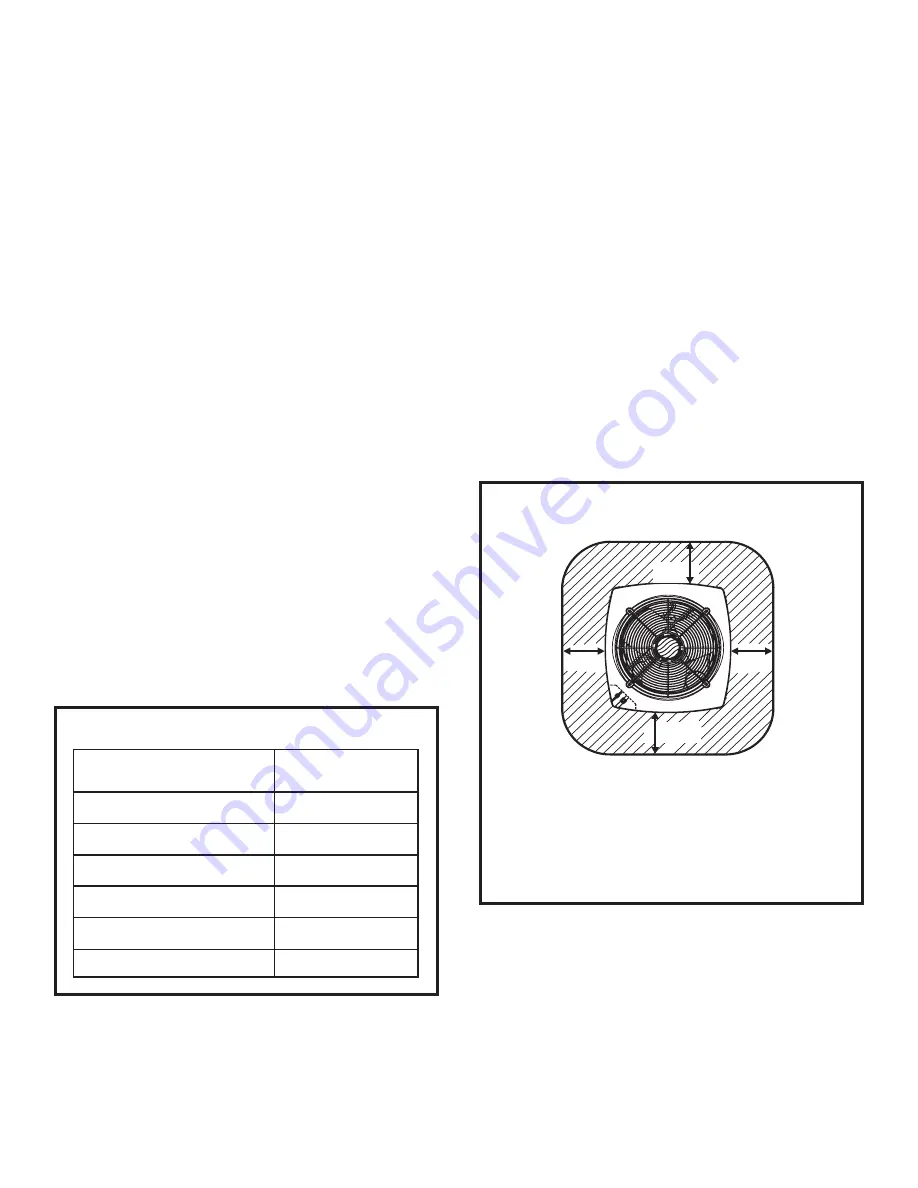
506469-01
Issue 1008
INSTALLATION
When servicing or repairing HVAC components, ensure the
fasteners are appropriately tightened. Table 1 shows torque
values for fasteners.
Inspection of Shipment
Upon receipt of equipment, carefully inspect it for possible
shipping damage. If damage is found, it should be noted on
the carrier’s freight bill. Take special care to examine the
unit inside the carton if the carton is damaged. Any concealed
damage discovered should be reported to the last carrier
immediately, preferably in writing, and should include a
request for inspection by the carrier’s agent.
If any damages are discovered and reported to the carrier
DO NOT INSTALL THE UNIT
, as claim may be denied.
Check the unit rating plate to confirm specifications are
as ordered.
Location of Unit
Outdoor units operate under a wide range of weather
conditions; therefore, multiple factors must be considered
when positioning the unit. The unit must be positioned to
give adequate clearances for sufficient airflow and servicing.
Refer to Figure 1 for installation clearances.
General
Read this entire instruction manual, as well as the
instructions supplied in separate equipment, before
starting the installation. Observe and follow all
warnings, cautions, instructional labels, and tags.
Failure to comply with these instructions could result
in an unsafe condition and/or premature component
failure.
These instructions are intended as a general guide only for
use by qualified personnel and do not supersede any national
or local codes in any way. The installation must comply with
all provincial, state, and local codes as well as the National
Electrical Code (U.S.) or Canadian Electrical Code (Canada).
Compliance should be determined prior to installation.
4AC18LT condensing units use R410A which is an ozone-
friendly HFC refrigerant. The unit must be installed with a
matching indoor coil and line set. 4AC18LT units are
designed for use in expansion valve (TXV) systems only. A
filter drier approved for use with R410A is installed in the
unit.
IMPORTANT:
This product has been designed and
manufactured to meet ENERGY STAR criteria for energy
efficiency when matched with appropriate coil components.
However, proper refrigerant charge and proper air flow are
critical to achieve rated capacity and efficiency. Installation
of this product should follow the manufacturer’s refrigerant
charging and air flow instructions.
Failure to confirm proper
charge and airflow may reduce energy efficiency and
shorten equipment life.
Page 2 of 24
Table 1
Compressor Bolts
90 in. lbs.
#10 Machine Screws
28 in. lbs.
#8 Machine Screws
16 in. lbs.
Sheet Metal Screws
16 in. lbs.
Service Port Caps
8 ft. lbs.
Stem Caps
8 ft. lbs.
Fastener
Torque
Torque Table
Figure 1
Installation Clearances
* A service clearance of 30" must be maintained on one of the
sides adjacent to the control box. Clearance to one of the other
three sides must be 36". Clearance to one of the remaining two
sides may be 12" and the final side may be 6".
A clearance of 24" must be maintained between units.
48" clearance required on top of unit. Maximum soffit overhang is
36".
36” *
36” *
36”
36”
Summary of Contents for 4AC18LT Series
Page 16: ...506469 01 Issue 1008 Page 16 of 24 Table 8...
Page 18: ...506469 01 Issue 1008 Page 18 of 24 Table 9 Flash Codes...
Page 19: ...506469 01 Issue 1008 Page 19 of 24 Table 10 Flash Codes cont...
Page 20: ...506469 01 Issue 1008 Page 20 of 24 Table 11 Miswired Module Troubleshooting...
Page 23: ...506469 01 Issue 1008 Page 23 of 24 WIRE DIAGRAM...