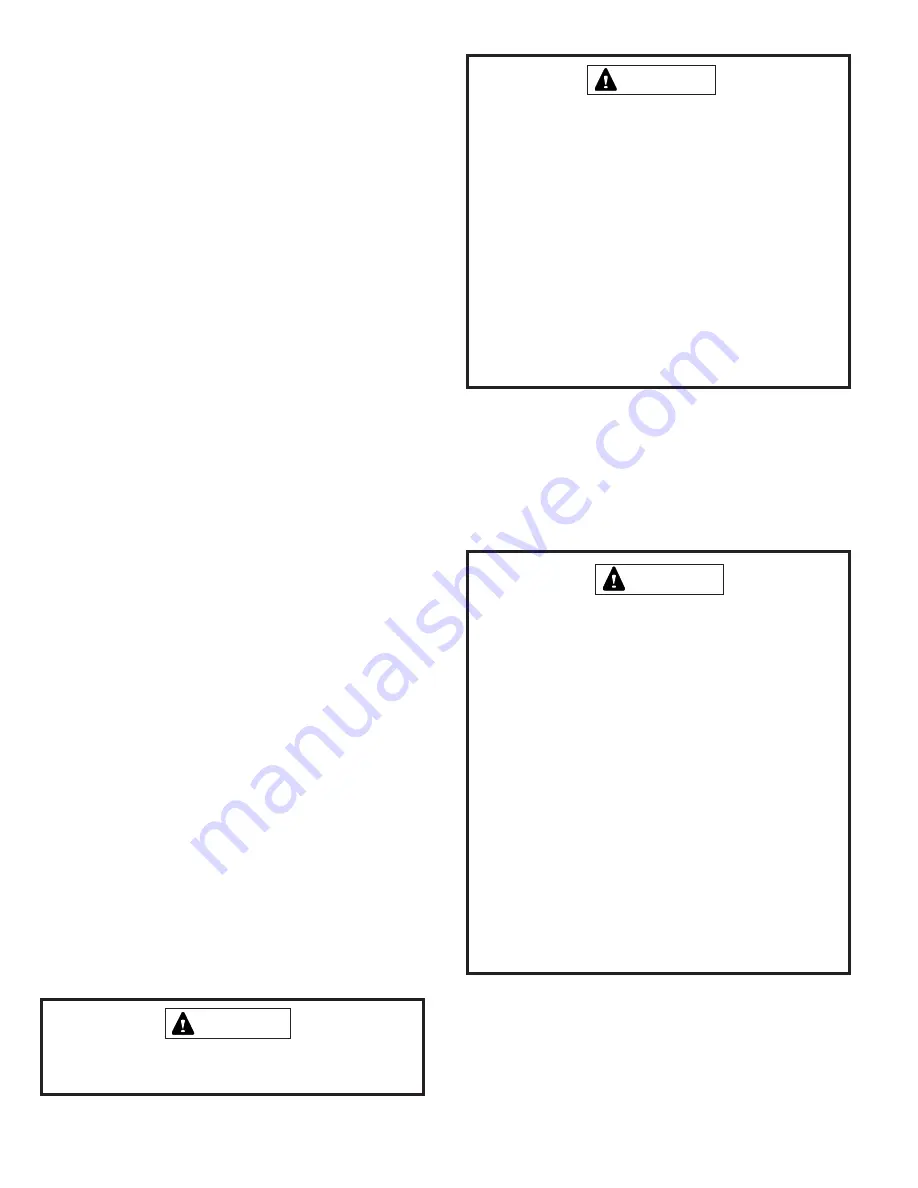
506725-01
Page 6 of 48
Issue 1109
•
Air filters must be replaced upon construction completion.
•
The input rate and temperature rise must be set per the
furnace rating plate.
•
One hundred percent (100%) outdoor air must be provided
for combustion air requirements during construction.
Temporary ducting may supply outdoor air to the furnace.
Do not connect duct directly to the furnace. Size the
temporary duct following the instructions in section for
Combustion, Dilution and Ventilation Air in a confined
space with air from outside.
•
The furnace heat exchanger, components, duct system,
air filters and evaporator coils must be thoroughly
cleaned following final construction cleanup.
•
All furnace operating conditions (including ignition, input
rate, temperature rise and venting) must be verified
according to these installation instructions.
General
These instructions are intended as a general guide and do
not supersede local codes in any way. Consult authorities
having jurisdiction before installation.
In addition to the requirements outlined previously, the
following general recommendations must be considered
when installing one of these furnaces:
•
Place the furnace as close to the center of the air
distribution system as possible. The furnace should also
be located close to the vent termination point.
•
When the furnace is installed in non-direct vent
applications, do not install the furnace where drafts might
blow directly into it. This could cause improper
combustion and unsafe operation.
•
When the furnace is installed in a non-direct vent
applications, do not block the furnace combustion air
opening with clothing, boxes, doors, etc. Air is needed
for proper combustion and safe unit operation.
•
When the furnace is installed in an attic or other insulated
space, keep insulation away from the furnace.
•
When the furnace is installed in an unconditioned space,
consider provisions required to prevent freezing of the
condensate drain system.
NOTE:
The Commonwealth of Massachusetts stipulates
these additional requirements:
•
Gas furnaces shall be installed by a licensed plumber
or fitter only.
•
The gas cock must be “T handle” type.
•
When a furnace is installed in an attic, the passageway
to and service area surrounding the equipment shall be
floored.
Combustion, Dilution & Ventilation Air
If this unit is installed as a Non-Direct Vent Furnace,
follow the guidelines in this section.
NOTE:
In Non-Direct Vent Installations, combustion air is
taken from indoors and flue gases are discharged outdoors.
In the past, there was no problem in bringing in sufficient
outdoor air for combustion. Infiltration provided all the air
that was needed. In today’s homes, tight construction
practices make it necessary to bring in air from outside for
combustion. Take into account that exhaust fans, appliance
vents, chimneys, and fireplaces force additional air that could
be used for combustion out of the house. Unless outside
Insufficient combustion air can cause headaches,
nausea, dizziness or asphyxiation. It will also cause
excess water in the heat exchanger resulting in rusting
and premature heat exchanger failure. Excessive
exposure to contaminated combustion air will result in
safety and performance related problems. Avoid
exposure to the following substances in the combustion
air supply:
Permanent wave solutions
Chlorinated waxes and cleaners
Chlorine base swimming pool chemicals
Water softening chemicals
De-icing salts or chemicals
Carbon tetrachloride
Halogen type refrigerants
Cleaning solvents (such as perchloroethylene)
Printing inks, paint removers, varnishes, etc.
Hydrochloric acid
Cements and glues
Antistatic fabric softeners for clothes dryers
Masonry acid washing materials
WARNING
These units should not be installed in areas normally
subject to freezing temperatures.
CAUTION
Product Contains Fiberglass Wool.
Disturbing the insulation in this product during
installation, maintenance, or repair will expose you to
fiberglass wool. Breathing this may cause lung cancer.
(Fiberglass wool is known to the State of California to
cause cancer.)
Fiberglass wool may also cause respiratory, skin, and
eye irritation.
To reduce exposure to this substance or for further
information, consult material safety data sheets available
from address shown below, or contact your supervisor.
Allied Air Enterprises, Inc.
215 Metropolitan Drive
West Columbia, SC 29170
WARNING