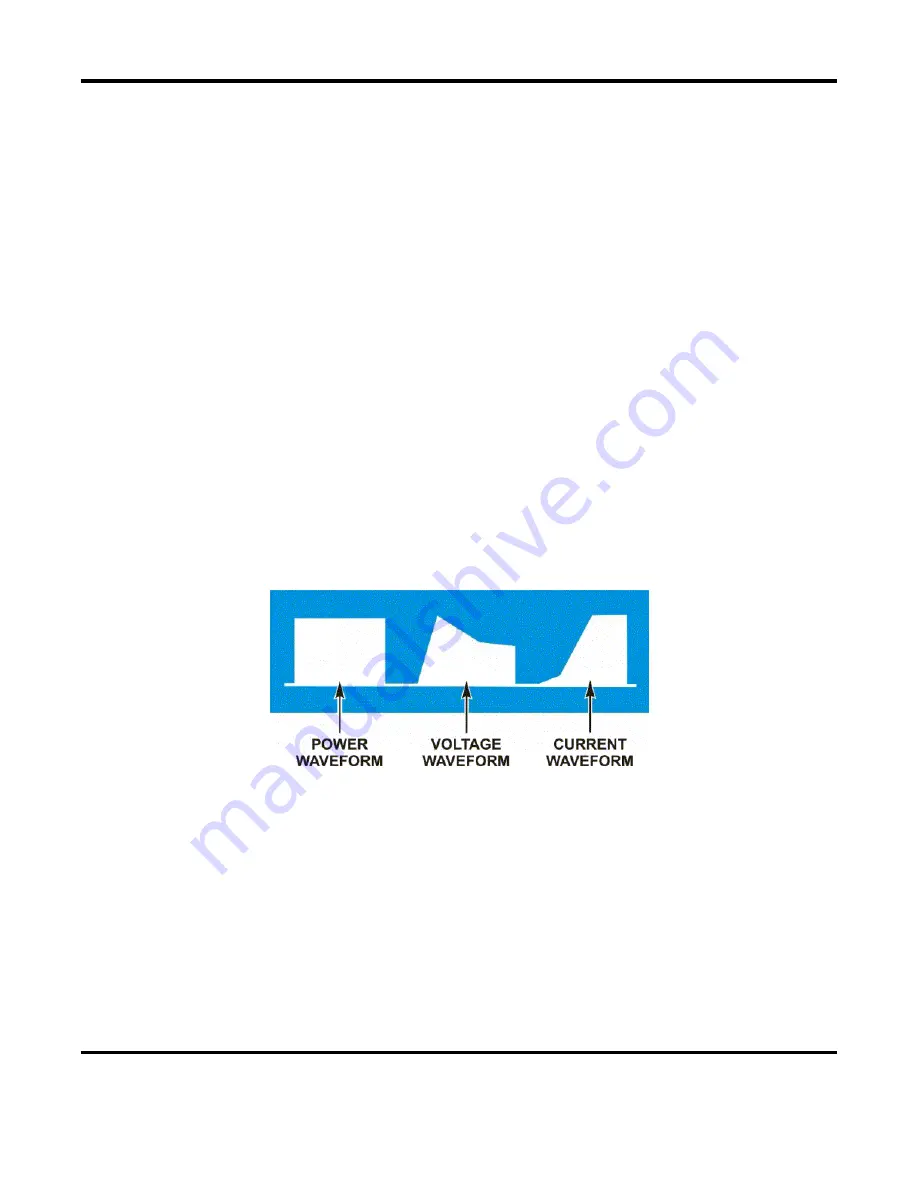
CHAPTER 4: INTRODUCTION TO FEEDBACK MODES AND MONITORING
HF28 DC RESISTANCE WELDING SYSTEM
990-372
4-5
If production parts are plated, there can also be a plating process variation over time resulting in
inconsistent welds. These minor material variations are a major cause of process instability, and it is
best welding practice to seek to minimize their effect.
Active Part Conditioner
is designed to cope with material contamination, variation and can be
programmed to apply the exact power to the parts required to displace oxide or contaminants. In
addition, the “Part Conditioner” pulse will terminate at a precise current flow preventing the sudden high
flow, which occurs when the oxide is displaced. This prevents weld splash and material expulsion,
which occurs as a result of an excessively fast heating rate. Part conditioning can help to reduce
variations in contact resistance from part to part caused by different fit up of parts. It will stabilize the
contact resistances before the main welding pulse, therefore reducing variation from weld to weld.
How It Works
Both
constant current
feedback and
constant voltage
feedback modes are limited in their ability to
deal with varying levels of part contamination and oxide. If
constant current
feedback were used, the
power supply would ramp the voltage to very high levels in order to achieve current flow through the
oxide. This rapid input of current is likely to cause splash, especially with round parts.
Constant
voltage
mode is not ideal for this purpose either, as the voltage will be restricted from reaching
sufficient levels to break down the oxide.
Constant power
is ideal for this purpose. As the power supply tries to achieve constant power to the
weld, it raises the voltage to high levels early in the output waveform, since current cannot flow due to
the oxide. As the high voltage breaks down the oxide layer, more current flows to the weld and the
voltage and resistance drop. It will achieve this in a controlled fashion to maintain constant power to the
weld.
Constant Power Waveform With Corresponding
Voltage and Current Waveforms
Active Part Conditioning
uses a dual-pulse output. The first pulse is programmed for
constant power
,
and the second for either
constant current,
constant voltage
, or
constant power
. (
Constant voltage
is
used if there is still a chance of weld splash). The purpose of a dual-pulse operation is to enable the first
pulse to target displacement of oxides and good fit up; the second pulse achieves the weld.
Summary of Contents for 1-288-01
Page 1: ...990 372 REV E DC RESISTANCE WELDING SYSTEM HF28 OPERATION MANUAL...
Page 10: ...HF28 DC RESISTANCE WELDING SYSTEM x 990 372...
Page 64: ......
Page 88: ......
Page 102: ......
Page 114: ......
Page 142: ......