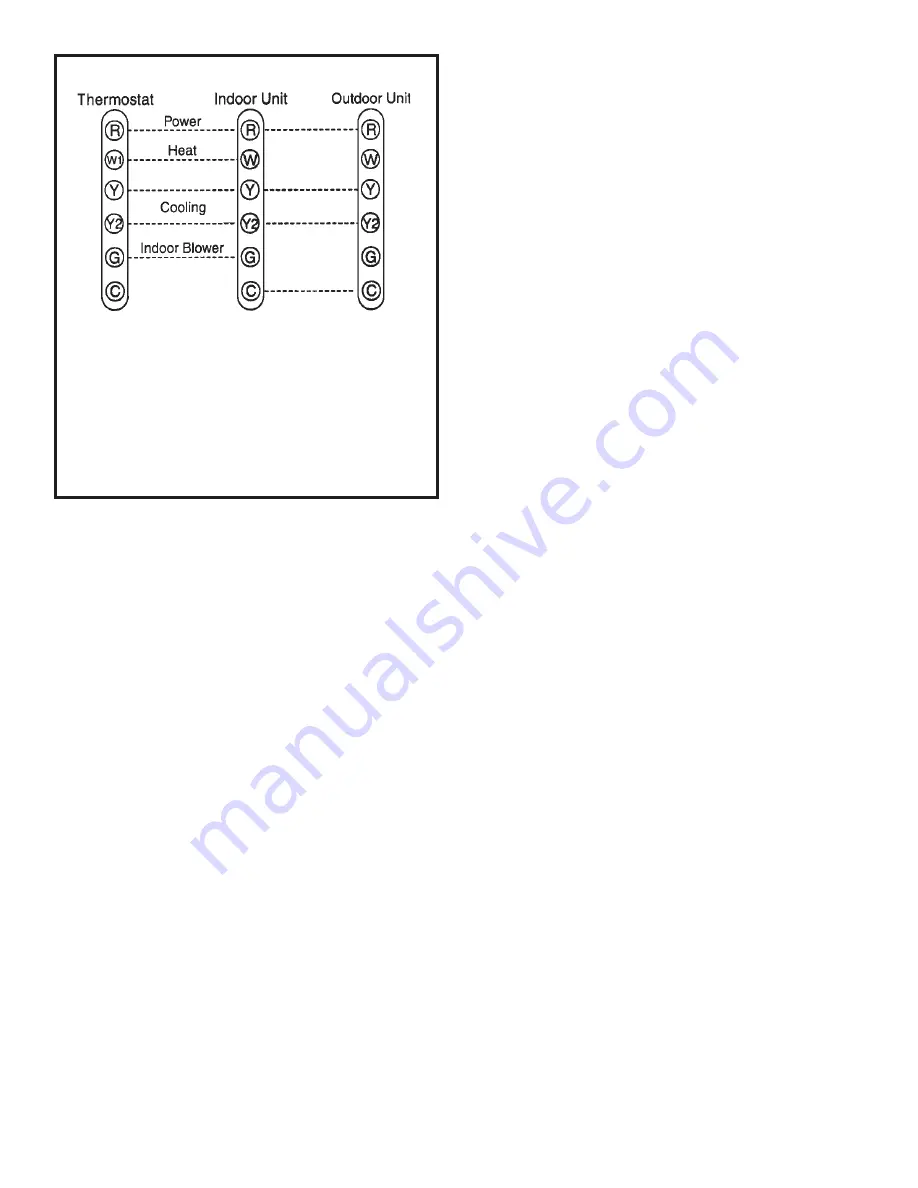
506469-01
Issue 1008
Refrigerant Piping
If the 4AC18LT unit is being installed with a new indoor coil
and line set, the refrigerant connections should be made as
outlined in this section. If an existing line set and/or indoor
coil will be used to complete the system, refer to this section
as well as the section that follows entitled -
Flushing
Existing Line Set and Indoor Coil
.
If this unit is being matched with an approved line set or
indoor coil which was previously charged with R-22
refrigerant, the line set and coil must be flushed prior to
installation. If the unit is being used with and existing indoor
coil which was equipped with a liquid line which served as a
metering device (RFCI), the liquid line must be replaced prior
to the installation of the 4AC18LT unit.
Field refrigerant piping consists of liquid and suction lines
from the outdoor unit (sweat connections) to the indoor coil
(flare or sweat connections).
Select line set diameters from Table 2 to ensure that oil
returns to the compressor. Size vertical suction riser to
maintain minimum velocity at minimum capacity.
Recommended line length is 50’ or less. If more than 50’
line set is required, contact Technical Services. Table 2
shows the diameters for line sets up to 100’ although vertical
lift applications and trapping requirements need to be
reviewed with Technical Services for line sets over 50’.
Installing Refrigerant Line
During the installation of an air conditioning system, it is
important to properly isolate the refrigerant line to prevent
unnecessary vibration. Line set contact with the structure
(wall, ceiling, or floor) may cause objectionable noise when
vibration is translated into sound. As a result, more energy
or vibration can be expected. Close attention to line set
isolation must be observed.
Following are some points to consider when placing and
installing a high-efficiency outdoor unit:
1. Install line voltage power supply to unit from a properly
sized disconnect switch. Any excess high voltage field wiring
should be trimmed or secured away from the low voltage
field wiring.
2. Ground unit at unit disconnect switch or to an earth ground.
To facilitate conduit, a hole is in the bottom of the control
box. Connect conduit to the control box using a proper
conduit fitting. Units are approved for use only with copper
conductors. 24V Class II circuit connections are made in
the low voltage junction box. Refer to Figure 4 for high
voltage field wiring diagram. A complete unit wiring diagram
is located inside the unit control box cover.
3. Install room thermostat on an inside wall that is not subject
to drafts, direct sunshine, or other heat sources.
4. Install low voltage wiring from outdoor to indoor unit and
from thermostat to indoor unit (See Figure 5).
5. Do not bundle any excess 24V control wire inside control
box. Run control wire through installed wire tie and tighten
wire tie to provide low voltage strain relief and to maintain
seperation of field-installed low and high voltage circuits.
Page 4 of 24
Thermostat Designations
See unit wiring diagram for power supply connections.
If the indoor unit is not equipped with a blower relay, one must
be field supplied and installed.
Do not connect C (common) connection between indoor unit
and thermostat except when required by the indoor thermostat.
Refer to thermostat installation instructions. C (common)
connection between indoor unit and outdoor unit required for
proper operation.
Figure 4
Summary of Contents for 4AC18LT Series
Page 16: ...506469 01 Issue 1008 Page 16 of 24 Table 8...
Page 18: ...506469 01 Issue 1008 Page 18 of 24 Table 9 Flash Codes...
Page 19: ...506469 01 Issue 1008 Page 19 of 24 Table 10 Flash Codes cont...
Page 20: ...506469 01 Issue 1008 Page 20 of 24 Table 11 Miswired Module Troubleshooting...
Page 23: ...506469 01 Issue 1008 Page 23 of 24 WIRE DIAGRAM...