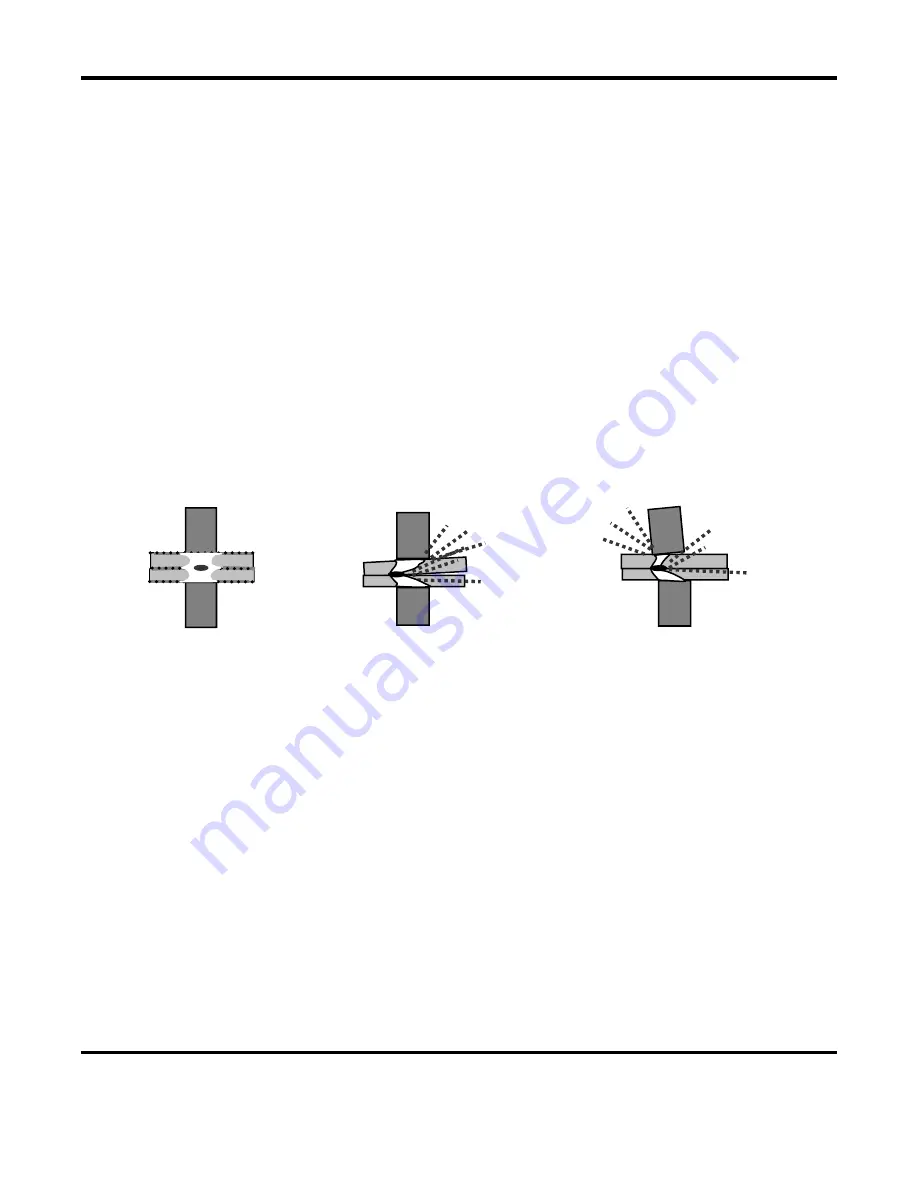
APPENDIX F: DEFINING THE OPTIMUM PROCESS
HF28 DC RESISTANCE WELDING SYSTEM
990-372
F-9
Process Perspective
What are the likely variables in a production process?
How will operators handle and align the parts?
What tooling or automation will be required?
How will operators maintain and change the electrodes?
What other parameters will operators be able to adjust?
What are the quality and inspection requirements?
What are the relevant production testing methods and test equipment?
Do we have adequate control over the quality of the materials?
Common Problems
During this stage of process development, it is important to understand that the majority of process
problems are related to either materials variation, or part-to-electrode positioning. Some examples are
shown below.
The changes detailed above generally result in a change in contact resistance and always affect the heat
balance of the weld. During weld development these common problems must be carefully monitored so
as not to mislead the course and productivity of the welding experiments.
In summary, the “look see” welding experiments should be used to fix further variables from an
application and process perspective and also to establish a “weld window” for energy, time and force.
This part of weld development is critical in order to proceed to a statistical method of evaluation
(Design of Experiments or “DOEs”). Random explosions or unexpected variables will skew statistical
data and waste valuable time.
Part-To-Part Positioning
Electrode-To-Part Positioning
Material Control
Summary of Contents for 1-288-01
Page 1: ...990 372 REV E DC RESISTANCE WELDING SYSTEM HF28 OPERATION MANUAL...
Page 10: ...HF28 DC RESISTANCE WELDING SYSTEM x 990 372...
Page 64: ......
Page 88: ......
Page 102: ......
Page 114: ......
Page 142: ......