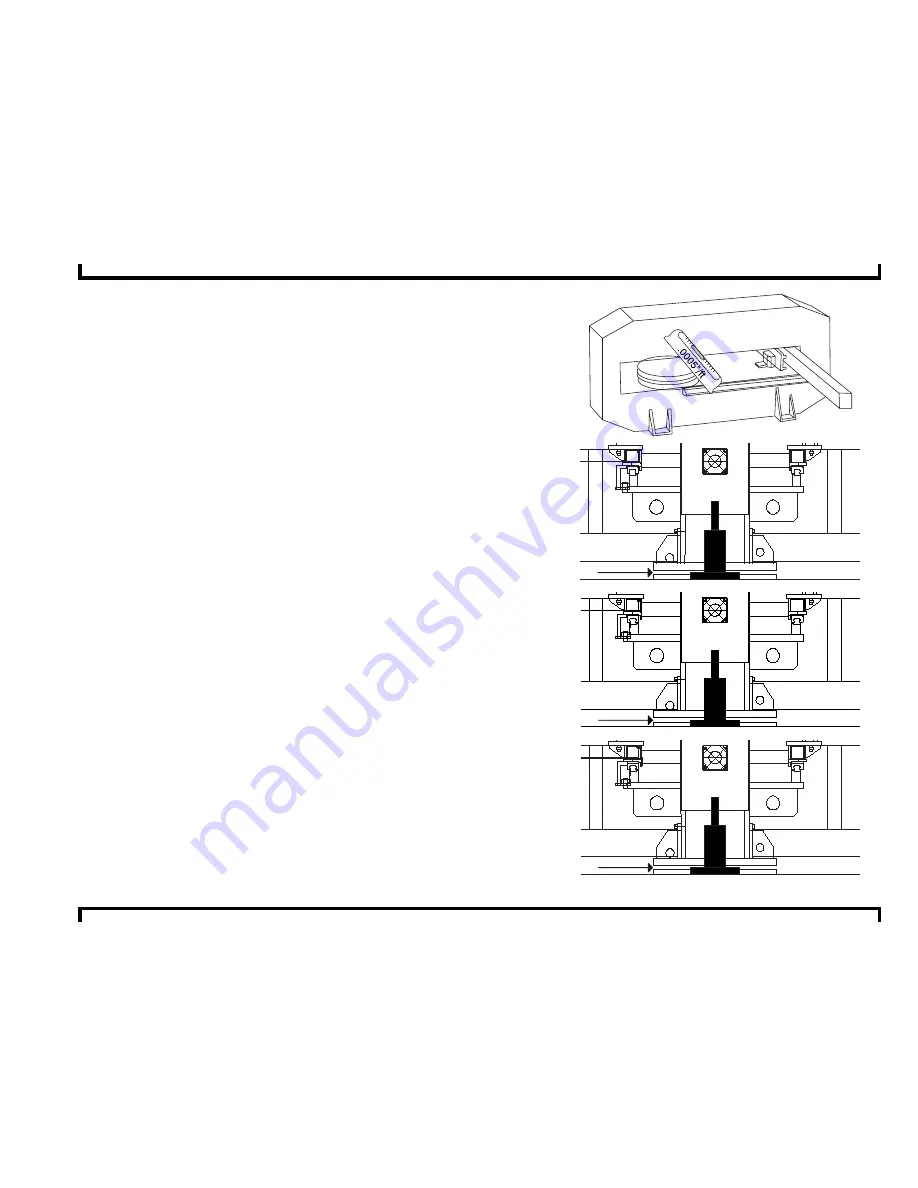
Pega 367 with Fanuc 04PC User Pre-installation Guide
©Amada America, Inc.
Print Date 03/07/2001 Revision 4.0
This document available on the World Wide Web at http://www.amada.com
Page 34 of 35
6.
With the machine supported on the bottle jack at the carriage end
of the machine frame and the machine feet at the turret end of the
machine frame, place the spirit level on the turret.
7.
Measure and record the level of the turret in the x-axis direction.
8.
Lower the machine frame to place all machine feet in contact with
the leveling shims and base plates.
9.
Lift the turret end of the machine frame to allow shimming
between the machine feet and base plates to level the machine
frame in the x-axis direction.
10. Repeat steps 5 to 9 until the machine frame measures level to
0.0005"/ft in step 7, then continue.
Shim to
level X-axis
Bottle
Jack
11. With the weight of the carriage end of the machine supported by
the bottle jack. Monitor the level of the turret in the x-axis, as the
bottle jack is slowly lowered to place the carriage end machine
feet in contact with the base plates.
12. Any change in the level indicates that the carriage end of the
machine needs to be leveled.
Remove weight
of machine from
base plates
Bottle
Jack
13. Lift the carriage end of the machine frame to allow shimming
between the machine feet and base plates to level the carriage
end of the machine frame in the x-axis direction.
14. Repeat steps 11 and 13 until no difference in level is noted when
the machine weight is on or off the base plates and shims, then
continue.
Shim to
level X-axis
Bottle
Jack