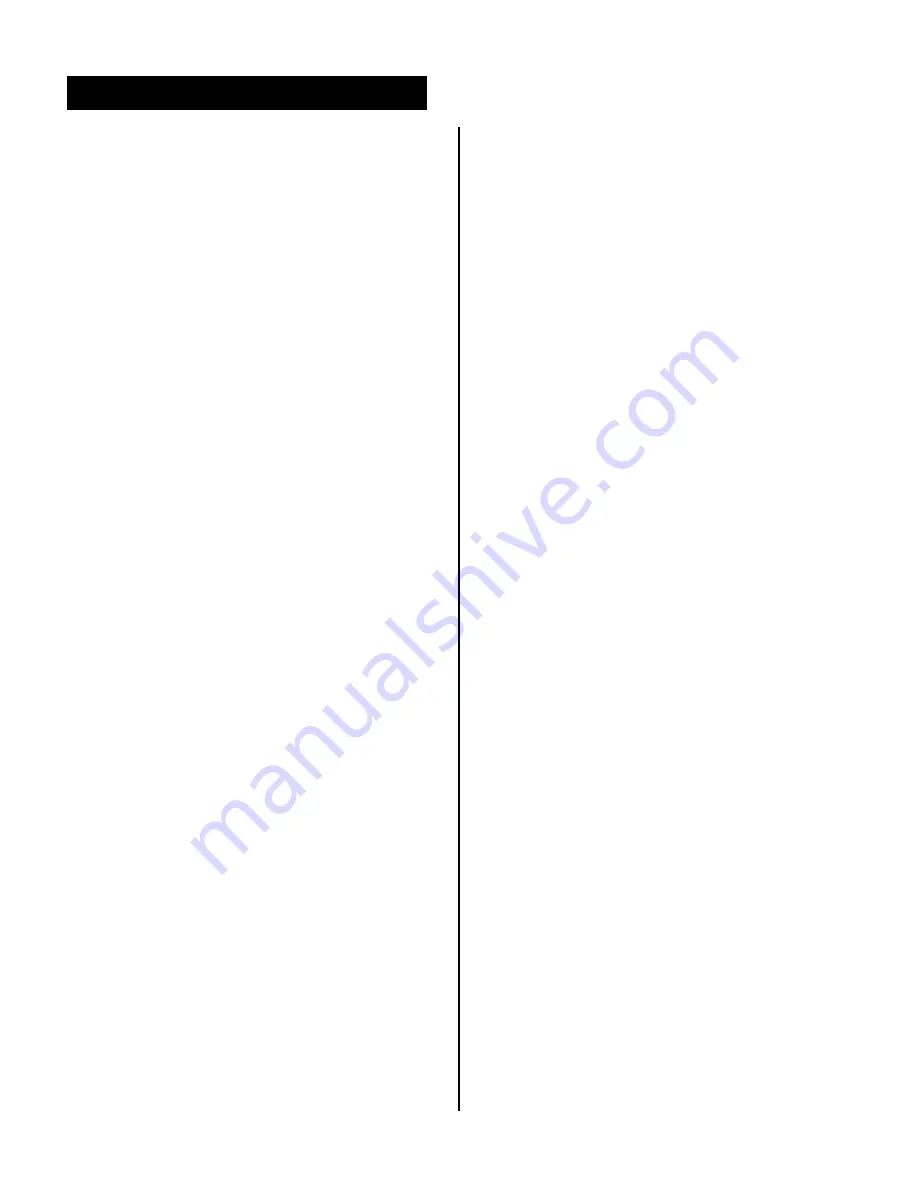
Allied Construction Products, LLC www.alliedcp.com
TM103349_SP1000B_15sep
3
3.0 Warranty Protection Summary
3.1 Overview
The Allied work tool is delivered assembled,
lubricated, and factory tested. Upon receipt of the
equipment, inspect for possible shipping damage.
For new equipment, Allied requires that a Warranty
Registration form be filled out. The form provides a
section for information about the host machine that
the work tool will be installed on. Complete all
sections of the form and return to Allied.
Warranty does not cover failures of the equipment
resulting from incorrect installation, misuse,
alterations by person other than authorized agents,
abnormal operating conditions, use of non-Allied
parts, unapproved service methods, or missed
maintenance requirements.
For details regarding warranty terms and conditions,
refer to document A100668.
3.2 Owner’s Responsibilities
When properly installed, operated and maintained by
qualified personnel, the Allied work tool will remain
productive with a minimum of service.
Keep the Allied equipment operating within its
performance limits by familiarizing yourself with the
specifications provided in the technical data and
specifications tables. Improper installation, including
failure to calibrate the carrier correctly may result in
loss of performance or subject the equipment to
conditions beyond their design.
The following outlines general maintenance policies
required for the Allied equipment. The owner is
strongly encouraged to adopt these general
guidelines and further develop them in order to
manage particular applications and operating
environments.
Ensure that personnel entrusted with installation,
operation, maintenance and transporting of the Allied
equipment adhere to the following:
Read and thoroughly understand the information
and procedures detailed in this manual.
Understand proper operating techniques for all
recommended applications.
Use the Allied attachment only if it is in sound
operating condition. Take prompt action to rectify
any faults that, if left uncorrected, could lead to
personal injury or further damage.
Use the Allied attachment only for the purpose for
which it is intended.
Understand that particular applications, such as
working underwater, will require modifications to
the standard breaker and additional training for
operation and service.
Appoint Who Does What. Ensure that all
personnel understand what their specific
responsibilities include.
1. Establish maintenance responsibilities to be
performed by the OPERATOR.
2. Establish maintenance responsibilities to be
performed by the SERVICE TECHNICIAN.
Recognize problems and know how to take
corrective action as detailed in Troubleshooting
Section 11.
Conduct regular checks and inspections as
scheduled in the Care & Maintenance Section 9.
Allow only qualified operators and Allied trained
service technicians to perform maintenance and
repair as specified in the care and maintenance
schedule.
Use only genuine Allied replacement parts and
recommended lubricants to protect total warranty
coverage.
Maintain written records of equipment
maintenance, service and repair. These records
are helpful if warranty coverage is ever in
question.
Each record shall include at least:
Date of service, maintenance or repair.
Description of the service, maintenance or
repair performed. Include part numbers if
applicable.
Copies of purchase order(s) and invoice(s)
for repair parts and service.
The name and signature of the person
performing the service, maintenance or
repair.
Summary of Contents for Skid-Pac 1000
Page 43: ...TM103349_SP1000B_15sep Notes ...
Page 44: ...TM103349_SP1000B_15sep R ...