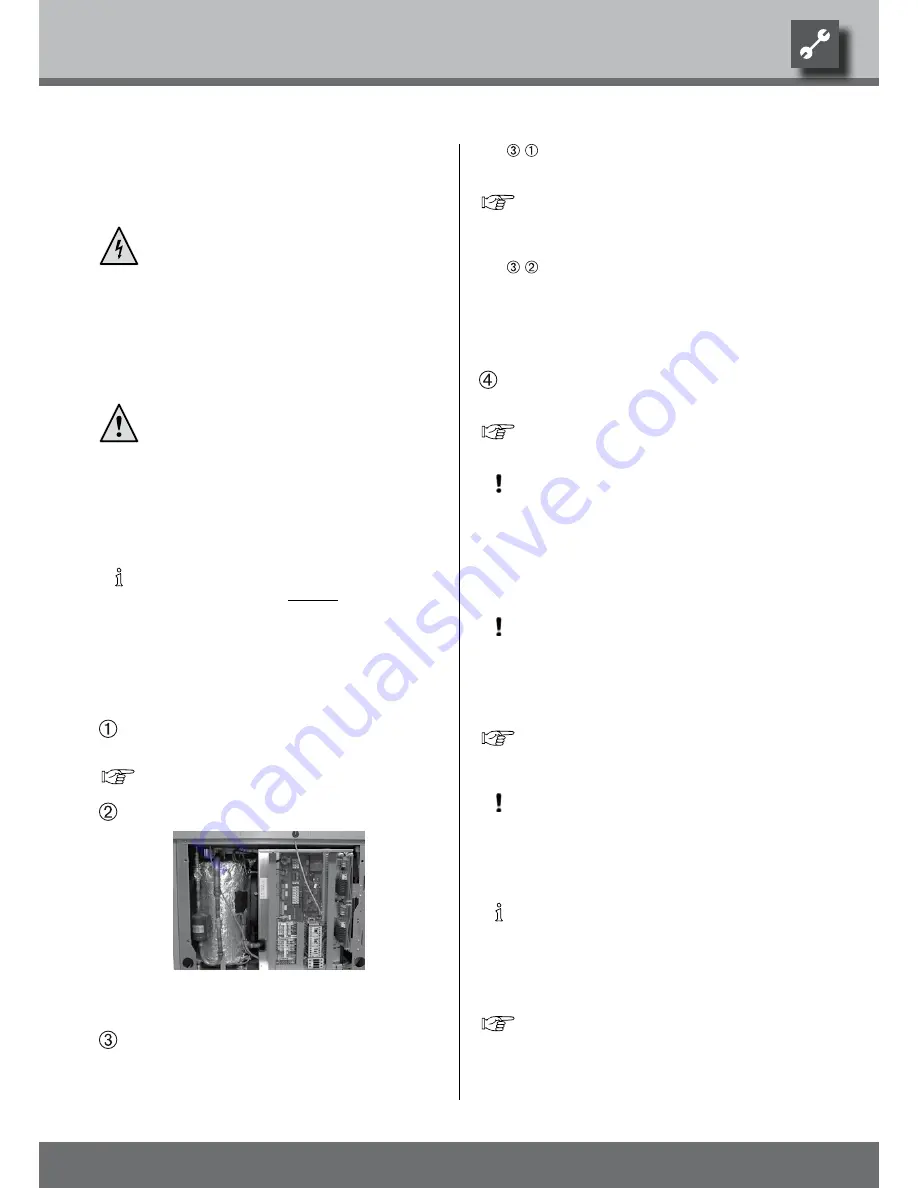
17
We reserve the right to modify technical specifications without prior notice.
83054300dUK
© ait-deutschland GmbH
•
Cut out the rubber sockets on the facing panel…
For positioning of the rubber sockets for insert-
ing the wires, see "dimensional drawing" for the
respective model.
•
Insert the cables through the rubber sockets in the
unit…
The wires inside the unit are guided in a closed wire
duct to the terminals on the switch plate.
Install electric connections according to the termi-
nal diagram that applies to your model…
Terminal diagram for respective model.
ATTENTION
Ensure clockwise rotary field of the load power
supply (compressor).
–
An incorrect rotary field of the compressor
during operation can cause serious, irreparable
damage to the compressor.
ATTENTION
Make sure to equip the power supply of the heat
pump with a 3-pole automatic cut-out with at
least 3 mm contact gap.
Note the level of the release current.
Overview “Technical data / scope of delivery”,
“Electric” section.
ATTENTION
If using the unit in 3~230V systems, please note
that the residual-current circuit breaker (RCCB)
used must be AC-DC sensitive.
ATTENTION
Factory setting for the electric heating element
in units with integrated electic heating elements
is 6 kW (9 kW). It can be changed at contactor
Q5 (Q6) for 2 (3) or 4 kW (6kW).
For further information, see the adhesive label
on the electric heating element.
Electrical connections
Observe the following when performing all work:
DANGER!
Danger of fatal injury due to electric
shock!
Electrical connections may be installed
only by qualified electricians.
Before opening the unit, disconnect the
system from the power supply and secure
it from being switched back on!
DANGER!
Observe the relevant EN-, VDE and/or
applicable local safety regulations during
installation and during all electrical work.
Comply with any technical connection re-
quirements laid down by the responsible
power supply company!
NOTICE.
All live wires must be stripped before they are
installed in the cable duct of the switch cabinets!
POWER CONNECTION
Proceed as follows:
If the unit is closed, open the facing panels on the
operating side…
"Installation".
Open electrical switch cabinet of unit…
Example of open
electrical switch cabinet…
Lead 230 V power cable, power cable for circulat-
ing pumps and cable for external temperature sen-
sor through the rubber sockets on the facing panel
in the unit…